Hackensack University Medical Center builds standalone CUP
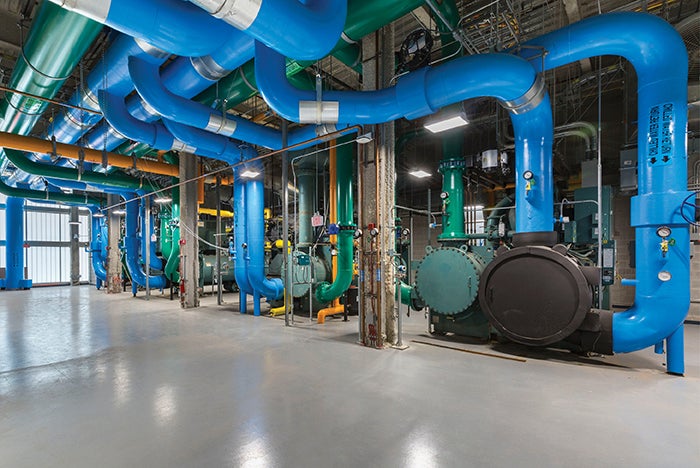
The campus’ new chiller plant consists of six chillers and seven cell cooling towers, which can support 11,000 tons of cooling capacity.
Photo by Kate Glicksberg
Situated in a densely populated urban landscape, Hackensack University Medical Center (HUMC) in Hackensack, N.J., stands as the largest provider of both inpatient and outpatient services in the state. However, the densely packed nature of the campus — which covers a nine-block radius — hindered its ability to expand its essential acute patient care services, particularly for an aging population.
This challenge was exacerbated by HUMC’s aging infrastructure, which struggled to accommodate any expansion efforts or withstand grid failures. Among the concerns, the main electrical service was operating at 90% capacity, while the chilled water system spanned four plants with minimal room for growth. Additionally, four of the five boilers within the steam plant were outdated and costly to maintain, surpassing their life expectancy.
To address these issues, the Hackensack Meridian Health network initiated the design and construction of a new central utility plant (CUP) at HUMC. Completed four years ago — under the guidance of RSC Architects, Hackensack; Page Southerland Page, Houston; Concord Engineering Group Inc., Vorhees, N.J.; Langan Engineering and Environmental Services Inc., Parsippany, N.J.; Reuther + Bowen P.C., Scranton, Pa.; Stantec; and Blanchard Turner Joint Venture LLC, Springfield, N.J. — the 45,000-square-foot stand-alone facility centralizes and modernizes the hospital complex’s energy infrastructure.
“The project team of architects, engineers, contractors and subcontractors worked together collaboratively and meticulously with plant operations and the hospital’s staff to design the new facility, coordinate and phase shutdowns, and relocate and commission equipment within the new plant while keeping the hospital fully operational at full capacity,” says Allen Prinzi, director of plant operations at HUMC. “The intricate ‘infrastructure surgery’ has replaced 100% of the medical center’s steam capacity, 100% of its chilled water capacity and its existing 26-kilovolt (kV) electrical service while increasing its oxygen capacity and garnering several other benefits and savings.”
Smart planning
The implementation of a new 26-kV substation, featuring larger 20 megavolt-ampere transformers and 12 of the campus’ existing 13.2-kV distribution circuits and duct banks, accommodates future expansion and aligns with HUMC’s master plan objectives. It also enhances the hospital’s cooling capacity to 8,800 tons, up from 6,600 tons, by centralizing chilled water production.
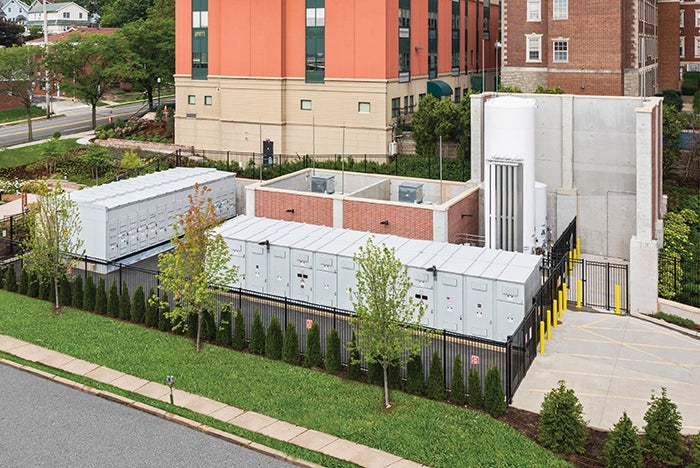
The new 26.2-kilovolt substation, 13.2-kilovolt distribution equipment and 20-megavolt-amperer transformers are now located in a new utility courtyard, along with a new oxygen tank farm, which was designed and landscaped into the hospital’s urban campus, with a new garden on the street corner.
Photo by Kate Glicksberg
Furthermore, the campus has transitioned from five aging dual-fuel boilers, operating at a 70,000-pound-per-hour capacity, to three state-of-the-art, dual-fuel watertube boilers boasting a 180,000-pound-per-hour capacity. These new boilers provide steam for the hospital’s sterilization protocols, ensuring efficiency and reliability. In addition, the installation of three new fixed 2.5-megawatt (MW) generators, surpassing minimum code requirements, offers energy redundancy. This guarantees an uninterrupted power supply to the hospital during emergencies.
“Within the CUP’s new chiller room, four electric chillers and two steam turbine chillers ensure that hospital services can be maintained in an emergency and loss of the grid,” says John Nesbitt, HUMC plant engineer manager. “One new 2,900-ton steam turbine chiller and one new 3,000-ton electrical centrifugal chiller have been installed, and four of the campus’ existing chillers — three 1,500-ton electric centrifugal units and one 1,600-ton steam turbine chiller — have been moved to the new plant. The consolidation and centralization of these 13 existing chillers down to six chillers, as well as from four condenser water systems down to one, reduced plant operations and maintenance expenses.”
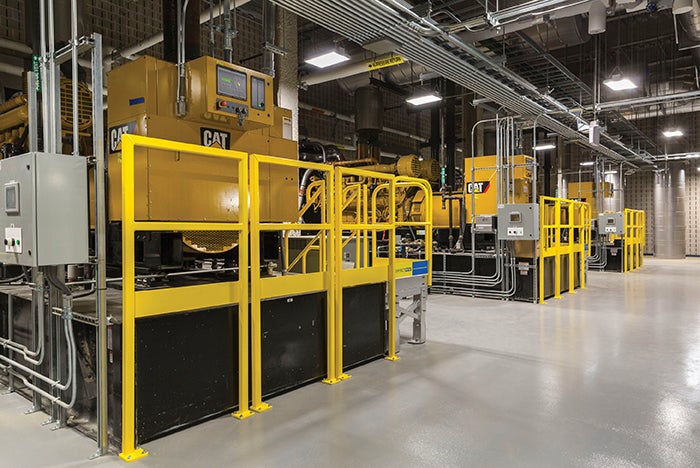
Three new, fixed 2.5-megawatt generators, located in a dedicated space above the plant’s boiler room, are sized over and above the code-required minimum to offer energy redundancy and other advantages.
Photo by Kate Glicksberg
Additionally, quick connects were implemented for the 2-MW rental generators, enabling chilled water generation to reach 93% of the extended load during a utility outage, regardless of the emergency power requirements. With this hybrid configuration, the plant can meet 55% of the anticipated future load of 8,000 tons in an emergency scenario using its steam-driven chillers.
Michael Fischette, PE, CGD, founder and CEO of Concord Engineering Group, notes that the hospital’s steam system also now consists of three 60,000-pounds-per-hour, 125-pounds-per-square-inch-gauge, dual-fuel watertube boilers that supply steam for space heating and the hospital’s sterilization protocols at a 180,000-pounds-per-hour capacity while also providing N+1 redundancy.
A 2022 analysis revealed significant annual savings for the plant, including decreased chilled water costs by 11%, reduced cooling tower costs by 75%, reduced chilled water pumping costs by 50%, enhanced operational efficiency of the electric chiller by 14% and reduced condenser water pumping expenses by 30%.
Significant hurdles
The task of linking the utilities of the new plant, positioned on the opposite side of a public roadway, presented considerable obstacles. Employing ground-penetrating radar, the project team meticulously surveyed the hospital’s 50-year-old underground utilities. Subsequently, logistics plans were devised to manage the utility pathways and traffic flow, followed by the excavation and construction of a trench measuring 40 feet wide by 20 feet deep beneath the roadway and existing infrastructure.
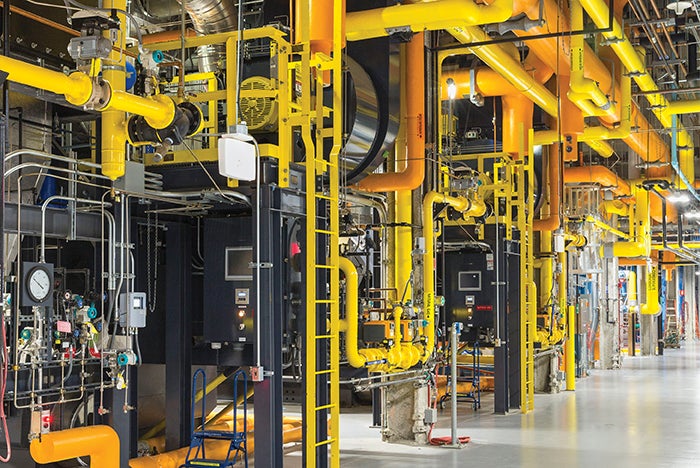
Three dual-fuel watertube boilers make up the 180,000 pound-per-hour steam plant to provide N+1 redundancy and steam to the steam turbine chillers.
Photo by Kate Glicksberg
Also, given the crucial role played by the existing electrical service, oxygen, steam system and chilled water production in sustaining vital hospital functions, prolonged outages were deemed impractical and unsafe. Hence, the team collaborated closely with hospital personnel and plant operations to develop detailed logistics plans, coordinate shutdowns and transitions, and implement adequate safety measures to safeguard uninterrupted hospital operations.
“This massive undertaking was dissected into a total of 12 smaller, separate enabling projects, which were carefully mapped out and phased,” says Erik Polyzou, ACHA, AIA, project manager and project architect for RSC Architects. “An extensive survey was performed by the design team before this work began to inspect the manholes, switchgear, transformers, pull boxes and other related equipment across each system to gain an operational understanding of their interconnections.”
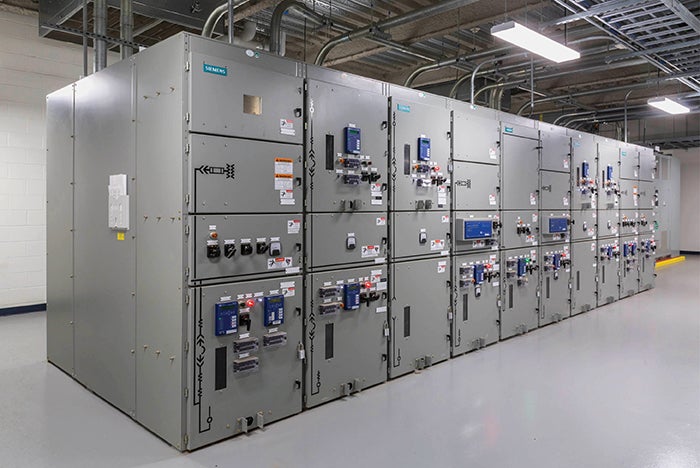
Acoustic silencers were installed to mitigate the noise of the generators
Photo by Kate Glicksberg
Incremental projects included phased strategies that facilitated the seamless transfer of occupants from existing buildings, relocation and feeding of new switchgear and bulk oxygen tanks, and successful phased implementation of chilled water capacity enhancements.
Surpassing standards
The enhancements integrated into the new CUP surpass standard code requirements for resilience, ensuring the hospital’s capability to effectively address patient needs irrespective of utility conditions or unforeseen weather events.
In addition, the project team’s adeptness in configuring tie-in points for the new boilers and steam system enabled simultaneous operation of the new and old plants. This eliminated the necessity for costly or prolonged shutdowns and mitigated potential risks to critical hospital operations. Moreover, operating both plants concurrently provided the plant operations team with an opportunity to undergo training on the new system.
Cohesive collaboration among hospital and operations personnel, architects, engineers and contractors resulted in safe and efficient outcomes.
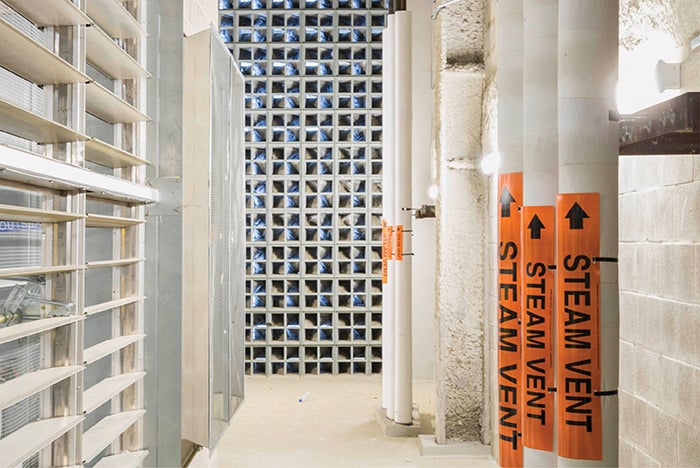
And new substations in the electrical room provide capacity for future upgrades.
Photo by Kate Glicksberg
“The CUP is truly one of a kind and incredibly elaborate in its undertaking and implementation,” says Donald Ferrell, Hackensack Meridian Health’s senior vice president of facilities and construction. “I commend the project team for their execution of this vital project, for supporting HUMC’s vision of transformative patient care and for their service in meeting the evolving needs of the Hackensack community.”
Vista Awards Task Force Chair Randy Regier says the project’s completion underscores the value of careful planning. “The team conducted proper due diligence on underground and overhead investigations to determine the right pathways for services with the least amount of disruption and assessed site conditions to select the best location for the new plant while allowing for future campus development,” Regier says.
Pasquale Avallone, LEED AP, principal at RSC Architects, says it’s gratifying to be recognized with a Vista Award. “It validates the team’s commitment to excellence in design and construction,” he says.
Project Info
- Square footage: 45,000
- Cost: $91 million
- Start date: May 2018
- Completion date: May 2020
Team Members
- John Nesbitt, plant engineer manager at Hackensack University Medical Center, Hackensack, N.J.
- Allen Prinzi, director of plant operations at Hackensack University Medical Center
- Donald Ferrell, senior vice president of facilities and construction at Hackensack Meridian Health, Hackensack, N.J.
- Erik Polyzou, project manager and project architect at RSC Architects, Hackensack, N.J.
- Tushar Gupta, principal and health care market sector leader at Page Southerland Page, Houston
- Michael Fischette, founder and CEO at Concord Engineering Group Inc., Vorhees, N.J.
- Joseph Yannucci, associate principal at Langan Engineering and Environmental Services Inc., Parsippany, N.J.
- Michael Stremski, associate principal and assistant structural department head at Reuther + Bowen P.C., Scranton, Pa.
- Peter Cornet, project executive at Blanchard Turner Joint Venture LLC, Springfield, N.J.