Commissioning matters for energy efficiency
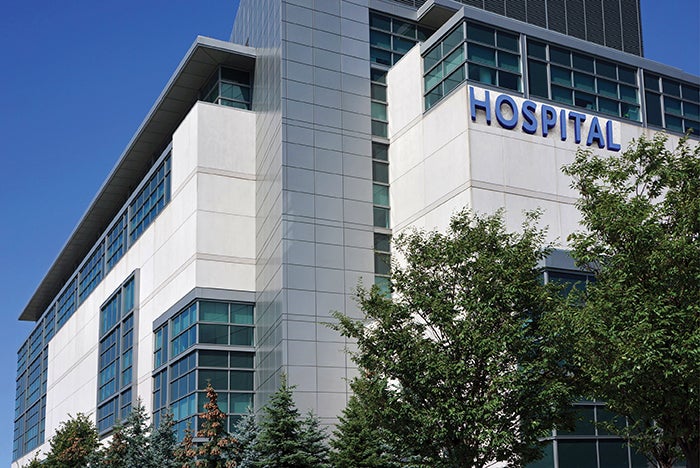
Building enclosure commissioning has become a critical process for verifying that exterior systems perform well, preserving energy efficiency, occupant comfort and indoor air quality.
Image by Getty Images
A well-executed commissioning (Cx) process ensures systems meet the owner’s design requirements, function effectively and align with energy-efficiency goals. This performance-focused, project-specific process instills confidence that buildings, systems and equipment meet the owner’s project requirements (OPRs), current facility requirements (CFRs) and other functional needs. Cx, therefore, plays a significant role in addressing the sustainability concerns that increasingly are shaping the construction industry.
By optimizing heating, ventilating and air-conditioning (HVAC) systems, verifying renewable energy performance and identifying energy waste, Cx contributes to significant energy savings. Furthermore, Cx enhances occupant comfort by ensuring proper ventilation, minimizing drafts and maintaining consistent temperatures. This translates to improved indoor air quality and a more productive environment. Finally, Cx reduces long-term maintenance costs by identifying and addressing potential problems early on, extending the lifespan of building systems and minimizing costly repairs. As more organizations focus on efficient operations and environmental standards, the importance of Cx has grown.
Buildings involve diverse stakeholders with differing priorities — program goals, budgets, maintenance requirements and sustainability targets. The Cx provider (CxP) aligns these goals, bringing all parties toward a shared vision. Working closely with consultants during design, contractors during construction and operations staff at turnover, the CxP ensures the building meets the OPRs and performs as intended.
While functional testing and equipment startups play a role, Cx begins much earlier. Ideally, the CxP joins the project from Day 1 to define the OPRs, a clear, detailed set of goals covering everything from measurable performance standards to training needs and benchmarks. Many mistakenly see Cx as simple testing, an afterthought or another code compliance step. However, the Cx process lays out a comprehensive framework that drives every stage — planning, installation and operation — toward full system integration and consistent performance.
Together, the CxP, construction team and manufacturer’s representative complete functional testing, verifying that systems meet the required responses. If results deviate, they adjust equipment operation to align with the OPRs.
Types of commissioning
New construction commissioning (NCCx) uses a quality-focused process to verify the OPRs and ensure a smooth transition to stable operations. This process confirms project performance through design reviews, construction reviews, functional testing, training and a structured handover to operations.
Existing building commissioning (EBCx) uses a quality-focused process to meet the CFRs of an existing building, its systems or assemblies. This process includes planning, investigating, implementing, verifying and documenting that the facility and its systems operate to meet the CFRs, with a program to sustain these improvements throughout the facility’s life.
EBCx usually involves either recommissioning — reevaluating a building already commissioned — or retrocommissioning for a building never previously commissioned. In recommissioning, existing Cx documentation provides a foundation for the CFRs, while in retrocommissioning, the documentation must be developed from scratch.
Ongoing commissioning (OCx) optimizes and sustains building performance through continuous investigation, analysis and monitoring of building systems. Typically, following NCCx or EBCx, OCx ensures a facility continues to meet both current and evolving requirements. OCx activities occur throughout the facility’s life, with some processes running nearly continuously. In contrast, others appear on a scheduled or as-needed basis.
Monitoring-based commissioning is a methodology for implementing OCx, which enhances building operations by leveraging system or meter data analysis to pinpoint improvement opportunities. This process is typically part of a larger EBCx or OCx project, using energy management and information systems software to help detect and resolve performance issues and streamline fault detection.
Each type of Cx covers various systems, with the most common including mechanical (e.g., HVAC and plumbing), electrical (e.g., power and lighting), enclosure (e.g., exterior walls, windows and roofing) and life safety (e.g., fire alarms, sprinklers and smoke control). As building complexity and standards rise, Cx increasingly focuses on sustainability in addition to functionality.
The value of Cx
One key value of a good Cx process is its proactive nature. It identifies and corrects issues before they become problems. The true value of Cx lies in preventing issues like premature equipment failures, inefficient sequences and expensive maintenance costs. This proactive approach ensures smooth project execution and long-term cost savings, making Cx an invaluable part of any construction project.
The “2018 Commissioning Cost/Benefit Study Findings,” authored by the Building Commissioning Association and Lawrence Berkeley National Laboratory, which can be accessed at bcxa.org/resources/2018-commissioning-cost/benefit-study-findings.html, highlights the substantial savings that seamless Cx offers. The study compares the cost of new and existing building Cx of more than 1,500 buildings, looking at the cost of Cx per area and as a percentage of the construction cost. Then, it compares this to the energy savings and projected payback periods.
Effective Cx is not just about boosting energy efficiency and lowering maintenance costs. It’s also about creating value for all stakeholders. Executives see increased returns through lower life-cycle costs, facilities managers gain more straightforward and efficient maintenance, and frontline staff experience a safer, more comfortable environment. This inclusive approach to Cx ensures all stakeholders feel valued and meet their needs, ultimately supporting sustainability goals.
Enclosure commissioning
Building enclosure commissioning (BECx) has become a critical process for verifying that exterior systems (i.e., walls, windows and roofing) perform well, preserving energy efficiency, occupant comfort and indoor air quality. BECx prevents air leaks, water infiltration and thermal inefficiencies in exterior systems, keeping heat inside during winter and outside during summer, which cuts energy use and improves comfort.
Modern architecture and advanced materials add complexity to building systems and construction sequences. Buildings now use multiple enclosure systems — glazing walls, spandrels, metal cladding, brick and stucco — that meet at challenging points and require detailed outlining of enclosure expectations during pre-design, design review, quality assurance observations and testing. This underscores the importance of addressing enclosure issues before construction ends.
The building enclosure commissioning provider (BECxP) helps develop and review the OPR for enclosures, including tests beyond code requirements. The BECxP also defines the enclosure performance criteria, drafts a BECx specification and performs a technical review of the design for OPR compliance, constructability and industry standards. Then, they follow the project through the construction phase and closeout by submittal review, and inspections to ensure OPR compliance is carried through the closeout stage.
BECx plays a crucial role in enhancing the performance of health care facilities. By minimizing air leakage and improving insulation, BECx reduces drafts and temperature fluctuations, creating a more comfortable and stable environment for patients and staff. By addressing enclosure issues, BECx also optimizes HVAC system performance, lowering energy consumption and reducing operational costs. Furthermore, BECx directly supports infection control by ensuring proper pressure relationships within the HVAC system. This is vital for preventing the spread of airborne contaminants.
Health care facilities, as energy-intensive environments with unique operational needs, require innovative strategies, cutting-edge technologies and interdisciplinary collaboration. BECx is a critical enabling effort, providing a foundation that ties every decision back to sustainability goals.
BECx advantages
The BECx process begins with tying enclosure performance back to the OPRs, ensuring all energy and sustainability goals are clearly defined and aligned with operational needs.
Early involvement of BECx professionals ensures critical enclosure-related decisions are made during the pre-design phase. For instance, determining whether a project will use a closed cavity facade or a triple-pane system, or if the facade is supposed to anchor to a mass timber structure, significantly impacts structural, energy and coordination requirements. These decisions require close collaboration with HVAC and mechanical consultants to align enclosure performance with overall building systems. By addressing these factors early, BECx can prevent costly modifications later in the project.
At the very early stages of a project and guided by the OPRs, the BECxP recommends advanced enclosure technologies that align with the project’s efficiency, budgetary and design goals. By evaluating various systems such as dynamic facades, photovoltaic integration and next-generation insulation, BECx ensures that the selected technologies integrate seamlessly with architectural intent and operational needs while anticipating potential construction challenges.
Advanced enclosure technologies, such as dynamic facades and adaptive systems, are revolutionizing building performance. These systems respond to environmental conditions by adjusting transparency, shading and insulation levels, optimizing energy efficiency and occupant comfort. BECx plays a crucial role in recommending the optimal system based on the owner validating these technologies, ensuring they meet performance standards and integrate seamlessly with other building systems.
The BECxP reviews include reducing air infiltration and thermal bridging, and BECx directly supports sustainability strategies by helping health care facilities transition toward cleaner energy solutions. Additionally, at the start of any project, the BECxP conducts workshops with appropriate stakeholders to understand their past experiences in health care facilities, analyzing energy consumption, operational challenges and successful strategies to create a knowledge base for sustainability efforts.
These insights enable health care projects to learn from past lessons, identifying what works and what doesn’t while addressing challenges such as air sealing or insulation upgrades in existing buildings. By evaluating the enclosure’s sealing quality and identifying necessary upgrades, BECx establishes a solid foundation for energy efficiency. Additionally, BECx is critical in systematically evaluating material choices and their impact on a building’s life cycle. While consultants generally ensure the design meets specifications, the BECxP focuses on material performance verification, ensuring selections meet both sustainability and durability requirements. This includes analyzing the supply chain, life-cycle emissions and potential waste reduction.
BECx also emphasizes real-world performance by testing materials under health care-specific conditions (e.g., an operating room), such as exposure and control of humidity, temperature fluctuations and mechanical stress. These evaluations ensure that materials not only are sustainable but also contribute to the long-term operational efficiency of the facility.
Adequate indoor air quality is a cornerstone of health care operations. BECx ensures this through a combination of advanced diagnostics and proactive planning. Air leakage tests, thermal imaging and blower door evaluations are employed to identify and mitigate potential weak points in the enclosure. While enclosure consultants ensure an appropriate design, the BECx checks for pre-design, design and implementation integrity by validating air barrier performance during construction and post-occupancy phases. This prevents issues such as uncontrolled air infiltration, mold or condensation. By addressing these challenges early, BECx can help create safe and clean spaces that promote faster patient recovery and higher staff productivity, directly contributing to the facility’s operational excellence.
Integrating photovoltaic (PV) panels into building enclosures is a growing trend in sustainable design. PV systems can transform facades and roofs into energy-generating surfaces. BECx ensures these systems are properly integrated into the enclosure design, addressing structural, thermal and aesthetic considerations.
Innovative insulation materials, such as aerogels and vacuum-insulated panels, are pushing the boundaries of thermal performance. These materials offer high thermal resistance with minimal thickness, making them ideal for space-constrained health care projects. BECx verifies the performance of these materials under real-world conditions, ensuring they deliver on their promises.
Health care facilities face growing challenges from extreme weather events, such as hurricanes, floods and heat waves. The BECx can help fortify building enclosures against these threats, ensuring they remain resilient in the face of environmental stressors. This resilience reduces the risk of service disruptions, protecting critical health care operations during emergencies.
BECx encourages the adoption of innovative materials and construction techniques that enhance enclosure performance. From advanced insulation systems to dynamic facades that adapt to changing environmental conditions, BECx drives innovation that benefits the health care sector and the construction industry. These advancements contribute to developing next-generation facilities prioritizing efficiency and occupant comfort.
Through its emphasis on durability and efficiency, BECx promotes responsible resource use across the construction and operation of health care facilities. By minimizing waste, conserving materials and reducing energy consumption throughout the value chain, BECx aligns with global efforts to build a more sustainable and equitable future.
A powerful tool
Cx protects stakeholders’ investments, strengthens operational resilience and supports sustainability targets. Its benefits — reduced energy use, prolonged equipment life, lower maintenance costs and improved comfort — make it a powerful tool for achieving long-term value and performance in any facility.
BECx will remain an essential tool for meeting efficiency and resiliency goals and shaping a more sustainable future for the physical environment.
By complementing and elevating the role of building enclosure consultants, BECx provides a robust framework for achieving long-term operational excellence and environmental stewardship.
Related article // The roles of third-party experts in building enclosure reliability
A building enclosure consultant provides specialized engineering knowledge on designing and constructing a building’s exterior envelope, including walls, roofs and windows, to ensure proper air, water and thermal barriers. Their expertise extends to the effective integration and continuity of these exterior design elements.
The building enclosure consultant provides expertise to create sustainable enclosures by applying structural engineering, materials science, physics, construction and architectural principles to new and existing buildings. They also focus on ensuring the enclosure meets aesthetic and functional goals, balancing sustainability with visual appeal.
Typically, these consultants are part of the design team hired by the owner to provide input, and their role starts after the design team has created the basis of design (BOD) for the project. They collaborate with architects and engineers to refine design details, ensuring constructability and long-term performance.
In contrast, the building enclosure commissioning provider (BECxP) acts as an impartial third party hired by the owner. Their role starts much earlier by creating an owner’s project requirement (OPR) prior to the BOD. (Click on the image to the right to see a sample OPR.)
The design team then incorporates the OPR as part of the BOD for enclosure-specific items. BECxPs validate that the design and construction of the building enclosure and its performance meets the OPR across the various stages of the project. This is achieved through design review, inspections and testing throughout the construction process. Their scope often extends beyond closeout and includes training facilities staff on proper enclosure maintenance, helping collaborate on detailed operations and maintenance manuals, and conducting 10-month warranty walks to identify and address any performance issues before the end of the warranty period.
Compared to a consultant’s limited focus, a BECxP’s focus is on performance validation — starting with the OPR until the warranty walk. BECxPs are experts in building science, scientific performance, analysis and testing.
By clearly defining these roles, building owners can make informed decisions and assemble a team best suited to achieving their project goals. This helps prevent miscommunication and ensures both roles contribute effectively to the project’s success, ultimately supporting long-term efficiency and durability.
About this article
This article was contributed to Health Facilities Management as part of a collaborative arrangement between the American Society for Health Care Engineering (ashe.org) and the Building Commissioning Association (bcxa.org).
Nicole Imeson, PL(Eng.), P.Tech.(Eng.), is mechanical engineer and principal at Vertica Engineering in Calgary, Alberta; Neha Verma, Assoc AIA, BECxP, CxA+BE, is branch manager for building enclosure services at ECS Florida LLC; Peter Nabhan, PE, PMP, LEED AP BD+C, is senior national practice leader for health care at the ECS Group of Companies in Chantilly, Va.; and Liz Fischer is executive director at the Building Commissioning Association in Portland, Ore. They can be reached at nimeson@verticaeng.ca, nverma@ecslimited.com, pnabhan@ecslimited.com and lfischer@bcxa.org.