COVID-19 and construction costs
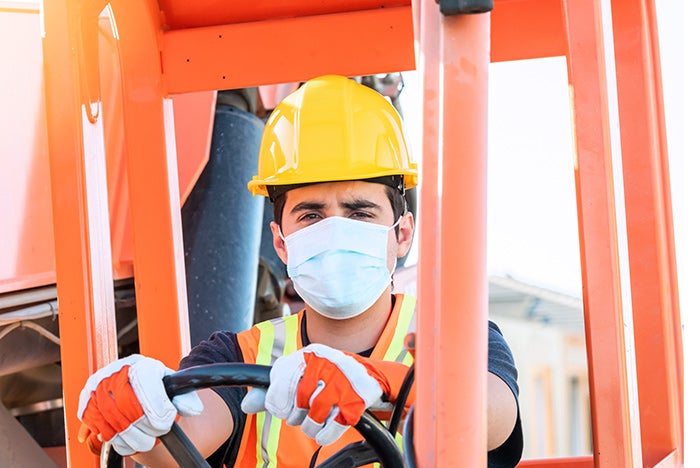
Health care construction professionals continue to grapple with cost increases as a result of the pandemic.
Image from Getty Images
The COVID-19 pandemic had an unprecedented effect on health care all over the world. From dealing with unknown patient treatment and isolation procedures to basic staffing shortages (e.g., nursing, transport, environmental services and others). Difficulties also included personal protective equipment pricing increases and supply shortages.
However, hospital operations were not the only area to feel the pressure of labor shortages, demand increases, supply shortages, pricing increases and delayed deliveries. The overall construction market (i.e., commercial, institutional and residential) continues to face the same challenges.
When the COVID-19 pandemic initially hit the U.S. in early 2020, all markets clinched down on their financial capital spending and shut down almost all construction projects that were in design and preconstruction phases. This financial move, based upon the unknown but forecasted possible future market instability, forced contractors, subcontractors, suppliers and manufacturers into survival mode with limited spending on both labor and materials.
Although most active construction projects were to remain in progress and on track to be finished, any project that was not in an active phase was pushed to the back burner while businesses focused on survival during an unpredictable time. This would include projects in design, preconstruction and even projects with executed contracts but on which the construction had not started.
Reducing the amount of projects forthcoming created a lower demand on both material and labor. The lower demand on materials and labor forced several manufacturers and suppliers to downsize on labor and minimize additional manufacturing for backlog of material storage. With the active projects utilizing manufactured backlog, new supplies were not being created.
The shutdown of construction was not permanent. Many health care organizations were eventually able to stabilize secondary to the ability to treat COVID-19, the release of vaccines and release of CARES Act funding. This stabilization allowed construction projects to be released again, creating a new demand for both labor and materials, almost all at once.
However, one of the many challenges the market did not anticipate was the release of Federal Pandemic Unemployment Compensation (FPUC) and Pandemic Emergency Unemployment Compensation (PEUC) programs that fall under the CARES act.
According to the FPUC program, “FPUC was a flat amount given to people who received unemployment insurance, including those with a partial unemployment benefit check. The original amount of $600 was reduced to $300 per week after the program was extended in August 2020, as long as [your] state signed the agreement as of Dec. 26, 2020. But the benefit then expired on Sept. 6, 2021, after it was extended by the American Rescue Plan.”
A look these programs include:
- FPUC: Provided a federal benefit of $300 a week up to Sept. 6, 2021.
- PEUC: Extended $300 per week benefits for up to 53 weeks until Sept. 6, 2021.
- Pandemic Unemployment Assistance: Extended benefits to self-employed, freelancers and independent contractors.
This provided common laborers additional financial stability on top of the standard unemployment already received. Many people who would occupy lower-level labor positions were able to obtain greater financial compensation under unemployment than if they were to return to work.
This forced the manufacturing industry to either raise compensation and reflect increases in the pricing of material, or to lower the number of manufactured products due to labor shortages. Even aside from competing wages with unemployment, suppliers faced challenges with labor production due to illness, quarantine and required care in the home for children not attending school or family members who fell ill.
Simple economics tells us the law of supply and demand will always have direct effects on market prices. Although the quantity of construction projects has increased from the initial downturn at the beginning of the pandemic, the supply chain does not have the labor to keep up with the product demands. When there is a decrease in quantity supplied, but no change in demand, the price point of equilibrium increases:
The costs are subsequently passed onto the project owner as part of the bidding process. As noted by the Associated General Contractors of America (AGC) Construction Inflation Alert (2021), construction cost rose nearly 13% from April 2020 to February 2021 in building materials, but project bids did not reflect the increased cost. This increase is 10% percent higher than the average 3% yearly inflation prediction included in most construction project bids:
Further complicating pricing increases, the AGC reported the price of polyvinyl chloride (PVC), used in electric utility work, has increased over 270% from March 2020 to March 2021. The price increase was a direct result of an extreme winter weather condition in Texas that put a PVC production facility out of commission. PVC is a component used for manufacturing multiple product lines but, in construction, its uses are best known for manufacturing windows, cabling, piping, roofing, siding, flooring and even the glue for particles and layers of plywood and oriented strand board (SOB).
The following chart provides the Bureau of Labor Statistic depiction on U.S. construction material cost increases from June 2019 (beige bars) to June 2020 (gray bars) and June 2021 (black bars):
In the 2020 construction market, material costs did increase from 2019, but do not compare to the increased cost of those in the 2021 market. Among the major material cost increases was wood products, hardware, and copper. Labor shortages in the supply chain is one of the major driving forces behind these increases.
According to sources at two local reputable general contracting firms, subcontractor bids are being qualified to have a 30-day bid pricing hold unless unforeseen material escalation affects the price prior to contracting and material purchase. Prospectively, when contractors and subcontractors are awarded a project that has an extended schedule (i.e., 1 to 2 years) they are forced to lock in the price on the bid date.
Prior to the pandemic, the contractors could add a price escalator of 3% per year ratio or supplier material holds to ensure the material price escalation was covered within their bid, depending on when their scope fell within the project schedule. However, with the instability of the supply market price, subcontractors are no longer able to guarantee pricing as they had in the past.
One alternative is to purchase materials and store them until the scope of work is required by the schedule. This would guarantee the material was purchased at bid-day prices, however, the cost of storing the materials will also be passed on to the project owner at bid time.
As the quantity of construction projects continues to increase, so will the demand on construction supplies. With material supplies depleted and labor shortages continuing, construction cost will continue to rise as the market establishes a new equilibrium price point. Owners will need to continue projecting project cost escalations until the labor crisis is resolved and material supplies are replenished.
Chris Harmon is director of facilities, construction and renovation at Baptist Memorial Health Care Corporation.