Building for energy efficiency
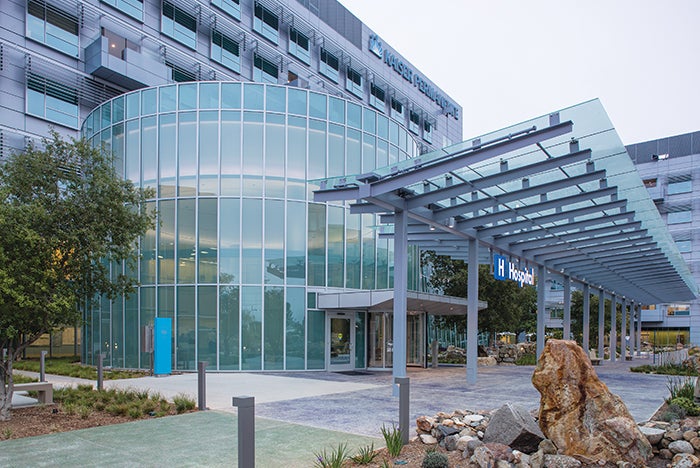
Kaiser Permanente San Diego Medical Center was the first LEED Platinum for Healthcare-certified hospital in California and has earned an ENERGY STAR rating of 90-plus points.
Image courtesy of Kaiser Permanente
The energy efficiency of the nation’s most important health care facilities begins with design. Design impacts the way the buildings are sited and laid out, the materials they use, the way they are sealed, their energy and water conservation, and their alternative energy use.
“The best time to initiate many sustainability initiatives is during the design process,” says Kara Brooks, LEED AP BD&C, sustainability program manager with the Chicago-based American Society for Health Care Engineering (ASHE).
“A project that is planned with sustainability in mind is naturally going to get better results than if sustainability projects are tacked on afterward. Planning for energy savings during early design helps ensure that sustainability is top of mind.”
In the following pages, Health Facilities Management examines the design features of some of the most energy-efficient health care facilities across the country.
Kaiser Permanente, San Diego Medical Center
Opened in April 2017, the medical center is 617,215 square feet in size. It opened with 253 licensed beds and 68 beds shelled for future expansion. The emergency department capacity is 39 beds. The medical center’s specialties include surgical specialties, emergency department, maternal child health services, intensive care unit, interventional radiology, neonatal intensive care and urgent care.
It’s difficult to quantify actual cost savings due to changing commodity costs and other variabilities such as demand charges, says Stephen McKnight, director of facilities operations at the medical center. However, it is estimated that the medical center uses approximately 17-30% less electrical energy than similarly sized medical centers within the Kaiser Permanente portfolio, McKnight says.
Kaiser Permanente San Diego Medical Center was the first LEED Platinum for Healthcare-certified hospital in California and has earned an ENERY STAR® rating of 90-plus points. Those instrumental in the operation of the medical center are pursuing a LEED award for existing building operation and maintenance (EBOM). If a Platinum-level certification for this award is received, the center may be the first hospital in the world to earn double LEED platinum for both building design and construction, and EBOM.
“This is a major feat and would demonstrate Kaiser Permanente’s excellence in not only delivering a phenomenal project, but also operating it,” McKnight says.
Building a new medical center from scratch provides opportunities to incorporate certain design elements that would not be possible, or far more difficult, when retrofitting an existing hospital. By designing San Diego Medical Center with the most sustainable solutions in mind from the very beginning, the hospital could be completed ahead of schedule and under budget.
The facility features an on-site 650kW tri-generation power plant recovering 210 tons of free cooling and 1,700kBTU of free heating resources. Its chilled beams in non-ICU patient rooms, corridors and nurse stations reduce need for system airflow and heating.
The medical center’s 1,560 installed photovoltaic panels generate 345kW, or 3% of its annual energy needs. Its 100% LED lighting consumes less energy and is cooler to run, cutting HVAC cooling needs. Exterior architectural shading features reduce cooling energy use by up to 64% in peak conditions. “The lighting control system also improves the indoor environment by allowing natural daylight harvesting, customized sequences and dimming to meet patient and staff needs,” McKnight says.
The medical center, whose primary materials are steel and concrete, uses prefabricated aluminum curtain walls to create the exterior skin, providing an energy-efficient building envelope and barrier from a nearby air field’s noise.
The medical center’s site uses native planting materials to minimize irrigation. Zero blowdown cooling towers operate upwards of 70 water cycles with validated savings of more than 5 million gallons of fresh water yearly.
Low-flow plumbing fixtures inside the building and mechanical cooling of some equipment reduce the amount of water used on the campus, according to McKnight.
“The site and buildings were designed to enhance the healing environment by creating an atmosphere that does not feel like an institution,” he says. “From the moment you arrive on campus as a visitor or a patient, you do not feel like you are at a hospital. The gardens, areas of respite, meditation room, artwork, lighting and other features create an overall relaxing and inviting environment.”
Health Education Campus, Cleveland Clinic Main Campus
The Sheila and Eric Sampson Pavilion is the centerpiece of the Health Education Campus of Case Western Reserve University and Cleveland Clinic, which was dedicated on April 17, 2019. It is a 476,000-square-foot building featuring an 80-foot-high, 27,000-square-foot central courtyard.
Designed by London-based Foster + Partners, the Health Education Campus on Cleveland Clinic’s main campus in Cleveland was originally considered as four buildings, those being two schools of medicine, a school of dental medicine and a school of nursing.
The design that emerged brought all four under one roof, cutting by 25-30% the footprint originally envisioned, says Chris Connell, Cleveland Clinic’s chief design officer. “This is a stage where many projects don’t even get the designer involved,” he says. “The first question is how much do you need to build, and can you create efficiencies and build less?
“Secondly, how can you create a volume that responds to that as efficiently as possible? We turned an external courtyard into an internal courtyard, and the roof of that was much less area than four elevations of curtain wall. By just making that central courtyard internal, we were able to eliminate three of the four internal circulation routes, and also use one HVAC system, reducing materials and cost.”
The internal courtyard created a central living room for the building, around which are placed study and tutorial spaces, “functionally more efficient and, from a design standpoint, a more elegant and interactive space,” Connell says.
The central courtyard is shared by all who work and study in the building. The courtyard space is heated and cooled, but not to the same extent as the interior spaces.
The first 8 feet off the floor of the courtyard benefit from radiant heating and displacement cooling. “That’s very efficient,” Connell says. “At the top of the building, we use chilled beams, an efficient way of conditioning the top floor. It also gives people a greater amount of individual control.”
Interior walls are painted white to maximize the positive impact of natural light. “The more natural light you get, the less artificial light is needed, the better people feel and the less eye strain they experience,” Connell says.
The building’s external finishes include “good quality, energy-efficient double glazing,” Connell says. Shading is incorporated on the building’s southern but not northern face. Internal materials include granite and natural oak “that feel natural [and have] positive qualities in terms of wellness,” he says. An overhanging roof extends over the entire exterior of the building, shading the top three floors of the four-floor building.
“It provides a better experience inside, because there’s less glare, and it takes the sun off the building much of the year but allows a low winter sun to warm the building,” he says. The building is also sited on the 11-acre site to allow indirect light to reflect into the building off the snow in winter, “even on quite dull days,” he says.
Water conservation in Ohio can be challenging and depends partially on what systems are available within local infrastructures, Connell says.
Designers of the Health Education Campus chose to incorporate stormwater storage on-site to better control how much water travels into the stormwater system. Lawn was chosen as a covering for much of the site to allow rain and snow to penetrate the grass and dissipate naturally. “Covering the site with hard landscaping or parking would make water runoff more difficult and complex,” he says.
Indiana University Health, Bloomington, Ind.
When complete, Indiana University Health (IU Health) Bloomington will be an approximately 600,000-square-foot hospital featuring about 200 beds. Ground was broken earlier this year, and construction is slated for completion in 2021. IU Health Bloomington is intended to replace an existing hospital that remains operational.
The building envelope features “good-quality glass” to ensure good performance, says Fred Betz, building performance consultant with Madison, Wis.-based Affiliated Engineers Inc. The selected glazing has a low U-value and solar heat gain coefficient to manage heat loss and gain. That permits building mechanical systems to be sized and operated efficiently.
“It’s not only designed but installed and commissioned properly,” Betz says. “We have an envelope commissioning agent. Commissioning agents for mechanical and electrical systems are very common, but less so for envelopes. This really allows us to ensure the building is designed and constructed well.”
As for alternative energy features, Betz reports per ASHRAE 189.3-2017, infrastructure is in place to add a 450kW DC photovoltaic array, enabling the owner to be flexible and rapidly add renewables on-site “once the economics are sufficiently favorable,” Betz says.
R-30 roofing and well-insulated walls reduce peak heating and cooling loads as well as energy consumption, Betz says. The roof features a light color in order to further minimize cooling loads during the summer months.
Water efficiency has been applied throughout the facility, not only via traditional approaches with low-flow fixtures, but also in process equipment.
Closed-loop cooling systems for sterilizers, efficient kitchen equipment, native and adaptive plant species, heat recovery chillers, minimization of steam systems and cooling towers with drift eliminator and an efficient water treatment protocol collectively substantially reduce the water consumption of IU Health Bloomington.
The design incorporates a 180-ton heat recovery chiller and a very high-efficiency central energy plant, from which the facility will be both heated and cooled. The entire heating plant operates at low temperatures of about 130 degrees. “Normally, heating systems are about 180 degrees, which leads to energy inefficiencies,” Betz says. ”Our preheat, reheat and perimeter heat are all low temperature.”
The humidification is also novel for health care. “We are using a system called adiabatic humidification, [which] allows us to use the lower-temperature heating system along with high-pressure water to provide humidification rather than the high temperatures that go hand-in-hand with steam systems … It’s only been allowed in health care for a couple years.”
Total energy wheels are featured for air side heat recovery throughout the hospital, Betz says. A total energy wheel is a round device made of materials that temporarily store heat and moisture, and sits within an air handling unit. Some heat and moisture is recaptured in the wheels from indoor air being expelled. That stored heat and moisture is then used to heat and humidify air being brought in from outside.
“One of the things I like about this building is that it’s very comprehensive in its approach to energy efficiency,” Betz says. “Many hospitals will include two or three energy-efficiency technologies. And in this hospital, we’ve incorporated dozens.”
IU Health is committed to the continued exploration and pursuit of providing the highest level of care in its health care facilities, says Kyle F. Hardie, director of south central region design and construction for Indiana University Health in Indianapolis.
“Our commitment to targeting ASHRAE 189.3 is to ensure that IU Health provides the greatest opportunity to fulfill our commitment to improving the health of Indiana,” he says. “ASHRAE 189.3 is one means to measure our success in designing a fiscally sustainable health building. IU Health is in the process of completing its first project with the target of ASHRAE 189.3 and looks forward to sharing future modeling. IU Health is committed to improving the health of Indiana through clinical care, research and the built environment. Sustainable design will influence the behaviors, community and environments of the Hoosier State and help Indiana become healthier.”
Baptist Health Medical Center, Conway, Ark.
Baptist Health Medical Center is a single-building facility that opened in July 2016. An expansion of one wing created the women and children’s addition, completed in mid-2017. The medical center measures 260,000 square feet and includes 110 beds. It has an ENERGY STAR score of 81, one of the highest of any health care facility in Arkansas.
“From the beginning, when the owner, architects and engineers formed a collaborative team, the goal was to design a high-performing and very energy-efficient health care facility that [would] be ENERGY STAR certified,” says Hamid Habibi, mechanical engineer for the facility management department.
“With that goal in mind, the design team made every effort to exceed all the requirements of ASHRAE 90.1 for energy-efficiency standards and adhere to the ‘Advanced Energy Design Guide for Health Care Facilities,’ developed by ASHRAE to achieve 30% reduction in energy consumption from ASHRAE 90.1 standard.”
The hospital was designed and constructed with a very efficient roof and wall as well as very efficient glass for windows, Habibi says. The roof, wall and glass exceeded the requirements of ASHRAE 90.1 standards. All indoor lighting was designed with LED light, providing energy efficiency as well as high indoor lighting quality. Also included was lighting control management for scheduling and monitoring.
The following features were included in the HVAC system for the hospital: variable speed, high-efficiency chillers; variable primary chilled water system, with 14 degrees Delta T; very robust chilled water system with sequence of operation to maximize chilled water system efficiency; high-efficiency boilers for heating water with heating water reset temperature based on ambient temperature; and air handling units with fan-array technology and direct drive fans with variable frequency drives.
Also featured are an air handling unit sequence of operations incorporating temperature and static pressure reset control to maximize energy efficiency; occupied/unoccupied features for operating rooms, C-section rooms, cath labs and procedure rooms to reduce air changes per hour when the spaces are unoccupied; a Type III desiccant wheel for the surgery air handling unit to provide required relative humidity control more efficiently; and a full building automation system for the entire facility to control and monitor HVAC systems, plumbing systems and medical gas equipment as well as lighting monitoring.
“The heating hot water system consists of a high-efficiency gas-fired water heating system, and all plumbing fixtures were selected with low-flow features to reduce water consumption,” Habibi says. “The entire staff of facility management was educated and trained about all aspects of the electrical and mechanical systems for the hospital. The staff also had building automation system training to enable it to troubleshoot and problem solve. This is one of the most important factors that enabled Baptist Health Medical Center – Conway to sustain energy saving and maintain an ENERY STAR rating.”
Memorial Hermann Cypress Hospital, Cypress, Texas
Houston’s Memorial Hermann Health System, a not-for-profit health system in Southeast Texas with 6,400 affiliated physicians and more than 26,000 employees, owns and operates 14 hospitals and has joint ventures with three other hospital facilities.
Its newest acute care campus, Memorial Hermann Cypress Hospital in Cypress, Texas, a 391,000-square-foot, 105-bed facility, opened in March 2017. Last year, within 13 months of its opening, the hospital received an ENERGY STAR 100 percentile ranking. Within 30 days of that award, Memorial Hermann Sugar Land Hospital in Sugar Land, Texas, a hospital renovated in 2016, also achieved ENERGY STAR 100.
Vice President of Facilities Engineering Michael Hatton attributes the score to “relentlessly focusing on quality control during the design and construction process, follow-up commissioning focused on HVAC controls or building automation systems, and the focus by key facility team members on achieving the ENERGY STAR 100 goal.”
The building envelope was designed to reduce the risk of building leaks during Gulf Coast storm events.
Quality control details included two independent precast sealant layers, quality control of precast panel assembly at the factory and as part of the construction phase, and spray chamber testing of difficult as-built window wall and precast details during the construction phase.
Also utilized were sealant inspections and pull tests to document proper adhesion of sealants and regular job observations by a third party during key phases of the exterior skin installation and completion. Similar processes were used on roofing assemblies and flashing details to ensure compliance with energy codes.
LED lighting is used to improve energy efficiency and kilowatt usage. The hospital uses pretreated outside air, equipped with heat recovery to better control temperatures and humidity in operating rooms and other patient care areas, Hatton says.
Reducing overall cooling BTUs per square foot reduced chiller loads and therefore reduced process water used for its evaporative cooling towers, proportional to the change in consumption. The facility uses variable primary chilled water distribution for better balance given variable load demands, point-of-use steam generation to prevent the central steam distribution’s thermal losses, and condensing re-heat boilers with 100 degrees Fahrenheit reheat distribution.
“Our team benchmarked energy efficiency and usage from day one,” Hatton says. “And we benchmarked the facility along with other Memorial Hermann acute care campuses. We didn’t look in the rearview mirror and say, ‘We had a problem last year.’ We were constantly monitoring building performance.”
‘A strong interest’
ASHE’s Brooks concludes, “Hospitals are some of the most energy consumptive buildings in the United States, ranking just behind the food service sector. With that in mind, health care facilities have a strong interest in sustainable design.”
Jeffrey Steele is a freelance writer based in Chicago.