Flexible casework helps health care facilities adapt
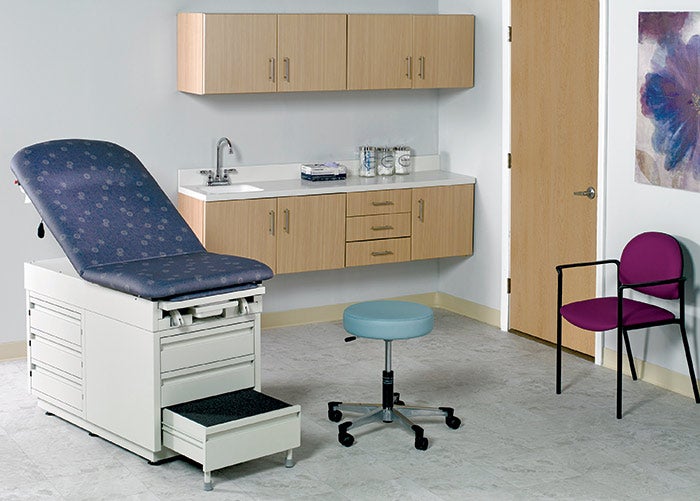
Intensa’s Pulse and Pulse Plus systems are only 16 inches deep, allowing an 8-foot-by-8-foot exam room to feel larger.
Modular casework combines the quality construction of traditional millwork with the added benefit of flexible design — a big plus for health care interiors.
Also in this article |
Modular wall systems provide dynamic options |
|
“In health care, spaces need to be designed to be able to change,” says Joel Van Wyk, director of clinical product category for furnishings manufacturer Herman Miller, Zeeland, Mich. “When we create solutions, they not only need to work well today, they need to be adaptable and adaptive to change, whether it’s the staffing model or the technology or the equipment or the space. We need to do our part to allow facilities to continue to be relevant and continue to allow for effective care,” he says.
Design expertise
Herman Miller entered the health care furnishings market in 1971 with Co/Struc, a system of mobile and modular components for laboratory and health care environments. The 45-year-old product line remains vital; people seeing it for the first time continue to be intrigued by the design’s intelligence and functionality, Van Wyk says. Co/Struc is truly modular, with 24- and 48-inch components that can be combined in a number of ways.
Five years ago, Herman Miller introduced Compass, a modular casework system for hospital and outpatient settings. “A lot of thinking goes into the parts and pieces based on our knowledge of the work that happens in those spaces,” says Van Wyk. Additional design expertise goes into creating solutions that can be reconfigured, upgraded or updated in response to client needs five, 10 or 20 years down the road, he adds.
You may also like |
Prefinished and modular health care designs |
Designing collaborative ambulatory space |
Hospitals vow to reduce furnishings with antimicrobials |
|
The infection prevention features of the system are especially important to clients purchasing Compass for inpatient rooms, according to Van Wyk. These features include overlapping panels that prevent germ entry points, a sink designed to minimize splash and a front edge detail along the work surface that blocks liquid spills from dripping into drawers.
For outpatient facilities, efficient construction and flexible design are major draws. “Customers tend to be interested in the fact that we can build and ship 100 rooms of products in four weeks,” Van Wyk says. “And the fact that they can completely pick up the product line and move it to a different building, because they know they may be in a space for a limited period of time.”
Each year since Compass was launched, Herman Miller has added about a half dozen new products to the line. Among the latest features are new storage solutions for accommodating items like a mini-refrigerator, safe or video game console in the patient room, new material selections and a simplified sink design intended to expand the range of available price points for the system, and new ways to support technology for using electronic health records (EHRs). In the next year, the company plans to introduce an antimicrobial option. “We’ve been studying the issue of antimicrobials for three or four years,” says Van Wyk. “We were able to find a solution that we feel is a really good balance between effectively killing germs and being environmentally friendly, not very costly and safe for people.”
Guaranteed quality
Modular casework for clinics and laboratories manufactured by Intensa Inc., High Point, N.C., carries a standard seven-year warranty to match the depreciation schedule for modular furnishings; if requested, the company will extend the warranty to 10 years. “I’ve never seen any built-in millwork with a warranty,” says Marty Cagle, president, Intensa.
While the depreciation time frame is a clear cost benefit, Cagle says the flexibility of modular casework can provide even greater value. He describes one client, a fast-growing health system in Houston, that plans to add 1,600 doctors over the next four years. “They were very frustrated because they’ve been doing that for the last couple years and they go in, buy the clinic, fix it up, make it look very nice and then six months later, their demographic studies show they should be in a strip mall six blocks down. So they leave behind tens of thousands of dollars of built-in,” he says. “They’re realizing that with the modular capabilities of this casework, they simply can bring it with them. All of a sudden, it’s not a 3 percent savings or a 4 percent savings, it’s a $100,000 savings for a clinic, depending on the size.”
Intensa’s Pulse and Pulse Plus systems are designed for clinic use. The wall-hung pieces are suspended 16 inches off the floor to allow for easier and more thorough cleaning of exam rooms. At just 16 inches deep, they take up little room. “You’re seeing thinner, cleaner lines, which are freeing up space,” Cagle says. An 8-foot-by-8-foot exam room essentially can be turned into a 9-by-8 exam room through the placement of the furnishings, he says.
For infection control, all edges of the Intensa casework are covered, even those that fit against the wall or other places that aren’t visible on an installed unit; this prevents liquids from seeping into the raw wood and creating a breeding ground for bacteria. Solid work surfaces are available with sealed edges for easy cleaning. A bactericidal surface is also available.
Beyond functionality, modular casework offers a contemporary aesthetic. “We feel like exam rooms are coming of age” with a design upgrade similar to that experienced by patient rooms over the past several years, Cagle says.
Intensa’s Essentials laboratory casework joins the strength of steel with the modular construction and flexibility of laminate. The product’s welded, 12-gauge, modular steel frame supports 1,000 pounds per cabinet or table. Laminate doors and end panels can be replaced on an individual basis if damaged. The units feature an integrated chase that allows for easy access to utilities. Casters can be added to any unit for mobility. The Essentials line can be used in conjunction with Intensa’s Catalyst system of vertical rails to organize computers, keyboards and storage elements for greater desktop productivity.
The materials and mechanical devices of millwork by DIRTT Environmental Solutions, Calgary, Alberta, carry a 10-year warranty. Like the company’s wall systems, this millwork is fully customizable and manufactured to the millimeter, says Kristin Moore, director of health care, DIRTT.
Recent innovations include sharps containers and glove boxes that are embedded in the millwork to keep vertical surfaces clutter-free and easy to clean. Exam tables and consultation tables can be embedded in the walls, too. Hands-free drawers, secure lockers and sinks designed to prevent splash-back are among the other products available.
Moore describes DIRTT components as “building blocks” for the design of health care spaces. “A lot of our innovation comes from specific challenges that a client has in the space. There’s all sorts of ways that we can look at creating more efficiencies,” says Moore.
Current and future needs
The Accelerate and Abound lines of systems products from The HON Co., Muscatine, Iowa, “provide great flexibility in the work area,” says Shawn Rininger, director of systems, storage and casegoods, HON. The products’ height and width can be made to fit a specific footprint, from a full nurse station to a smaller touchdown station that might be used for such activities as entering patient data into an EHR or filling out prescriptions.
Durable, hard-surface materials, such as laminate or polymer panels, can stand up to the high traffic of a health care environment. “It won’t get damaged and it’s easily cleanable,” says Rininger. Abound’s open-base frame option makes it easy to clean under the units. The storage pieces lock to keep patient records or other sensitive items secure.
Additional storage options are available in HON’s Contain collection. A personal storage table, for example, would allow a patient receiving chemotherapy to store his or her belongings during treatment. Seating cushions fit on top of these units, so a family member or caregiver could comfortably sit with the patient.
HON pieces can be reconfigured to provide flexibility “not just right now as you need it, but in the future when you redo your work area,” Rininger says. Caitlin Grady, health care marketing manager, HON, notes, “One of the biggest trends … in the health care world right now is the move from large-scale hospitals into smaller outpatient care facilities.” HON systems furnishings fit well into the administrative and patient care areas of both environments. “They’re able to be scaled down from a larger area into a smaller one to work better for the smaller outpatient facilities,” Grady says.
Coordinating units can be especially useful to health systems with multiple locations. “If you’re a large health care provider and you have large and small facilities, we can provide you with great solutions that will coordinate throughout a local, regional or even national area,” says Rininger. This helps to ensure a positive patient experience throughout the system. As providers expand, either within a service area or into a new area, “the furniture will work with them,” he says.
Efficient, well-built, flexible
Efficiency, high quality and flexibility are the trifecta of good health care design. Health care furnishings need to be efficient to buy, use and maintain; well-built, to meet the infection-control and durability requirements of the demanding patient environment; and flexible enough to adapt to changing health care needs. Modular casework delivers on all fronts.
Amy Eagle is a freelance journalist based in Homewood, Ill., who specializes in health care-related topics. She is a regular contributor to Health Facilities Management.