Three areas that can benefit from building information modeling
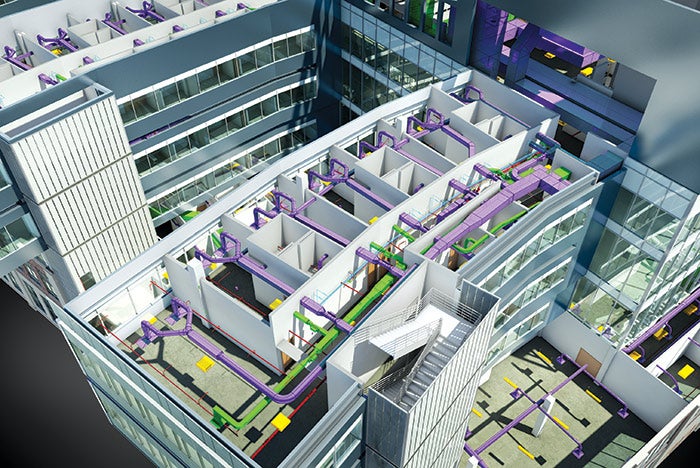
Intelligent areas created in BIM can be used to define spatial relationships and streamline the calculation and reporting of space.
To handle the complexities of today’s health care facilities, building information modeling (BIM)-based design and construction processes are becoming standard.
Also in this article |
How to optimize BIM for post-occupancy |
|
The National Institute of Building Sciences defines BIM as “a digital representation of physical and functional characteristics of a facility. BIM is a shared knowledge resource for information about a facility forming a reliable basis for decisions during its life cycle; defined as existing from earliest conception to demolition.”
This connection to life-cycle management provides opportunities for health facilities professionals, but they must understand certain things about the process before these advantages can be exploited.
Owner-driven process
Health care facilities professionals have a great opportunity to drive their own BIM processes. They have the ability to establish owner-driven data plans that will help to capture the potential value. Taking control of information will allow facilities professionals to set their own objectives, standards and goals. The question they should ask is, “What do I want to get out of BIM?” By setting goals early, facilities professionals can continuously measure, monitor and track the reliability of the data from concept to facility handover.
You may also like |
Transitioning facility operations to BIM |
Medical equipment planning and BIM |
BIM’s role expands as facilities take ownership |
|
They can start by determining the information needs for facility life-cycle maintenance. Traditional thoughts and methods need to be revised as the scope of the deliverable information is prepared. The owner-driven process should be to provide complete and verified building data before the first day of operation.
Time and effort should be taken when preparing for this turnover of information. There are many different thought processes for what needs to be addressed when implementing an owner-driven BIM process. Incorrect data can prove to be costly for a facilities department.
Building commissioning data are key for data validation. In the owner-driven process, building commissioning is used to verify equipment data to avoid wasting time, effort and capital. A three-step method of data collection and validation — design verification, submittal verification and field verification — will bring a business value to BIM and allow the organization to reduce cost, ensure equipment continuity and future-proof its investments.
Taking ownership of this process is critical to the success of an owner-driven plan. The defined scope of the project sets the expectations for deliverable information. The contract scope seems to be an overlooked area with BIM. Defining the scope in a facility’s contracts will add tremendous value and set expectations. Implementing the facility’s standards early will ensure that the facilities professionals can get needed data and avoid any possible misunderstandings in the BIM contract language.
Application areas
To begin the process of exploiting BIM for the operations and maintenance of a facility, there are two areas where the success of early adopters make it prudent to explore — space management and asset management. In addition, some specialty applications are being explored, such as infection control. A closer look at these applications includes:
BIM and space management. The need for a health care organization to have an accurate measure of space usage and allocation is critical. One of the most acute needs is to accurately account for the use of space for the purposes of Medicare-Medicaid facilities reimbursement. Some health care organizations have mentioned that these facilities reimbursements can account for 8 to 12 percent of the bottom line revenue. Federal research grant reporting can have a similar impact on an organization, and also require detailed reporting of the space actually being used for the grant-funded activities. The process for calculating and managing this space can vary greatly between organizations. Regardless of the sophistication of the process, BIM can benefit.
Traditional area take-off methods for space management and chargeback business functions rely on the use of scales and calculators to manually measure floor plans and determine areas. Computer-aided design (CAD) applications introduce a slightly improved method in which electronic floor plans are used as backdrop references and closed polylines are manually added to the floor plans to define areas for calculations. BIM offers a different workflow.
In BIM, components understand their relationships to each other. A wall, for example, “knows” what it is and how to react to the rest of the building. When there are enough walls to create a room, the square footage is immediately calculated. These intelligent areas then can be used to define spatial relationships and streamline the calculation and reporting of space.
The boundaries of these areas (and their area measurements) are based on industry standards such as those by the American National Standards Institute and Building Owners and Managers Association International. Square footage is automatically calculated based on the area type, which is selected when the area is created and can be updated at any time. For example, gross building area is calculated by using the exterior of the walls, whereas office area is calculated using wall interiors. Area boundaries automatically adhere to window height rules as well, so when a window height is greater than 50 percent of wall height, the area boundary lines go to face of glass versus the wall interior. And if the window is modified to be less than 50 percent, the boundary line reverts to the wall interior and the area automatically updates.
Visually, BIM supports the use of such information as department parameters, and creates area color schemes using this department parameter. This enables facilities professionals to create floor plans that are color-coded by department. These area plans are graphic views or representations of areas and, if the model changes, these color-coded floor plans change automatically.
Schedules enable facilities professionals to view the same information in a tabular format. Area schedules based on manual or CAD processes are typically laborious and error-prone. Using BIM, area schedules are merely informational presentations of the underlying model. Facilities professionals easily can create schedules of any type of information in the model such as window and door take-offs or interior finish schedules. Area schedules also can be created to quantify departmental space allocations.
These schedules can be added to any drawing sheet or floor plan, and the information can be exported to a tabular spreadsheet format.
Finally, many of the major integrated workplace management system (IWMS) space management platforms now support BIM integrations.
BIM and asset management. Asset management is a key requirement for health facilities maintenance teams. With changing rules and regulations, the risk of a facility being noncompliant is great.
As BIM integration moves forward, particular attention must be paid to how assets are transitioned to the facility maintenance team. Developing a plan early in the process will allow assets to be properly defined during design and construction. Being able to gather this asset data during design and construction will allow a team to get a better grasp of the assets they will be working with as they move into operations.
The turnover of closeout documents traditionally has been a complex process. Typically, facilities professionals receive a huge number of documents like plans, submittals, and operations and maintenance (O&M) manuals. Oftentimes, they end up collecting dust instead of being integrated into facilities operations. BIM and facilities management integration allows facilities professionals to re-evaluate this traditional process and eliminate the complex layers of the turnover.
A well-considered BIM integration plan allows facilities professionals to continuously collect and check the quality of entered data and documents throughout a project. Using open standards for software integration and creating protocols that require well-defined rules and stringent quality controls will allow BIM to provide a business value. This data set can eliminate the need for manual data acquisition and allow staff to focus on building startup rather than acquiring data the traditional way.
What value does handing over an asset database at substantial completion bring to a health care facility? BIM integration can lead to an accurate, compliant and complete IWMS before the first patient enters the building. It can reduce oversight needed to create, implement and oversee the computer maintenance management system software. It should allow facilities professionals to have complete and accurate O&M manuals. Having this information readily available will allow the facility’s technical staff to be familiar with the manufacturers’ O&M procedures, thus reducing the long-term cost of maintaining the asset. This will reduce the cost of redundant work and cut down on the number of steps technicians take on a daily basis.
Maintaining a building in today’s health care environment is no easy task, but new technologies bring opportunities for optimizing patient care. Asset management with BIM can be a way for a facilities team to impact patient care and building performance.
BIM and infection control. BIM also can help health care facilities develop better ways to understand the spread of the infectious diseases. The sophistication of BIM software will allow health care facilities to use airflow and fluid concepts to better understand the complex movement of air through a health care facility.
Computational fluid dynamics (CFD) can help facilities professionals to analyze internal and external fluid flow and thermal performance. Digital prototyping can help engineers to improve design techniques and optimize building efficiency, but it also will allow facilities professionals to simulate the potential spread of infection. Then, 3-D airflow can show the movement of the pathogens within the building model.
While adding BIM to a complex process might seem difficult, the potential rewards are great. Operating rooms (ORs) gain the biggest advantage. Being able to simulate how the airflow interacts with lighting, equipment and people provides a better understanding of how air can move throughout an OR. Engineers also can understand how the air movement is affected by temperature and humidity as it is circulated in the environment. Modeling and simulation allow for testing multiple design options to help achieve optimal design efficiently.
When combined, BIM and CFD tools can offer significant value to health care facilities planning. Early conceptual simulation will assist in visualization and validation of design concepts. Project teams can better understand the programming of the surgical suite as well as airflow variables that impact the environment of care.
Getting started
The first rule to getting started is to split the conversation into separate tracks — new construction and existing buildings — and then investigate the application of these processes to each track.
For example, a workflow outlined for space management may favor an approach for existing buildings due to the importance of facilities reimbursements and the potential productivity gains versus the investment required. Many health care organizations are converting their CAD-based floor plans to lightweight BIM models to achieve space benefits. One large health care organization documented a doubling of their productivity in calculating space usage and chose to start with existing buildings because of this efficiency.
Conversely, asset workflows could have a high level of application to new construction because of the benefits of meeting regulatory compliance and a quick startup of the operational systems used to manage the hospital's assets. A strong business case justification can be based on the cost savings in transferring asset information directly into the systems that are used to manage them, offsetting manual data entry after the handover of a project.
The key point is to start and learn as the process moves forward.
Charles E. Mies, LEED AP, is business development manager for architecture, engineering and construction solutions at Autodesk Inc., San Rafael, Calif., and Mark Mergenschroer is BIM application specialist for Bernhard TME, Little Rock, Ark. They can be reached at chuck.mies@autodesk.com and mmergenschroer@bernhardtme.com, respectively.