Supporting the maintenance mission
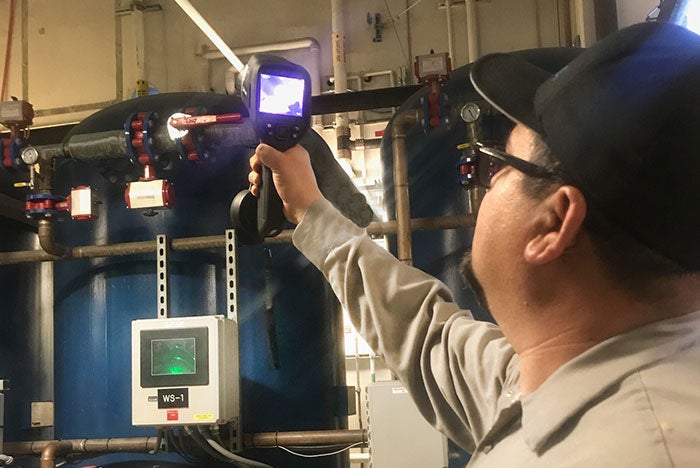
Francisco Flores, plant operations engineer, checking the steam trap in the central plant.
Photos by Megan Pierce of CHOC Children’s
A 300-bed children’s hospital constructed over many years ranging from 1958 to 2012 can be a very diverse and challenging environment and infrastructure to maintain.
The mechanical and electrical systems are extensive, widespread and can get very complicated. In a time where funding and replacement of major components is always struggle, proper understanding of each system and its true conditions as well as its optimal maintenance strategy is utterly essential.
While considering different maintenance strategies, I have found that predictive maintenance technologies can be used to supplement and create a cost effective and efficient way to identify potential catastrophic equipment failure early by utilizing a pro-active and diligent approach.
Predictive maintenance strategies will provide a true condition assessment of the equipment. For example, it makes good sense to proactively maintain equipment prior to experiencing a catastrophic failure causing a major disruption to health care operations. Predictive maintenance technologies have provided my team a systematic approach by enhancing routine maintenance tasks beyond historical maintenance techniques and frequencies.
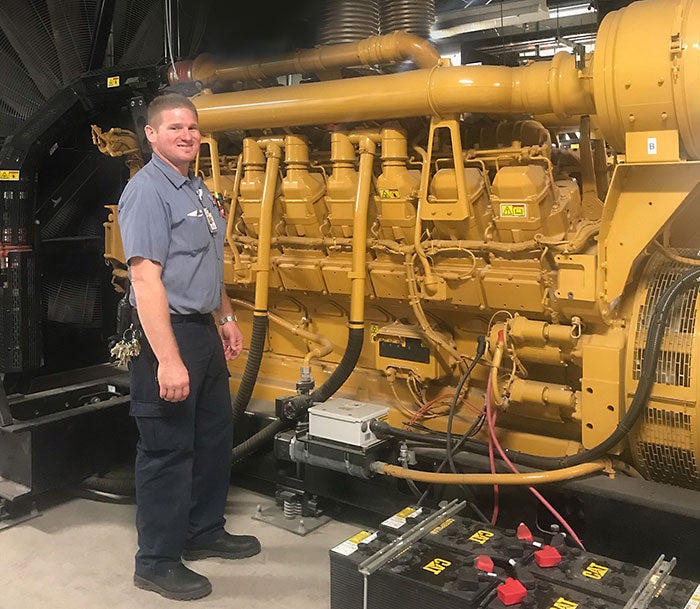
Travis Roper, facilities supervisor, performing preventative maintenance to the emergency generators.
Photos by Megan Pierce of CHOC Children’s
Nevertheless, the switch to predictive maintenance technologies does not come without challenges. It requires a different thinking process and commitment from the management team as well as the front-line staff. Staff education and communication are key elements of any quality-oriented maintenance program. Purchasing more advanced testing and diagnostic equipment such as vibration analyzers, thermal imagers, pressure differential monitors and more is one thing, properly educating staff on the usage and program requirements is another. Staff education, communication and team work must be present before making any changes to an existing program to successfully implement.
Another positive side effect in implementing various procedures and incorporating them into our already existing preventive maintenance procedures has helped my staff and I better understand our infrastructure and system condition, making staff more knowledgeable and confident in their abilities. After all, it is the staff that performs the tasks not the manager; confident and forward-thinking employees are more productive and effective.
Guaranteeing higher reliability
Four years ago, shortly after I started my position at CHOC Children’s in Orange, Calif., and commissioned and opened a new 456,000-square-foot tower addition to the existing campus, I realized the immense workload and systems in place needed a prompt and thorough overhaul to guaranty higher reliability and up-time. I also realized that historic maintenance at the hospital wasn’t meeting the needs of daily operations, neither from reliability nor from an energy consumption point of view.
Obviously both reliability and energy consumption have a great impact on operational as well as capital expenditures. The first major task was adding all the new equipment to an already extensive equipment inventory. The next major element was reviewing and validating the hospitals existing equipment inventory which turned out to be a challenge, including the occasional “needle in the haystack” search. This was followed by reviewing the maintenance procedures, many of which were either obsolete or not specific enough.
Quickly we realized that maintenance is only as good as the task that is being performed; rewriting and updating of tasks was a necessity and, anytime you rewrite or update a procedure, staff education and training will be necessary.
After these steps, we defined our approach. First came the low-hanging fruits such as bearings, steam traps, motors, filters, ice machines and refrigerators. After that came the more challenging items such as controls, transfer-switch equipment, electrical distribution, large chillers and cooling towers. The final group included utilizing the condition reports to develop a capital replacement strategy for equipment in desperate need of attention after reaching an unreliable state or to support energy conservation initiatives.
The implementation of the vibration analysis program was accomplished by partnering with a third-party vendor. The initial implementation of the program allowed the facility to obtain a base line of the equipment that was used to educate everyone involved in the program. Staff quickly identified necessary repairs that included items such as bearings, that we confirmed when we conducted a tear down and inspection of the equipment.
Upon inspection, the initial readings of our vibration analysis were confirmed and allowed us to avoid a potential catastrophic failure and giving the facility the opportunity to plan a scheduled shut down and repair. The opportunity to schedule a piece of critical equipment for shut and repair is very valuable as most of the parts needed to complete some repairs need to be ordered and aren’t usually readily available. In the process, we were also able to teach our staff what proper lubrication of bearings means — too much grease is as bad as too little.
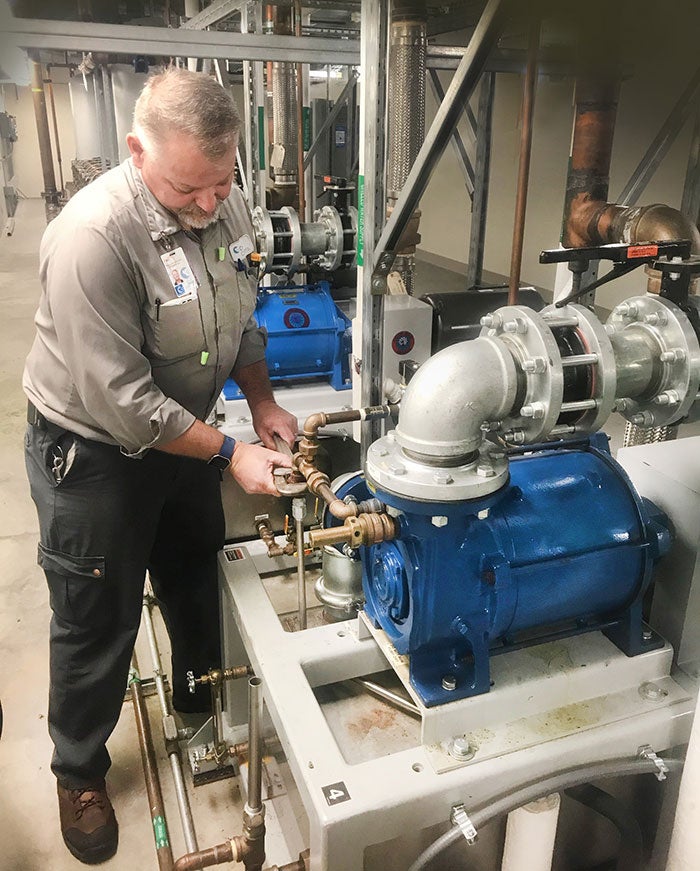
Paul Versteeg Jr., plant operations engineer, maintaining medical vacuum pumps housed in the facility.
Photos by Megan Pierce of CHOC Children’s
Another technology that we implemented was the use of thermal imaging equipment into the facility with more successful results. However, I highly recommend professional training for this type of equipment as I realized in my first day of thermal imaging class that thermal imaging is not a simple science and could be a waste of time unless the proper training is received. Now we are using the imager to diagnose a wide range of problems from leaking roofs, to electrical panel, boilers, steam systems and everything in-between.
The first project that we conducted with the new thermal imager was an assessment of all the steam traps in the facility. Wouldn’t you know it? Three out of four existing traps failed and appeared to have not worked for years. The positive side of this inspection and the high failure rate was that our local gas company has a nice incentive program when replacing old steam traps.
Based on the program we internally replaced a significant number of our traps receiving somewhere between a $100 to $200 rebate per trap, the true cost of the work was only our labor which must be paid to staff anyways. If available, rebates are great incentives to facility operators. Our electrical provider also has similar programs available to incentivize the replacement of items such as motors, refrigeration compressors, air compressors, gasket materials, heat/window films and insulations. Every time the reliability to cost ratio allowed we replaced equipment to newer energy efficient rather than maintaining aged equipment.
Proceeding into the future
Undoubtedly, the implementation of predictive maintenance technologies and the updates to our existing program has shown unlimited potential and can be customizable to each facility and budget. We realize that this process must proceed into the future as new equipment, new techniques and better testing equipment becomes available. The rewards are multifold, higher customer satisfaction, higher employee knowledge and self-esteem, and a reduction of critical systems failures.
In the end, we all need to understand that communication, training and education as well as vision and a good understanding and assessment of risk are the vital part of any successful program. It starts with the human factor, different skill sets and mentalities that need to be brought to a common understandable language leading to a safe, operational and reliable environment maintained by compassionate and visionary stewards.
Lastly the implementation of these predictive maintenance technologies is the precursor to the development of a true reliability-centered maintenance program. More information regarding reliability-centered maintenance program development and implementation is on the way from various sources.
I encourage you to consider learning more about this topic. The opportunity that we have to transform our historical approach to maintenance by using good science to develop alternate maintenance strategies based on the true equipment condition will be ground breaking. The key will be for us to diligently track, trend and share our data to justify the development of alternate maintenance strategies.
Manufacturer recommendations are a good starting point but in my experience, they don’t properly address the true need. I would prefer the ability to perform what is needed when it is needed by understanding the true condition of the equipment in real time.
Devin Hugie, SASHE, CHFM, CHC, CHSP-FSM, CHEP, is executive director of support services for CHOC Children’s, Orange, Calif. He can be reached at dhugie@choc.org.