Commissioning existing health care buildings
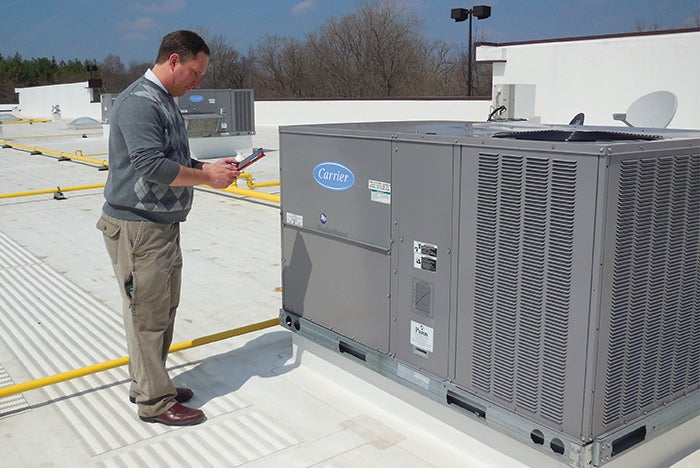
From subbasements to rooftops, existing building commissioning engineers examine all aspects of health care facilities infrastructure, with an eye to improving efficiency and reducing costs.
Image courtesy of Grumman|Butkus Associates
Existing building commissioning (EBCx), previously referred to as “retrocommissioning,” can be a powerful tool for health care organizations that are striving to maximize energy efficiency, reduce greenhouse gas emissions and cut operating costs. Whether the facility is relatively new or decades old, the process can highlight low- and no-cost adjustments that may yield impressive savings in energy consumption and dollars within only a few years.
EBCx also may suggest capital improvements with an attractive longer-term payback and help owners prioritize such efforts.
Based on about 15 years’ worth of data regarding more than 100 EBCx projects (including more than 60 hospitals), average annual electrical savings have been 5.7% (about 1.23 kilowatt-hours (kWh) per square foot), and average natural gas savings of these projects were 7.8% (0.075 therm per square foot). Overall, the average annual energy cost savings amounted to 6.6%, with an average simple payback period of only 0.71 years. (Adding in the provider fee generally will increase payback by about one year, but such fees are often funded entirely or partially by utility incentive programs.)
Anatomy of a program
A health care EBCx project typically includes a planning phase, a detailed investigation phase, an implementation phase and a verification/hand-off phase, preferably followed by ongoing commissioning (OCx). Sometimes facility adjustments or upgrades, particularly around building controls, may be required before a productive EBCx program can commence.
Planning phase. This generally involves conducting staff interviews and gathering existing data, including utility bills; floor plans; as-built documentation, especially for the building automation controls or a building automation system (BAS); an equipment inventory; test and balance reports; and information about planned upgrades.
Recently, the investigation approach has expanded to incorporate fault detection and diagnostics (FDD) software, which is most productively onboarded during the planning phase to kick-start collection of trend data or equipment performance data.
The planning phase investigation verifies BAS sensor accuracies and equipment configuration, helping to validate the FDD software. Then, the detailed investigation explores opportunities suggested by the software.
The combination makes the entire EBCx process more efficient. Implementing FDD early also maximizes the value of the software throughout the project and beyond.
Investigation phase. This represents a deeper dive, including analysis of trend logs and functional performance testing. The testing effort may examine air-handling units (AHUs) and rooftop units (RTUs); terminal units, such as variable air volume (VAV) boxes and fan-powered boxes, fan coil units and heaters; chilled water (CHW) systems; heating systems; exhaust systems; and temperature/humidity/pressure controls and relationships for critical zones, such as operating rooms (ORs) and pharmacies. Operations and maintenance issues such as sensors needing calibration or broken valves, dampers and actuators typically are identified during functional testing.
The hospital facilities staff and the commissioning provider (CxP) should meet before proceeding with a detailed investigation to ensure that the work moves ahead effectively.
For example, assessing the usefulness of temperature reset strategies might only be possible if critical-zone requirements are investigated in detail.
Access to active care spaces such as ORs is typically limited during the day, so testing often is completed after hours and must be coordinated with site staff and nursing staff. Without an adequate dialogue, the EBCx team could be prevented from accessing all the necessary spaces or could spend excess effort investigating equipment that is already scheduled for replacement.
In addition to site staff support, a controls contractor and/or test and balance (TAB) contractor often is needed during the investigation phase. The controls contractor can assist by answering questions and digging into the details of the sequence of operations or by helping to set up trends. The TAB contractor may be needed to confirm critical-zone airflows or pressure readings. Hospitals should budget $10,000 to $20,000 for contractor support during the investigation phase.
A report showing recommended improvements, or energy efficiency measures (EEMs), is the key deliverable of this phase. It should include a detailed utility analysis; a description of the facility; system descriptions and baseline sequence of operations; a description of the recommended measures, including kWh savings, therm savings, dollar savings and predicted payback; and, possibly, an estimate of implementation costs.
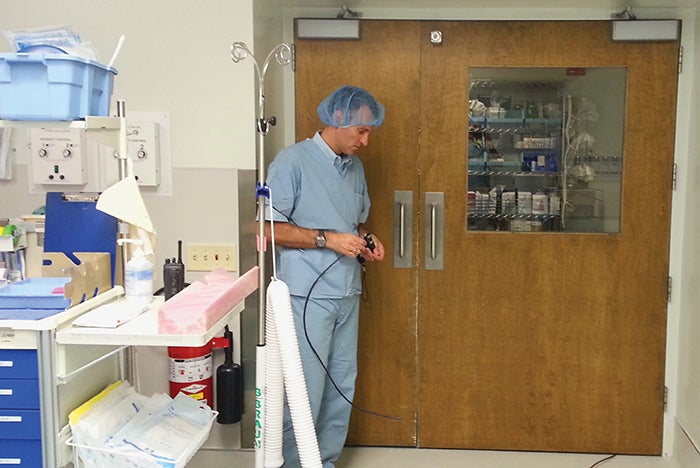
Testing of critical space pressurization is an essential aspect of existing building commissioning in health care facilities.
Image courtesy of Grumman|Butkus Associates
Implementation phase. During this phase, the hospital selects measures for implementation.
In a traditional model, the hospital issues purchase orders to relevant contractors and manages implementation of the measures. Projects also may be structured as an energy performance contract, with work performed by an energy services company and funded by the savings realized by the project. Some CxPs also offer turnkey design-build services. In the design-build model, after the EBCx study is conducted, the CxP may design the necessary changes and even manage the construction work. Hospitals should be clear about the implementation scope being offered in any EBCx project.
Verification/hand-off phase. This phase begins after measures have been implemented. Ideally, all measures have been implemented successfully and the predicted savings have been realized, but often this does not occur.
The verification process, which incorporates commissioning, not only confirms that the scope of work was completed but also that each measure is performing as intended. Verification usually includes additional measurements, functional testing or trend data analysis. Adjustments may be necessary to achieve the intended savings or to tweak the sequence of operations if measures are creating issues for occupants. The CxP’s hands-on support is vital to project success and savings persistence.
When developing the verification approach, it’s important to balance the level of effort required to complete the process with the level of uncertainty allowed.
Suppose a basic verification approach can achieve 90% savings prediction accuracy. The uncertainty amounts to 10% of the savings. If the predicted energy savings are $50,000 per year, it may be reasonable to spend $5,000 to boost the accuracy of the effort — perhaps by installing energy meters, data loggers or additional sensors. But if the predicted savings for the measure are $1,000 per year, it may be reasonable to spend only $100 on the verification effort.
Also included during this phase is training the building operators on the modifications and new sequences of operations. Most or all of the savings from EBCx can be wiped out by a few turns of a valve or by clicks on the keyboard at the BAS. The CxP must transfer the necessary knowledge to the operations team. With FDD software already in place, the hospital can elect to keep using it for OCx to ensure persistent savings. Such work may also be called the “persistence phase,” “monitoring-based commissioning,” or “continuous commissioning.”
Studies from Lawrence Berkeley National Laboratory and others suggest that a third of the energy savings achieved through EBCx may be lost within three to five years due to equipment operating issues, shifting occupant expectations, seasonal changes or facility staff turnover. OCx is essential to keep buildings operating efficiently.
This process should be integrated into existing workflows to help facilities staff and hospitals prioritize resolution of issues that have an energy impact, alongside typical maintenance issues.
In a best-case scenario, the building operators have access to the FDD platform and can resolve issues and respond to recommendations on their own. More often, the CxP is needed to continue active reviews, make recommendations to site staff, support the implementation or resolution of issues, and document any new energy efficiency opportunities and their resulting savings.
Typical efficiency measures
Some typical EEMs that may have an attractive payback for health care facilities include:
- AHU discharge air temperature and static pressure resets.
- Economizer optimization.
- Minimizing or eliminating simultaneous heating and cooling.
- Nighttime AHU and VAV scheduling, such as reducing airflow to unused ORs, kitchens or office suites at night.
- Condenser water supply temperature resets.
- Differential pressure resets, such as secondary CHW or hot water (HW) pumps.
- Chiller, heat exchanger and cooling tower staging.
- Boiler plant staging and pumping optimization.
- Kitchen exhaust fan scheduling.
- Replacing failed control valves or damper actuators.
Most of these measures involve changes to operating parameters or schedules governed by the BAS.
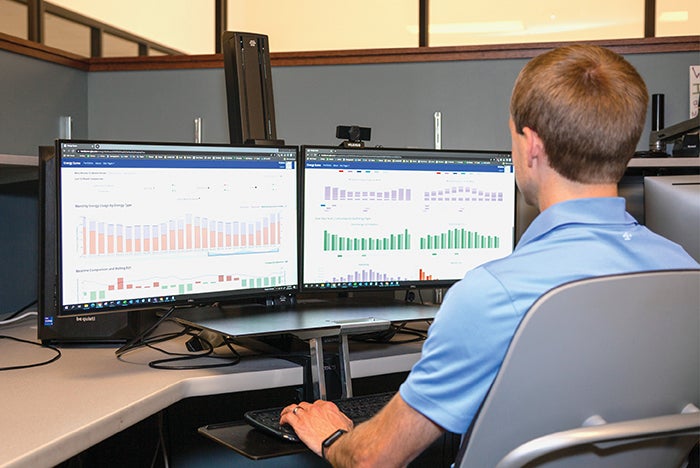
Increasingly, engineers are using analytics software to analyze facilities’ overall energy usage and the performance of systems and equipment.
Image courtesy of Grumman|Butkus Associates
Modified setpoints often can be identified through functional testing. ASHRAE provides guidance on economizer setpoints based on the local climate zone. On a static pressure reset or CHW or HW differential pressure reset, the most remote or most critical zone will dictate how low a setpoint can be. The minimum condenser water supply temperature will vary based on chiller manufacturer and the ability to control to refrigerant head pressure. These types of adjustments lie within the realm of low- and no-cost, short-payback measures that are the goal of a standard EBCx project.
However, investigators often uncover issues and opportunities that require hospitals to budget for capital projects. Though the payback is longer term, such measures often make sense based on facility objectives for reliability, energy efficiency, resiliency and sustainability. Examples include AHU, RTU and chiller or boiler plant upgrades or replacements; addition of variable frequency drives on AHUs, cooling tower fans and CHW pumps; installation of plate-and-frame heat exchangers and/or heat recovery systems; steam leak repairs; and BAS upgrades.
Finding a provider
While the EEM list may appear standard to any large facility, health care facilities present a unique challenge. Hospitals should look for commissioning providers that have experience in implementing energy saving opportunities in health care settings.
A commercial facility may reasonably accept a discharge air temperature reset that raises temperatures by 10 F. But in a health care facility, 5 F is more reasonable to avoid negatively impacting patient comfort or relative humidity. Pharmacy, central sterile processing, ORs and other procedure rooms (e.g., C-section rooms) often have exacting humidity and pressurization requirements that will dictate how far the facility can push the savings envelope. CxPs should understand the relevant standards and goals.
Similarly, night setbacks in ORs are possible, but extra care during the investigation phase is crucial. The minimum air change rate must be checked, and testing must verify that the rooms stay positively pressurized before, during and after the transition from occupied to unoccupied mode.
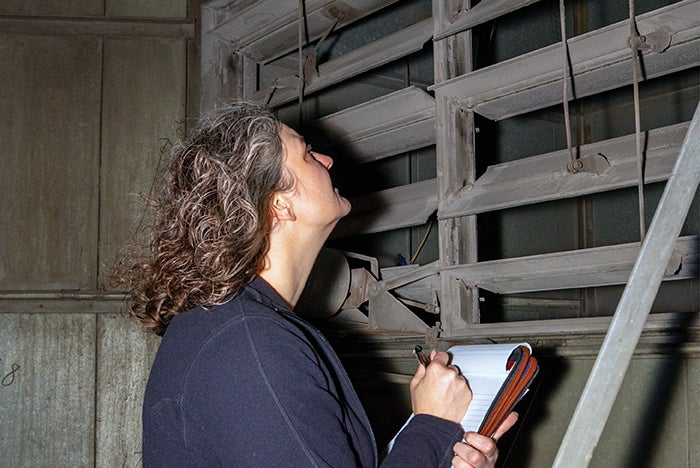
Heating, ventilating and air-conditioning inspections during existing building commissioning often include documenting the condition and functionality of fans and louvers.
Image courtesy of Grumman|Butkus Associates
Medical centers that include research and laboratory spaces are another area in which CxPs must have specialty experience. Chemicals require fume hoods and controlled ventilation. Space pressurization must be monitored to ensure fumes are exhausted from the lab space and not into surrounding offices.
To realize all the potential benefits of EBCx, owners should carefully vet service providers to be sure they have appropriate health care experience.
The expense of hiring a professional CxP to conduct the EBCx project will, of course, lengthen the estimated payback period, since the CxP must be paid even if the recommended measures are inexpensive. Nevertheless, a provider with strong health care facility experience will be able to suggest steps that will pay off — not only in dollars and energy consumption but also, often, in reliability, patient comfort and reduced hassle for the facility’s operations team.
Fortunately, in many areas, public utilities will subsidize all or part of the cost of an EBCx study, making the payback even more attractive.
For instance, ComEd, the electrical utility for Chicago and northern Illinois, currently offers three levels of EBCx incentives; one of them, “Retro-Commissioning Flex,” provides fully funded studies for facilities whose peak demand exceeds 100 kW. By contrast, a New York State Energy Research and Development Authority initiative called “FlexTech” allows eligible facilities to receive an EBCx cost-share of at least 50%. Safety net hospitals in disadvantaged communities can receive a 100% cost-share.
Utilities may impose various requirements for project approval, implementation and third-party verification. For instance, a ComEd-funded Flex study requires building owners to agree to implement mutually agreed-upon measures with a simple payback of 1 1/2 years or less.
Health care facility owners should always discuss the availability of utility funding with any EBCx providers under consideration.
Peak performance
EBCx is a practical, financially attractive process for helping hospitals and other health care inpatient or outpatient facilities perform at peak energy efficiency while reducing their carbon footprint.
An OCx program, harnessing the power of FDD software and dovetailed with the analytical skills of a good CxP, will help ensure continued savings. It should be a key tool for every health care facilities manager.
Related article // Existing building commissioning yields savings for health system
Arecent initiative by Universal Health Services Inc. (UHS), a Pennsylvania-based health care organization that operates 27 acute care hospitals and more than 450 other health care facilities nationwide, demonstrates the impressive potential of existing building commissioning (EBCx).
UHS conceived a four-year initiative intended to reduce heating, ventilating and air-conditioning (HVAC) energy consumption costs by 20%, with a program encompassing about 4.8 million square feet of facilities in California, Texas, Nevada, Florida, Oklahoma and the District of Columbia.
A proof-of-concept project at Palmdale (Calif.) Regional Medical Center helped the team refine the EBCx plan before rolling it out across the targeted facilities. This comprehensive project identified a few code issues, nearly 30 general operations and maintenance issues, nine energy efficiency measures (EEMs) and nine more capital-
intensive measures.
About a dozen additional measures were suggested to give the hospital a detailed picture of how the facility might make long-term gains in energy efficiency and sustainability. The EBCx project saved more than 20% of HVAC energy costs, and another 20% savings was identified through conversion of constant-volume boxes to variable air volume control. (Project staging has been necessary due to impact on patient spaces as well as approval requirements from the local authority having jurisdiction.)
Levels of EBCx scope for the UHS facilities varied with each site’s size, condition and goals, but the overall process included phases of planning, investigation, implementation, verification and ongoing commissioning. Third-party fault detection and diagnostics and energy information system software platforms were used to help identify additional EEMs and verify performance of implemented measures.
Typical measures developed through EBCx included air-handling unit (AHU) temperature and pressure resets; economizer modifications; AHU scheduling and setbacks; and staging optimization of boilers, pumps, chillers and cooling towers.
In some instances, new sensors and valves were installed, as well as variable frequency drives and plate-and-frame free cooling heat exchangers. The commissioning provider (CxP) also provided design and construction management services for capital projects, overseeing installation of selected measures.
The CxP and the hospitals’ facilities teams collaborated in applying for financial incentives through various local utilities, resulting in incentives of nearly $400,000. Cost savings for the entire four-year EBCx cycle were nearly $2.2 million.
About this article
This article was contributed to Health Facilities Management by Grumman|Butkus Associates in partnership with the Building Commissioning Association.
John Villani, PE, CCP, CEM, LEED AP, is vice president and commissioning team leader; Fiona Martin McCarthy, PE, QCxP, BEAP, LEED AP O+M, is associate; and Tim Shinnick, PE, QCxP, CEM, LEED AP, is associate at Grumman|Butkus Associates in Evanston, Ill. They can be reached at jvillani@grummanbutkus.com, fmccarthy@grummanbutkus.com and tshinnick@grummanbutkus.com.