Maintaining fire safety in hospitals
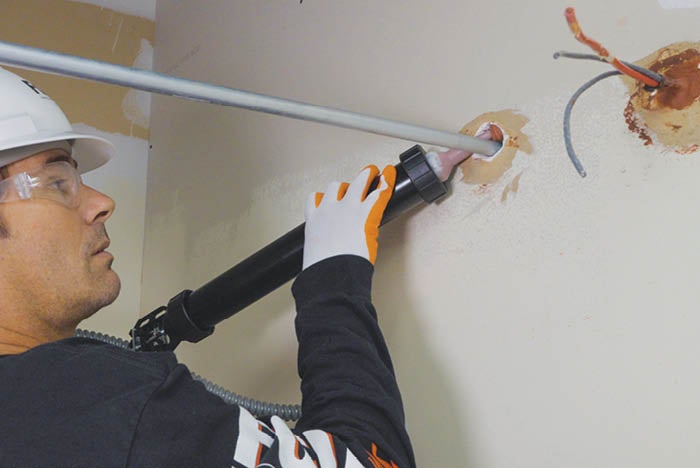
Fire resistance looks easy to install until systems are reviewed and limitations are known.
Image courtesy of FCIA
A hospital facility is one of the most protected structures in the country. Detection and alarm systems, automatic suppression systems, structural protection and effective fire resistance-rated compartmentation during new construction provide amazing safety.
Specifiers, general contractors (GCs) and subcontractors work to get installations done right. After handover from the GC, the facilities manager is responsible for maintaining protection of the building’s safety features.
Fire test standards
Fire resistance-rated assemblies and building elements — beams, columns, walls and horizontal assembles — are used to construct hospitals. They are fire tested in accordance with ASTM E119, Standard Test Methods for Fire Tests of Building Construction and Materials, or UL 263, Standard for Safety of Fire Tests of Building Construction Materials. Other methods also may be used to determine fire resistance as listed in the codes.
The testing also provides a comparison basis for different fire resistance assemblies for floors and walls.
The ASTM E119 and UL 263 fire tests were developed to provide proof that materials will keep the assembly or building element under acceptance temperatures from ASTM E119 or UL 263 standards. Testing proves the suitability of products for use as systems, which results in a listing.
Exceeding structural building element or assembly temperature thresholds causes structural strength loss — and the resultant sagging, expansion and possible breaking of beam/column connections supporting a building. For walls, exceeding temperatures results in fire spread without holes poking through the wall, or conditions not tenable for humans to use the area for egress.
When steel and concrete structural elements and assemblies are used to provide a fire resistance rating, sprayed fire resistive materials (SFRMs), intumescent fire resistive materials (IFRMs), boards and wraps are used. Concrete, masonry, or gypsum panel assemblies can provide the fire resistance, too. Wood assemblies might be protected with Type X or Type C gypsum panels.
The ASTM E119 and UL 263 test standards are used to prove that materials protecting breaches in fire resistance-rated assemblies, fire dampers, fire doors, firestopping and fire-rated glazing provide fire resistance. Each of these fire tests uses a smaller-scale assembly.
For instance, an ASTM E119/UL 263 full-scale fire test apparatus is used to evaluate a horizontal assembly, where size is critical. The full-scale furnace is approximately 10 feet by 18 feet, with a load applied via “rams,” representing real-world conditions. Without a load, fireproofing could pass an hourly fire resistance test but could fail under real-world conditions. Small-scale testing is not acceptable for horizontal assemblies, except for horizontal shafts.
Building and fire codes
All fire resistance-rated and smoke-resistive assemblies require installation in accordance with the listing and the manufacturers’ instructions. Some require special inspection as defined in chapter 17 of the International Code Council’s (ICC’s) International Building Code and chapter 12 of the National Fire Protection Association’s NFPA 1, Fire Code. All fire resistance-rated building elements require that the fire resistance protection be maintained continuously for the building’s life cycle.
In a way, the building and fire codes are the law; and all codes can be used in a court of law — or by an insurance company. Hospitals work to comply with requirements in NFPA 101®-2012, Life Safety Code®, because the Centers for Medicare & Medicaid Services uses the code as a basis for service reimbursement for patients. Other fire codes, including the ICC’s International Fire Code (IFC) and NFPA 1, also have specific language that addresses maintaining protection.
NFPA 101 contains a paragraph that requires the hospital facilities manager to maintain fire resistance-rated assemblies and smoke-resistive assemblies. In chapter 4, the charging language states that the chapter 8 “features of fire protection” need to be “continuously maintained.” How that is done is up to the hospital facilities manager.
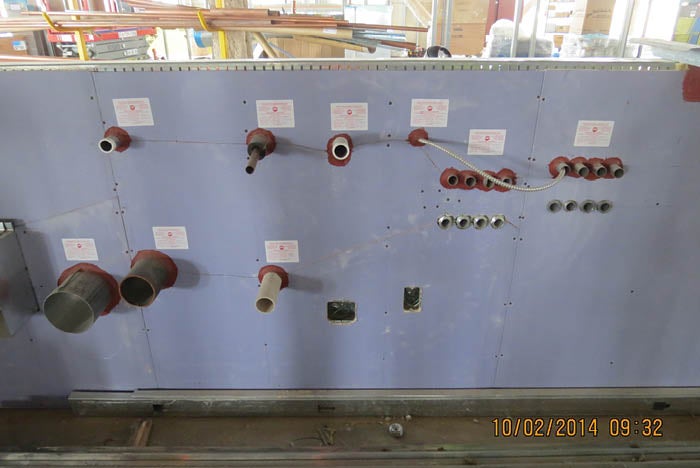
Firestop labels identifying tested and listed systems provide easier visual inspection because the system number is on the wall.
Image by Corey S Zussman, Pepper Construction Co.
NFPA 1 assigns responsibility to the building owner (e.g., hospital facilities manager) to ensure that the products and systems were installed correctly in the first place and are maintained continuously. Even if an authority having jurisdiction (AHJ) approves the building, the building owner is still the responsible party should there be loss of life or property due to an improper installation or lack of maintenance of the fire resistance or smoke-resistive features. The details in the 2018 edition of NFPA 1’s section 12.3.3.1 state that fire resistance-rated assemblies, even the roof coverings, “shall be maintained and shall be properly repaired, restored, or replaced where damaged, altered, breached, penetrated, removed, or improperly installed.”
Then, section 12.3.3.3.1 requires that visual inspection of fire resistance-rated assemblies be performed by a person who demonstrates “appropriate technical knowledge and experience in fire resistance-rated design and construction acceptable to the AHJ.”
Further, NFPA 1 mandates the frequency of visual inspection for fire resistance in high-rise buildings is required once every three years.
The IFC takes fire resistance and breaks it into sections by assembly and protection discipline. For assemblies, exterior walls, firewalls, fire barriers and fire partitions, smoke barriers and smoke partitions, horizontal assemblies and shaft enclosures are all mentioned.
For breaches in these assemblies — penetrations, joints and voids, door and window openings, duct and air transfer openings and concealed spaces — protection must be maintained. There also is a separate section that addresses structural fire resistance, SFRMs and IFRMs.
Just before the “owner’s responsibility” section, it states, “materials, systems and devices used to repair or protect breaches and openings in fire resistance-rated construction and construction installed to resist the passage of smoke … shall be maintained….”
In 701.6, Owners Responsibility, the IFC requires an inventory of fire resistance-rated building elements and assemblies and the features be kept. Records of inspections and repairs are required. The AHJ can at any time ask for the fire resistance-rated and smoke-resistive inventory and annual visual inspection/repair records. If NFPA 1 or 101 is used in the jurisdiction, the AHJ might also ask for proof that “the individual providing the visual inspection is competent …”
The IFC also has similar language to NFPA 1 for fire resistance-rated and smoke-resistant assemblies, where it states that these assemblies be “visually inspected by the owner annually and properly repaired, restored or replaced where damaged, altered, breached or penetrated. Records of inspections and repairs shall be maintained.”
Similar language also is in the ICC’s International Property Maintenance Code. For hospitals with internationally located facilities, the United Arab Emirates Fire and Life Safety Code of Practice has very consistent sections with the IFC; and Saudi Arabia’s code, Section 107.1, has sections that look like NFPA 101. In Canada, the National Fire Code expects fire separations to be “repaired so that the integrity of the fire separation is maintained.”
It’s clear that in several codes, fire resistance-rated and smoke-resistive assemblies need protection maintained. In fire resistance, these are all systems that can be found in directories such as the UL Product iQ™, Intertek or the FM Approval Guide. The products used to build these tested and listed systems might need routine maintenance. Where products don’t require maintenance, the tested and listed system will need to be visually inspected to be sure alterations that would violate the listing haven’t taken place.
Barrier management
There are some key steps the building owner and manager need to consider to comply with the various fire codes and standards to maintain protection of fire resistance-rated and smoke-resistant assemblies in buildings.
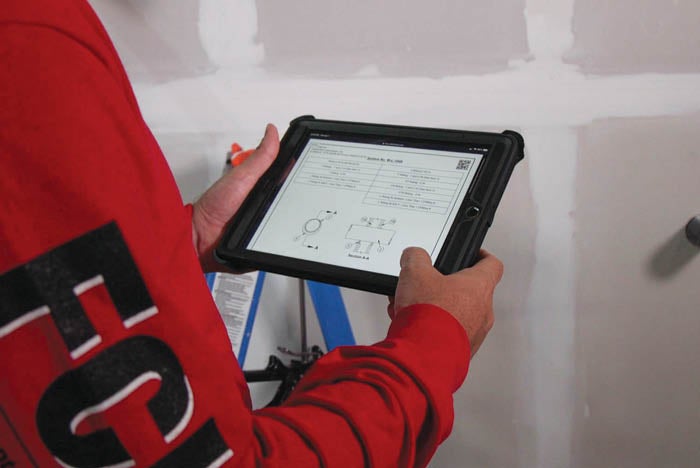
Life safety drawings, tested and listed systems, and manufacturers’ installation instructions, are mandatory for maintaining protection.
Image courtesy of FCIA
The first step is to build a fire resistance and smoke-resistant assembly inventory to set up and inform management of the building elements and assemblies. The inventory should include life safety drawings and plans showing rated walls and floors for fire, smoke, sound and other considerations; tested and listed systems listings, if not included in manufacturer’s installation instructions for each of the products used; the manufacturer’s installation, maintenance and repair instructions for records of which version of products were used; and the manufacturer’s product data sheets. Finally, manufacturer safety data sheets (where applicable) are needed for worker and building occupant protection.
Once the inventory is built, it needs to be managed. A visual inspection and survey schedule is needed with a frequency that results in the safety demanded by NFPA 101 and other applicable codes.
Of course, to manage the fire resistance-rated and smoke-resistant inventory, someone needs to take on this important assignment. That’s where someone needs to assign a “barrier management champion” — the individual responsible for ensuring that inspections, repairs and recordkeeping take place on a timely basis. Facilities managers should remember that The Joint Commission (TJC) arrives every three years. Additionally, a fire marshal and code official can request records at any time, and insurance companies can as well.
The barrier management champion then needs to educate the inspection and repair staff and all other staff who come into contact with barriers. Education leads to compliance, with staff buying in over time.
To become a “responsible person,” as required by NFPA 101, the champion and staff education can consist of many sessions with manufacturers, distributors and the free Barrier Management Symposium online video series created by the American Society for Health Care Engineering, the Firestop Contractors International Association (FCIA), TJC and UL. This symposium provides generic product and systems knowledge for staff — from purchasers of services to the workforce — to understand the complexity of fire resistance-rated and smoke-resistant assemblies (see the ASHE Resource box on this page for more).
Other sources of education include webinars by FCIA at fcia.org and the International Firestop Council as well as offerings by the National Fireproofing Contractors Association, the Gypsum Association, the Air Movement and Control Association International, the Door & Access Systems Manufacturers Association, Association of the Wall and Ceiling Industry, UL, Intertek, door groups and fire-rated glazing manufacturers who participate in Barrier Management Symposiums.
After the barrier management process is in place, it is most critical to maintain continuous protection through visual inspections and repairs. The barrier management process can be managed efficiently through a process that keeps easily retrievable inventory and inspection/repair records and the status of each.
The final step is to repeat and document the process for the building life cycle, so the facility remains safe for patients, visitors and staff. Additionally, this ensures the facilities team will be ready at any time for AHJ or fire marshal inspection as well as review by TJC or an insurance company.
Throughout the codes and standards — and the barrier management process — inspections are referenced. These seem to be described as visual inspections (i.e., a survey, rather than destructive testing). A survey is a visual review, where the assembly seems to comply or seems not to comply.
Facilities managers should check out the UL Product iQ website to learn more about the systems. These systems are used to visibly compare whether the assembly — fire door, firestopping, fire-rated glazing, fire dampers, etc. — seems to visually comply or not.
Repair requirements
Fire dampers must be repaired in accordance with their listing, which is incorporated in the manufacturer’s installation instructions. Fire-rated glazing has a listing with manufacturer’s instructions for the glazing and frame.
For fire resistance-rated gypsum panel systems, “scab patches” are not allowed. The furnace pressures used during the fire test might push the patch held by wallboard compound and paper out of the wall. Then, the mandatory hose stream test will blow the patch right through the assembly. NFPA 1 states a repair procedure, as does the Gypsum Association.
Fixing fire-rated doors with generic metal extension plates is not allowed either. There are metal extenders that have been tested at fire test laboratories available for this repair, making the door a system again.
When patching fireproofing, repairs in accordance with the listing and manufacturers’ installation instructions — the system — are required. (To learn more about this topic, read the Fall 2018 edition of FCIA’s Life Safety Digest.)
Additionally, firestopping cannot be patched with just any red firestop sealant. To maintain firestop protection, only the firestop sealant that is in the tested and listed system can be used. An accredited specialty firestop installation contractor can provide the manufacturer-recommended repair for the firestop product referenced in the firestop system.
Some hospitals use their staff for maintaining fire resistance-rated and smoke-resistive assembly protection. That works if the responsible people are competent as required by NFPA 101 and NFPA 1. Other hospitals use specialty firestop installation contractors to manage the complete barrier assembly, including patching walls and floors; testing fire dampers and doors; and fixing breaches with firestopping. Whichever method is chosen by a hospital to maintain fire resistance in buildings, a professional who has knowledge and experience working with fire resistance-rated and smoke-resistant assemblies is essential to manage the process.
A continuous system
Facilities managers should develop a barrier management system to maintain the fire resistance-rated and smoke-resistive building elements and assemblies continuously, so they work when called upon during a fire event.
FCIA and its role in fire protection
The Firestop Contractors International Association (FCIA) created the Barrier Management Symposium (BMS), a program that focuses on fire resistance-rated and smoke-resistive assembles, and the need for a systems culture to maintain them.
FCIA collaborated with the American Society for Health Care Engineering (ASHE), and The Joint Commission and UL to deliver the BMS live throughout the U.S., helping hospitals create competence to either hire the service from the outside or to use their own staff. The BMS lives on at FCIA and ASHE’s websites.
Since 1998, FCIA members have built or improved standards for firestopping through the FCIA’s mission for proper firestopping design, installation, inspection and maintaining (DIIM) protection. Some members have management systems for maintaining protection in existing hospital buildings to keep hospitals compliant with NFPA 101®-2012, Life Safety Code®, and other codes. Most importantly, they help keep people safe in buildings. Lives and continuity of operations in hospitals, homes, offices, stores, malls and elsewhere count on fire resistance-rated and smoke-resistive assemblies working when called upon by fire. It’s just as important as the fire suppression system, the fire detection and alarm system, and any other feature in the building. It’s all expected to work.
FCIA members understand what DIIM means to firestopping. Facilities managers can go to fcia.org for the Barrier Management Symposium, and to find barrier management contractors, manufacturers and inspection agencies.
Bill McHugh is the executive director of FCIA. He assembled and moderated the ASHE/FCIA/TJC/UL Barrier Management Symposium. He also works on the ICC’s building and fire code development processes. Additionally, he chairs the task group for the ASTM International firestop inspection standards, participates in UL standards technical panels and serves on the NFPA’s fire protection features committee. He can be reached at bill@FCIA.org.