Ensuring facility power quality
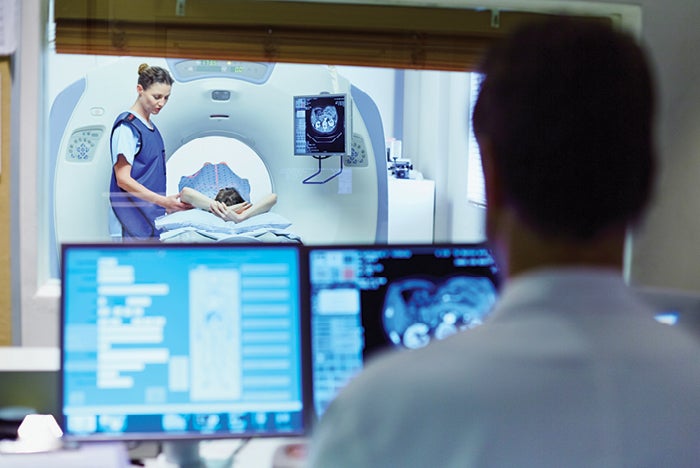
Imaging equipment can be particularly sensitive to poor power quality, and larger imaging equipment also can produce power quality issues that affect other equipment.
Image by Getty Images
Power quality usually refers to the adequacy of a power system’s voltage, frequency and waveform characteristics. In more common usage, power quality is often used to reflect several types of negative impacts that a power system may have on electrical equipment operation. Sometimes, the negative power quality impacts originate within the power system and, other times, they originate from other equipment within the facility.
The phrase “poor power quality” generally indicates that power supply conditions are capable of triggering equipment maloperation or even premature failure. The phrase “good power quality,” on the other hand, means there is a low probability of such contributory events. Because different equipment items have different sensitivities, the same condition may adversely affect one type of equipment while not adversely affecting another type of equipment.
Common problems
Electronic equipment within modern health care facilities can be both more prolific and sensitive than before. Increasing operating speeds can result in circuits being more susceptible to and more capable of emitting electromagnetic interference. Smaller and tighter microcircuits and components are more susceptible than before to overvoltages and other adverse transient conditions.
Imaging equipment can be particularly sensitive to poor power quality, and larger imaging equipment also can produce power quality issues that affect other equipment. Poor power quality also can result in damage to equipment; however, the more serious results often are lost or corrupted data, the adverse effects of downtime and losses in productivity. With interconnected networks, a component failure may propagate to other equipment as well.
Health care facilities also have much more computer-based technology than before. Poor power quality can affect the reliability and proper performance of such equipment, adversely affecting patient care and other important activities.
The most common types of power quality problems include the following:
Voltage deviations. There are a wide range of voltage deviations, including issues such as undervoltage, overvoltage and power interruption.
An undervoltage — also called sag, dip or brownout — is a short-term decrease in voltage from the desired voltage. This event is often caused by simultaneous high-power demand of electrical equipment such as heating, ventilating, air conditioning, pumps, chillers, compressors, elevators and large imaging equipment, among others. Those types of demands often occur when large motors or other equipment such as electric heaters are starting.
A voltage sag also can result from a short circuit — also called an electrical fault — or as the result of a loose electrical connection. Most sags do not adversely affect legacy equipment such as motors, heaters, and incandescent and fluorescent lights, unless the degree or duration of sag is beyond the tolerance of that equipment.
A sag’s impact often will adversely affect sensitive electronic equipment, causing a crash or data corruption. Although a backup battery in a medical device is intended to provide internal backup power during a momentary undervoltage, it probably will not provide protection from voltage transients or other overvoltages.
An undervoltage also might originate from the electrical utility serving the facility. A surge type of overvoltage is a fast-moving temporary voltage increase. Surges can result when high power equipment is turned off, and the extra voltage is then dissipated through the power line to other equipment.
Because delicate electronic devices generally require a constant voltage, surges can stress those components and lead to early failure. A spike is typically an extremely high voltage increase with an extremely short duration.
Spikes can be caused by short circuits, tripped circuit breakers, the discharge of built-up static electricity, lightning strikes or the switching of large sections of a utility network. Spikes also can damage sensitive electronic equipment. A swell is also a temporary voltage increase but not as rapid as a surge.
A transient — also often called surge, spike or impulse — is defined as a temporary rise in voltage and current on an electrical circuit that has been disturbed. Transients are high energy and very short duration subcycle events. Transients can disrupt and severely damage equipment instantaneously or can cause cumulative damage over time resulting in unexplained failures.
Externally created transients typically are caused by lightning strikes, utility grid switching or a nearby business with electrical welding. Internally created transients can be created by turning on or off equipment, with greater load currents creating larger transients. Examples of such internally generated transient sources include static electricity, capacitive loads, loose wiring, differences in ground potential, and switch bounce on motor starters and contactors, among others.
Because power interruptions or loss of power certainly reduce the power quality for some time, that eventuality is also considered in this discussion. Power interruptions — also called outages, power failures or blackouts — occur when either the utility service to the facility or some internal portion of the facility loses its power for a time. Utility outages can be caused by excessive demands on the power system, lightning strikes and other natural disasters, external cyber hacking that affects the utility power system and other types of power system damage.
Another power quality issue is noise on the electrical wiring. This electrical noise is rapid, repeating fluctuations that interfere with the consistent flow of electric power to the equipment. This noise — also called electromagnetic interference or radio frequency interference — can disturb the smooth operation of software programs and result in data errors.
Harmonics. Harmonics and harmonic distortion can be found within the voltage and/or current waveforms as waveform variations.
Harmonics have frequencies that are integer multiples of the waveform’s fundamental frequency (60 hertz fundamental; second harmonic = 120 hertz; third harmonic =180 hertz; and fourth harmonic = 240 hertz). Total harmonic distortion is the summation of all the harmonic components of the voltage or current waveform compared to the fundamental component.
A simple resistive heating element is a linear load that does not create harmonics. Harmonic load currents, on the other hand, are generated by nonlinear loads. Examples of nonlinear equipment include uninterruptible power supplies, computing equipment, office equipment, motor controls, variable frequency drives, compact fluorescent lamps, lighting dimmers, televisions, battery chargers, power factor correction capacitors and, in general, most electronic loads. High levels of harmonics in the current increase line losses and decrease equipment lifetime. Harmonics tend to overheat circuits, especially the neutral conductor. Excessive harmonics can cause some types of electronic equipment to malfunction.
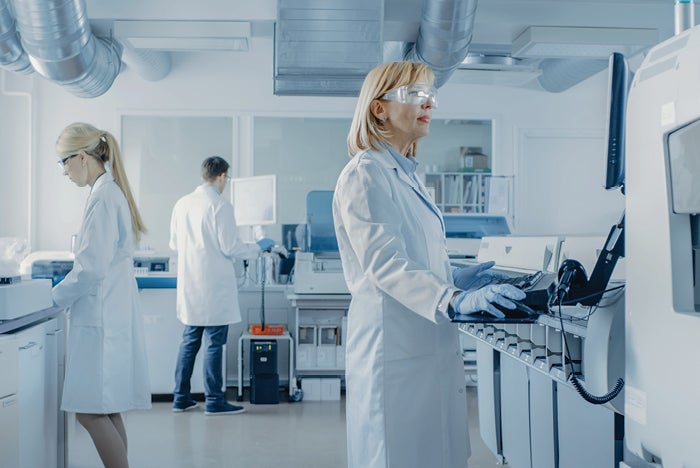
Clinical laboratory equipment such as heaters, coolers, pumps and centrifuges can cause overvoltage impulses and transients, along with high-frequency noise.
Image by Getty Images
Harmonics or distortions in the waveform can travel back into the power source and affect other equipment connected to that same source. As harmonic currents increase, detrimental issues such as overheating of equipment and cables, equipment malfunction and vibration, false tripping of circuit breakers, reduced equipment life, and other adverse results or safety issues can occur.
Voltage flicker (most apparent to humans as flickering lights) is caused by repetitive or random voltage variations in the +/- 10% range. This usually results from machinery with rapid fluctuations in load, elevators and similar equipment. Voltage flickering also can be caused by loose wiring connections.
Clinical laboratory equipment such as heaters, coolers, pumps and centrifuges also can cause overvoltage impulses and transients, along with high-frequency noise. Some common impacts of the above power quality problems may include data errors, equipment failures, memory loss, automatic resets or corrupted software.
A harmonic survey can provide guidance to whether there is a harmonic problem and, if so, where it is located. One approach could be to create an inventory, check transformers for heating, check transformers for secondary current, check the subpanel (load side of the transformer) for neutral current amount and check receptacles for neutral-to-ground voltage.
Finding solutions
A health care facility with suspected power quality issues should be investigated to determine the flow of power to the trouble areas, as well as the other locations and equipment near the trouble areas. An accurate, updated one-line diagram of the facility power distribution system can be very helpful in this regard.
Facilities professionals should interview operations personnel to determine whether new equipment has been connected to existing wiring, whether existing equipment has been moved into another location or other changes. They should assess whether any sensitive equipment is powered by the same equipment as loads capable of generating disturbances. Facilities professionals also should determine whether any construction or renovation equipment is temporarily connected to portions of power systems that also feed medical equipment.
Making sure to follow all applicable electrical safety program requirements, facilities professionals should look at both the normal power system and the essential electrical system items such as panelboards, transformers, power and grounding conductors and terminations, earth ground rod and other installation issues. They also should look for both power connections and ground connections that may be either loose or corroded.
Facilities professionals should compare what they found with imaging equipment manufacturer recommendations if imaging equipment is experiencing adverse power quality conditions. They should assess which different types of equipment are powered by the same panelboard or the same feeder. Portable power quality instrumentation can be very useful in pointing the right direction. Power quality instrument manufacturers can provide useful guidance in selecting and using such instrumentation.
Although the main function of an uninterruptible power supply (UPS) is to provide backup power during a power interruption, some types of UPSs also can provide solutions to power quality issues for the loads they are serving.
A transient voltage surge suppressor (TVSS) or a surge protection device (SPD) are the most-used approaches to mitigate or avoid equipment damage from either externally created or internally created transients. TVSS devices protect equipment from short duration, high voltage events such as nearby lightning strikes or switching of large loads. The SPD is designed to limit the voltage supplied to a protected electrical device. Lightning arrestors also can be used to protect against voltage spikes caused by lightning. Lightning arrestors divert the surge current through the arrestor to the ground.
Harmonic mitigation methods include using double-sized neutrals and K-rated transformers. The double-sized neutrals (or even separate neutrals for each phase conductor) can be used to compensate for the additional heat caused by the harmonic currents within the neutral conductor, and the UL 1561 K-rated transformer is similarly intended to compensate for the additional harmonic current-generated heating. Circuit breakers and panelboards also can be sized to accommodate overheating from harmonics.
Other harmonic mitigation methods also include harmonic mitigating transformers to eliminate the harmonics, active filters that cancel the harmonic current, or passive filters that correct the phase current or convert nonlinear loads to linear. Harmonic filters are devices that are tuned for a specific harmonic frequency and, when installed in a power system, prevent the propagation of this harmonic beyond the equipment that generates it.
Another solution is to monitor, measure and locate power quality issues. Facilities professionals should determine if they have any power quality issues and what type of power quality problems exist. Installing multiple continuous power quality meters in a power distribution system with disturbance monitoring, historical trend logging, harmonic monitoring and transient analyses can help to proactively detect power quality problems.
By detecting issues early, facilities professionals can mitigate them before they grow into worse problems. Some power quality meters are able to capture and view waveforms; detect disturbances, such as voltage sags and swells; measure harmonic power flow; and provide alarms in real time. Power quality monitors also may be integrated into modern power management and control systems.
Power quality monitors can tell facilities professionals whether power voltage and current fall within the equipment’s parameters. If that is the case and the equipment operates incorrectly, follow-up testing of that equipment would be indicated.
Power quality issues do not necessarily cause an equipment failure while the power quality issue is occurring. In fact, it is not unusual for equipment failures to occur sometime later. Therefore, some power monitoring systems can be configured to monitor for power quality issues in real time and alert facilities professionals or clinical engineering professionals to act before failures or medical equipment maloperation occurs. Furthermore, a real-time power quality monitoring system can identify when equipment failures were not caused by power quality issues, but rather by a cause within the failed equipment.
Facilities professionals should consider using the results from a power quality monitoring system (metrics such as voltage surges or sags, currents and harmonic distortion) as triggers for predictive maintenance. They also should consider separating sensitive electronic loads from switchboards, feeders and panelboards feeding other equipment, particularly motors and nonlinear loads.
Demanding requirements
As health care facilities become more technology intensive, they will require sources of power that are less disruptive and unpredictable. Facilities professionals will need to be familiar with techniques discussed above as they troubleshoot and safeguard these power systems and maintain their demanding requirements.
David L. Stymiest, PE, CHFM, CHSP, FASHE, is a senior consultant at Smith Seckman Reid, Nashville, Tenn. He can be reached at dstymiest@ssr-inc.com.