Boilers and chillers for health facilities
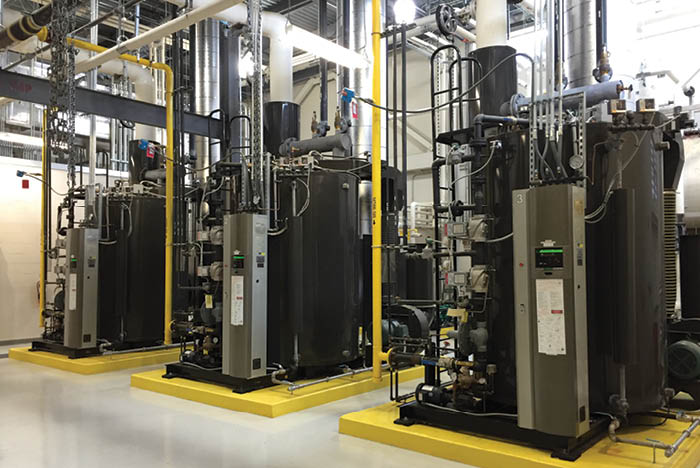
Boilers and chillers have contradictory roles in health care facilities — one technology heats things up, while the other cools things down — but both have a common goal of improving building operations and doing it cost-effectively.
Both also are represented by an army of manufacturers continually working to advance the state of the art to benefit hospitals via new technologies that help improve dependability and efficiency.
Better boilers
Manufacturers agree that smart control interfaces are one key advance in hospital boilers. “New boiler technologies that hospitals are using include color touch screens and lead-lag technologies that provide smart control interfaces to their building management systems,” says Ray Pierce, packaged boiler and national sales manager at Hurst Boiler & Welding Co., Coolidge, Ga. “We see more interest in data collection in everything from feed water temperature to stack outlet temperature.”
Integration of condensing boilers has allowed advanced lead and lag controls that optimize modular (multiple unit) boiler plants to operate together in parallel. “This technology allows multiple burners to run at lower modulation rates where modern condensing boilers are more efficient,” says Kyle Bottorff, product manager at Fulton Heating Solutions, Syracuse, N.Y.
Integration and communication needs have been growing rapidly. Many condensing boiler manufacturers offer integrated cloud communication to the boiler plant, according to Kal Osman, director of boilers at AERCO, Blauvelt, N.Y. “However, due to security requirements of hospitals, many will not allow remote setting changes,” he says. “In these scenarios, offering remote monitoring with alerting ability is important while providing the security of one-way communication.”
Boiler designs with higher thermal efficiencies consume less fuel to produce the same output, thereby reducing carbon footprints. Newer burner technologies reduce NOx (oxides of nitrogen) emissions as well, manufacturers say.
“Newer combustion technologies, such as linkage-less, fuel-air-ratio controls utilize motor-driven valves and actuators, which results in lower excess air burners and the highest combustion efficiencies safely obtainable,” Pierce says. “Benefits include reduced fuel costs and greatly reduced NOx emissions.”
Among systems introduced to hospitals, Fulton Heating Solutions offers the straight gas Endura+ (EDR+) boiler featuring an ultra-compact footprint.
“The high-precision, dual-servo combustion control platform features an O2 compensation system, which automatically tunes the air-fuel ratio while the boiler runs to simultaneously optimize reliability, durability, emissions and fuel efficiency,” Bottorff says.
Hurst Boiler & Welding Co. promotes energy-saving devices such as stack economizers that preheat the boiler feed water temperatures. Other savings can be gained through the use of low excess air burners, variable-frequency-drive boiler feed water pumps and burner blowers.
Benchmark Platinum boilers available from AERCO are designed to operate a combination plant with multiple setpoints while optimizing whole system efficiency. An edge controller manages two boiler groups and their swing valves to separate the two set points. In addition, this design provides several layers of operational security by allowing some boilers to swing between the domestic and space heating groups based on demand and priority settings. This allows boilers to condense without raising the full hydronic system temperature just to satisfy one loop.
Cleaver-Brooks, Thomasville, Ga., recently introduced Prometha IoT Connected Boiler Solutions, which provides an overview of the key parameters of a hospital’s boiler system on web-enabled devices in real time. When a key performance indicator (KPI) is out of range, Prometha provides the user with at-a-glance operational insights.
“Prometha’s user-friendly dashboard can display the most critical boiler operational parameters, including boiler efficiency, water level, operating pressure or temperature, flame signal strength and oxygen level,” says Terry Conger, controls development product manager. “Also, Prometha provides trends for each displayed KPI that can be used to uncover emerging problems and increase efficiency.”
Prometha works with a cellular connection and does not require access to the hospital’s local network, which minimizes the possibility of a data breach, he adds. In addition, the device features one-way communication, preventing any boiler setting from being changed remotely.
Hospitals are required to have power-generation backup plans. When it comes to boilers, they should have N+1 redundancy, an additional backup in case of a unit failure.
“Modular boilers are a great solution to this requirement because hospitals can have a backup of one modular unit versus having a backup of the whole system. This saves money and space in the boiler room,” says Rick Gaston, sales support at Miura America Co., Rockmart, Ga.
Hospitals also are required to have a backup fuel system in case the primary fuel has a shortage or is curtailed by the gas provider. Miura has designed systems to tackle these problems.
“We normally sell our Miura EX Dual-Fuel boiler to the hospital sector because it easily runs dual fuels,” Gaston says. “The EX model has many options that pertain to hospital needs. Miura also decided a few years ago to stock boilers. This includes our EX models, allowing hospitals to purchase a stock model and have it delivered and installed quickly. Miura recently upgraded this program to include some feed water tanks.”
Chiller challenges
Chillers must be able to react quickly to power loss events and get back online to maintain cooling for critical spaces. Another critical issue is maintaining quiet operation with no vibration because equipment rooms are sometimes located close to surgical centers or patient rooms.
New chiller systems recently introduced to the health care field offer many features for improving efficiency in these areas. Also, new climate-friendly systems are designed for use with low-GWP (global warming potential) refrigerants.
Danfoss Turbocor Compressors, Tallahassee, Fla., has developed the Turbocor TGS490, which the company calls the first oil-free compressor optimized for use with low-GWP refrigerants HFO1234ze and R-515B. It offers part-load efficiency ratings up to 24.5 energy efficiency ratio (EER) for integrated part load value (IPLV) for air-cooled chiller applications. This is achieved through optimization of the aerodynamics and the use of oil-free, magnetic bearing technology.
Trane Commercial HVAC Americas, Davidson, N.C., recently introduced the Model ACR, part of its Ascend portfolio of chillers, featuring a full-load efficiency exceeding ASHRAE guidelines of 90.1. “Other air-cooled chillers can deliver good part-load efficiency, but often at the cost of full-load operation,” says Craig Elliott, health care vertical market leader. “Premium levels of full-load efficiency often can drive lower kilowatt (kW) demand charges and possibly lower generator sizing.”
The Model ACR’s part-load efficiency also exceeds ASHRAE 90.1 guidelines, which can help lower utility bills. “The Model ACR offers an optional harmonic filter that minimizes total demand distortion at the chiller terminals to less than 5%,” Elliott says. “Not only can this help with generator sizing, it also can protect sensitive equipment such as MRI machines.”
Daikin Applied, Minneapolis, has debuted the next generation of its Magnitude magnetic bearing centrifugal chiller. Oil-free, magnetic-bearing technology allows it to deliver sustainable efficiency without performance degradation due to oil fouling, according to Garrett Holloway, health care market manager. “The Magnitude is up to 40% more efficient than standard centrifugal chillers,” he says. “Also, the next generation Magnitude will use R-1233zd, a low-GWP refrigerant offering low toxicity and non-flammability for low-pressure centrifugal chillers.”
Carrier HVAC-Commercial, North America, Charlotte, N.C., has expanded its AquaEdge 19DV water-cooled centrifugal chiller line, which is suited to the needs of hospitals. The chiller is capable of processing condenser water temperatures ranging from 40 F entering condenser water to 120 F leaving condenser water. This range is suited for both cold-entering condenser water commonly associated with 24/7 operation and the dedicated reheat loops common in many large health care facilities. Using a chiller for reheating can bring significant savings.
Because heat is diverted to the reheat loop instead of the cooling towers, less freshwater is evaporated at the cooling tower to expel heat outdoors, according to Wayne Garrett, managing director of applied equipment. “In addition, when in cooling mode, the 19DV can operate with condenser water temperatures as low as the 40s instead of the 70s for substantial cooling savings. At 100% load, there is a 35% difference in kW between operating at 75 F and 45 F entering the condenser.”
Multistack LLC, Sparta, Wis., offers large-format, magnetic bearing centrifugal chillers for heat recovery. They deploy the heat-recovery technology the company has perfected but on a larger scale, according to Scott DeGier, director of sales and marketing. “Larger oil-free, multiple magnetic compressors provide high efficiency across the whole load profile. Not only is energy efficiency improved, but a sustainable solution is provided that does not degrade over time. Oil-free magnetic chillers have no metal-to-metal contact and hence no wear, ensuring long-term efficiency.”
The York Solution Outdoor Air Handler from Johnson Controls, Milwaukee, is engineered for outdoor environments where more air handlers are being installed to increase the efficiency of the building space for health care use. Key features include a patent-pending membrane roof system that is warranted for 10 years against water leakage, an integral vestibule to facilitate safe and convenient servicing, and an exterior finish built for long life.
Digital controls and the “internet of things” are key factors driving improvements in chiller systems. Internet of things technologies make it easy to stay on top of chiller maintenance, according to Fawn Staerkel, director of health care strategic accounts at Johnson Controls. The company has partnered with Microsoft, using Azure IoT suite, to build a solution that connects data streams from sensors on critical equipment to the cloud. “This insight into the efficiency of chiller equipment and access to a network of skilled technicians offers fewer disruptions, reduced downtime and longer equipment life.”
Advances continue
As boiler and chiller manufacturers continue their research and development efforts, further advances will likely continue to improve these important workhorses of modern hospitals and health care facilities.
Neal Lorenzi is a freelance writer and regular contributor based in Mundelein, Ill.
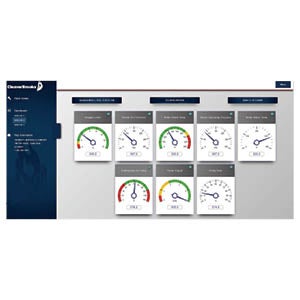
SMART SOLUTION
The Prometha IoT boiler solution displays gauges of key performance indicators in real time on mobile devices. Cleaver-Brooks
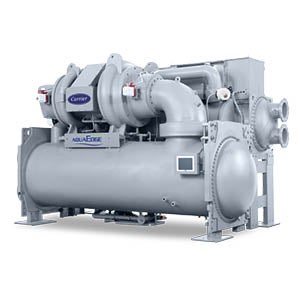
HOSPITAL READY
The AquaEdge 19DV water-cooled centrifugal chiller is well suited to the needs of hospitals. Carrier
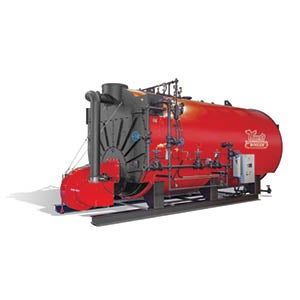
ALL STACKED
These boilers feature the StackMaster integrated and internal boiler stack economizer. Hurst Boiler & Welding Co.
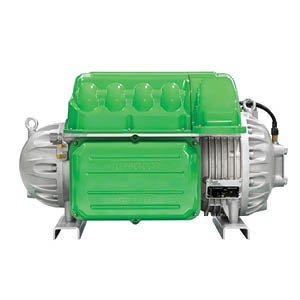
QUALIFIED COMPRESSOR
The Turbocor TG490 is an oil-free, variable-speed, magnetic-bearing centrifugal compressor qualified for the use of R-51B. Danfoss
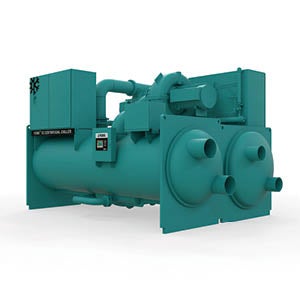
KEEPING IT COOL
The York YZ magnetic bearing centrifugal chiller utilizes a new dual-compressor design to expand cooling capacity up to 2,020 tons. Johnson Controls

NO OIL NEEDED
The Magnitude centrifugal chiller features oil-free, magnetic-bearing technology. Daikin Applied
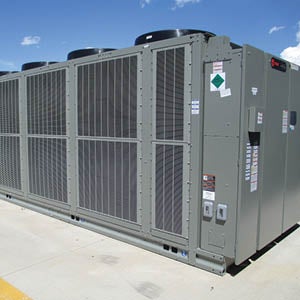
EXTRA EFFICIENCY
The Model ACR, part of the Ascend portfolio of chillers, features a full-load efficiency that exceeds ASHRAE guidelines of 90.1. Trane
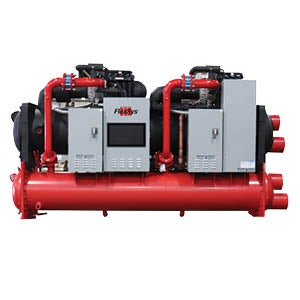
FLEXIBLE FEATURES
MagLev high-lift, magnetic bearing centrifugal chillers in modular configuration offer flexibility in heat-recovery applications. Multistack LLC
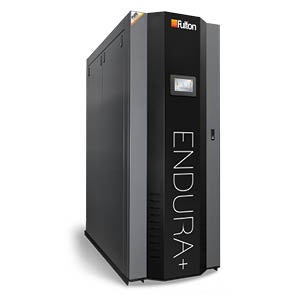
BOILING UP
The EDR+ condensing boiler features a size range from 2.5 to 12 million British thermal units per hour. Fulton Heating Solutions