New boiler and chiller advances for hospitals
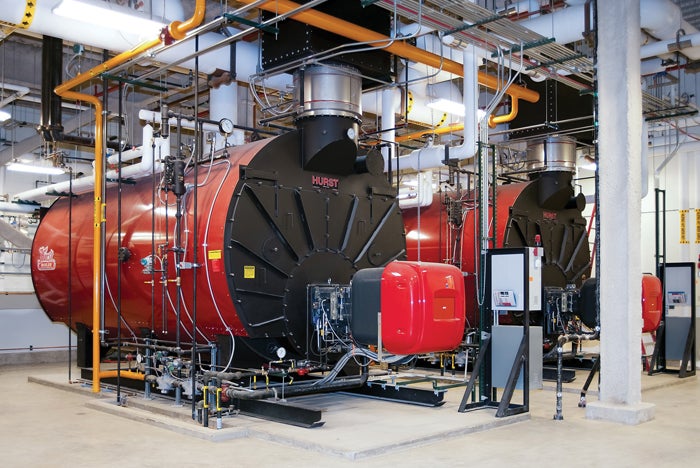
Photo courtesy of Hurst Boiler & Welding Co.
Boilers and chillers have long been the workhorses of hospital HVAC systems, and operating them safely, efficiently and sustainably is a continual challenge for health facility professionals. Fortunately, equipment manufacturers are addressing these concerns in their latest product rollouts, and new generations of boilers and chillers offer many features that can benefit hospitals.
Better boilers
Intelligent control systems that promote connectivity between components and remote monitoring in real time are hallmarks of new boilers. High operating efficiency paired with high turndown rate is another feature. Also, advances in combustion technology have reduced atmospheric pollutants emitted by boilers.
The integration of boiler control systems into building communication networks has allowed for remote boiler monitoring in real time. “Steam pressure, firing rate, stack temperature and alarms are a few examples of common monitoring points that can now be delivered directly to a smartphone,” says Matt Whittington, regional sales manager, Hurst Boiler & Welding Co., Coolidge, Ga. “This allows the operator to address issues quickly and avoid downtime.”
More efficient boiler operation is another hallmark. For example, the Hurst Stackmaster internal boiler stack economizer integrates a stainless-steel heat exchanger into the smokebox section of a fire-tube boiler. The purpose of the internal economizer is to extract heat from the flue gas that otherwise would be wasted and transfer that heat to the boiler’s feed water. By increasing the boiler’s feed water temperature, the unit is able to increase the overall fuel-to-steam efficiency by as much as 4 percent.
“All across the country, boiler-control platforms are requiring more from every module that is attached to them,” says Patrick Villaume, manager of application engineering, Harsco Industrial Patterson-Kelley, East Stroudsburg, Pa. In response, the company has developed the NURO Touch-Screen Control System that monitors and modulates the combustion and ignition of the boiler to maintain a desired outlet temperature.
“Patterson-Kelley NURO controls allow facilities managers to include components such as pumps, sensors and control valves that dictate fixture comfort and maximize boiler efficiency,” Villaume explains. “In addition, it allows remote monitoring of components through a user-enabled NURO Connect feature so that one can observe and analyze data from any location.”
Facility professionals are looking to get away from steam systems with two or three large boilers that are always running to keep up with rapid load swings and maintain N+1 redundancy, according to David Vrana, Northeast division manager, Miura America Co. Ltd., Rockmart, Ga. Instead, they are seeking greater control and monitoring capabilities.
To meet that need, Miura America Co. has developed the BP-201 Master Controller, which allows for seamless load matching with various models to cover a wide range of operating conditions. “Whether that means automatic lead-lag rotation of multiple EX-Series boilers to provide reliable steam with high efficiency on a day-to-day basis, or automatic rotation of a combination of EX-Series and LX-Series boilers for optimal load matching in swing seasons, the BP-201 automatically addresses these changes in steam demand, without the need to waste fuel to keep a full-sized, back-up boiler warm when it’s not needed,” Vrana says.
The CBEX line of boilers from Cleaver-Brooks, Thomasville, Ga., features heat-transfer tubes that are 85 percent more effective than traditional bare tubes, according to Sean Lobdell, director of sales for packaged boilers. “The geometrically optimized furnace of the CBEX enables the boiler to achieve 3 percent O2 across the entire 10:1 turndown range,” Lobdell says. “This means the boiler cycles less, minimizing the purging of energy caused by boiler cycling.”
Controlling the CBEX is the Cleaver-Brooks Hawk, which keeps the boiler and burner consistently operating at peak efficiency with the lowest possible emissions. “The Hawk gives facilities managers the ability to continuously monitor and control a boiler system’s O2 levels, stack temperatures, lead-lag sequencing and water levels to increase efficiency and reduce operating costs while improving operational response,” Lobdell adds.
New boilers are designed to run during natural and man-made disasters. Many are available in dual-fuel configurations, which allow them to operate on both natural gas and an alternate fuel, according to Greg Alcorn, vice president and general manager, Carrier Commercial Systems in North America. “This provides redundancy should the main gas supply be interrupted. In addition, the boiler, along with its pumps and ancillary devices, can be supplied by the facility’s emergency electrical generator should there be any interruption in the electrical supply,” he says.
New boiler designs are greener because they reduce the level of emissions. In fact, advances in combustion technology have significantly reduced levels of atmospheric pollutants emitted by boilers. “These advances have reduced the amount of nitrogen oxide (NOx) in boiler emissions to levels as low as 5 parts per million (ppm). This reduction is significant considering that sub-30 ppm NOx was the benchmark not long ago,” says Whittington of Hurst Boiler & Welding Co.
“As emissions regulations increase, and natural gas and alternative fuels become more readily accessible, hospitals likely will stop using #2 oil,” says Vrana. “Miura’s dual-gas train and biofuel options will assist in this transition toward a cleaner, more efficient future.”
Looking at near-future advances, Harsco’s Villaume says the need for more intelligent controls will continue. “In the next year, items such as maintenance notifications and system health reports will be integrated not only at the building management level, but also at the base appliance boiler level.”
Chilling out
The latest chillers feature higher efficiencies and expanded versatility, providing real-time control of both chilled- and hot-water supply temperatures. Advanced smart controls allow chillers to monitor themselves. Also, new systems are designed for use with low global-warming potential (GWP) refrigerants.
Trane, Davidson, N.C., has expanded its Series S CenTraVac chiller line with the new CVHM model to provide a solution focused on reducing the impact of greenhouse gas emissions through reduced energy consumption and the use of low-pressure, low-GWP refrigerant, according to Mike Patterson, product manager. The CVHM operates with R-514A, next-generation refrigerant featuring an ultralow GWP of less than 2. Higher efficiency is achieved through AdaptiSpeed technology, the integration of a new specific-speed, direct-drive compressor, a permanent magnet motor and adaptive-frequency drive.
Daikin Applied, Minneapolis, has developed the Intelligent Equipment control solution, which helps facility managers track performance and reduce chiller energy consumption from their smartphones. This is part of Daikin’s Pathfinder air-cooled screw chiller with variable-
volume ratio. “The technology constantly adjusts the compression ratio to meet a building’s load demand, maximizing system efficiency no matter the conditions,” says Mark Kearschner, vertical market lead for health care.
Multistack, Sparta, Wis., has expanded its MagLev (oil-free) centrifugal chiller portfolio, providing 60 to 2,500 tons in a single chiller using one to eight compressors. The company also continues to refine its dedicated heat-recovery chiller (DHRC) family to make heat recovery available for various types and sizes of systems. “We can provide heat-recovery chillers from 3 to 1,320 tons in a single chiller with hot-water supply temperatures as high as 175 degrees F,” says Scott DeGier, director of sales and marketing.
Multistack’s newest offering is the air-cooled ARA chiller with integral full-heat recovery, which delivers hot water temperatures up to 135 degrees F. “As with all DHRC chillers, we provide real-time control of both the chilled- and hot-water supply temperatures,” DeGier says.
The York YZ centrifugal chiller from Johnson Controls Inc., Milwaukee, is designed for use with the next-generation of low-GWP refrigerant, R-1233zd(E), delivering up to 35 percent annual energy savings versus traditional fixed-speed, oil bearing chillers, according to Jill Woltkamp, marketing manager, global chiller products. “Unlike conventional, oil-lubricated bearing chillers, the York YZ operates with entering condenser water temperatures as low as 40 degrees F, providing enhanced performance.”
The chiller can operate with evaporator and condenser temperatures inverted. This capability, sometimes called “running upside down,” is when the entering condenser water temperature is below the exiting chilled water temperature. “The inverted operation design of the York YZ eliminates the need for a water-side economizer, which saves money on components, piping, controls and maintenance,” Woltkamp adds.
Carrier Commercial Systems recently introduced the AquaEdge 19DV water-cooled centrifugal chiller platform that utilizes lift-optimization technology. This enables a chiller with excellent cooling efficiency to also provide up to 120 degrees F of hot water, eliminating natural gas consumption, lowering utility costs and reducing carbon footprint. The unit also can provide free cooling.
“The future is moving toward what we call Carrier SMART Service, which uses wireless cellular communications technologies to continuously stream operating data to the cloud in real time, directly from a chiller’s product integrated controller,” Alcorn says. “The data are then captured within Carrier’s ‘internet of things’ platform to provide ongoing insight into the chiller’s health.”
As hospitals continue to focus on conserving energy, chiller manufacturers need to provide systems that increase efficiency, according to Trane’s Patterson. “For example, chillers with heat recovery reduce the ancillary power necessary to reject heat while also reducing the amount of purchased heat required. This reduces operating costs and lowers emissions output through the reduction of burned fossil fuels,” he says.
The new generation of oilless compressors will have a major impact on larger chiller selections, according to Multistack’s DeGier, who says health care is moving toward oilless chillers because of their reduced maintenance requirements and greater lifetime efficiency.
“The market has already moved to standardize medium-range, water-cooled chillers (150 to 600 tons) on oil-free centrifugal technology because it offers a combination of efficiency, minimal maintenance, and sustained operation and performance,” DeGier says. He adds that the larger MagLev oil-free centrifugal compressor offers a higher-capacity (up to 2,500 tons) chiller that can provide the same energy savings on a larger scale.
Neal Lorenzi is a freelance writer based in Mundelein, Ill.
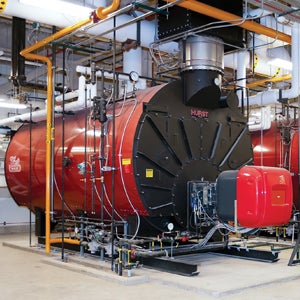
Complete control
This four-pass, high-pressure steam boiler features optional boiler stack economizers, PLC-based combustion controls and electronic, modulating water-level control. Hurst Boiler & Welding Co.
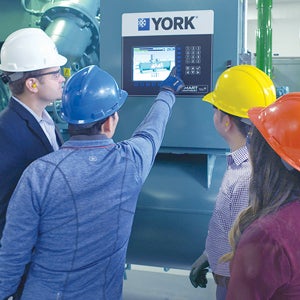
Energy conscious
The York YZ chiller delivers up to 35 percent annual energy savings versus traditional fixed-speed, oil bearing chillers. Johnson Controls
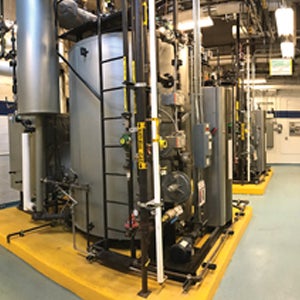
Small footprint
The LX Series low-NOx steam boilers are compactly designed, which makes them easy and safe to install and maintain. Miura America Co.
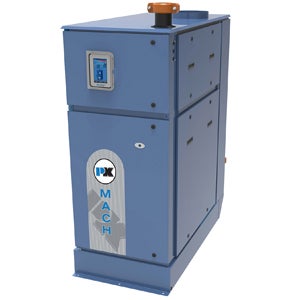
Heating up
The P-K Mach is a high-efficiency condensing boiler that features an aluminum heat exchanger. Harsco Industrial Patterson-Kelley
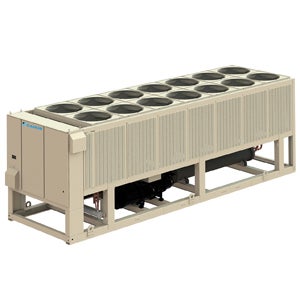
Cooling down
Pathfinder is a high-efficiency, air-cooled screw chiller featuring variable-volume ratio technology. Daikin Applied
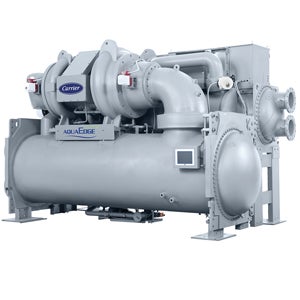
Easy replacement
Carrier AquaEdge chillers are compatible with both R-134A as well as the low-GWP option R-513A, allowing a retrofit of existing commercial products. Carrier Commercial Systems
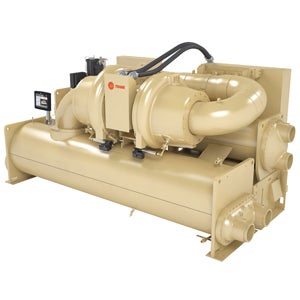
A sure fit
The Series S CenTraVac chiller is designed for a variety of applications, including retrofit and replacement. Trane
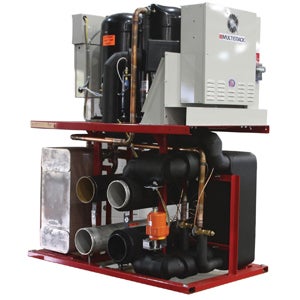
Seamless operation
Dedicated heat-recovery chiller modules with integrated controls are designed to operate efficiently and reliably as a heat-recovery system. Multistack
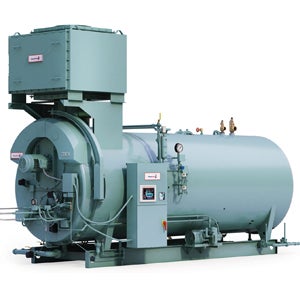
The right shape
CBEX Elite features a larger, geometrically optimized furnace with lower heat release to minimize NOx emissions and improve combustion. Cleaver-Brooks