The benefits of co-locating design and construction teams
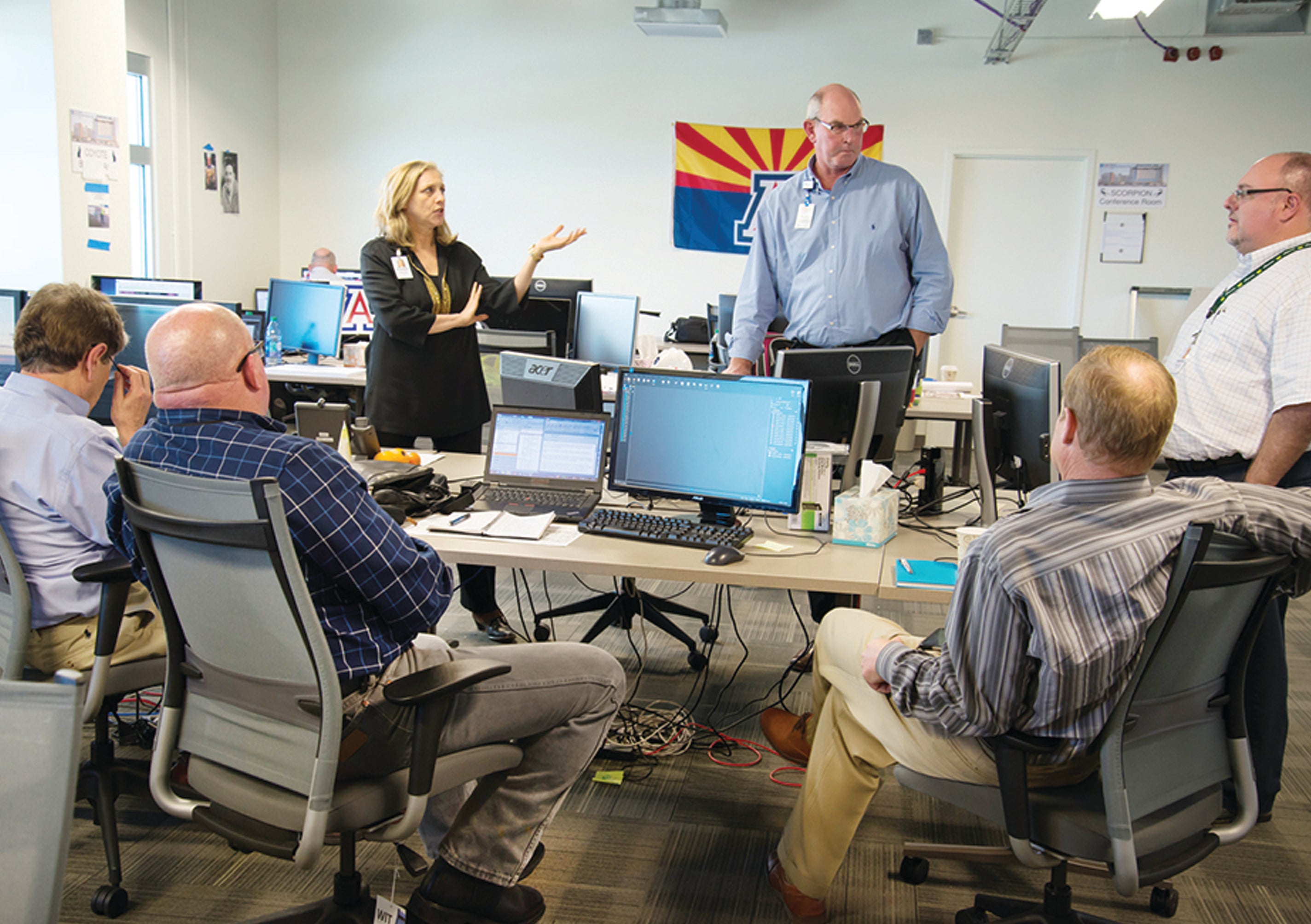
Flexible workspaces promoted impromptu conversations and collaboration throughout the course of the project.
Image courtesy of Shepley Bulfinch
As demand for faster, more efficient and progressive projects across renovations and new construction accelerates, the request for in-person, cross-team collaboration has followed suit.
Co-location holds the promise of significant savings in time, effort and financial resources, while enhancing the quality of the documents, construction process and finished building.
While simple in concept, the practice of design and construction teams working together from a central operations hub requires thoughtful consideration and coordination beyond that of traditional project delivery.
Though it does not require a specific contractual arrangement, at its heart, co-location entails realignment of practices and priorities from that of individual entities to that of the project.
Big-room experience
A project team at Banner Health’s Banner – University Medical Center Tucson (BUMCT) in Arizona recently provided a prime example of a big-room experience during a 670,000-square-foot addition that replaces much of the existing hospital.
Led by the architectural firm, the core design and construction team included a local architecture and engineering firm, a national engineering firm, two construction management firms and Banner Health, based in Phoenix. Additional engineering consultants and subcontractors also participated in the big room.
Comprising nine floors of new construction — including five floors of 240 private critical care and medical-surgical patient rooms — the project consists of labor and delivery, 24 operating rooms and more than 50 imaging, interventional and other clinical diagnostic exam and treatment rooms.
A new main entrance for the medical center, lobby, cafeteria and other public amenity areas as well as a new loading dock, materials management, pharmacy, central sterile processing, blood bank and other support areas complete the new construction. Connections to the existing hospital and medical campus occur on four floors with an additional 75,000 square feet of renovation planned as backfill projects.
Logistical considerations
Unlike many local co-location setups, the BUMCT big room was located adjacent to the site, 115 miles from the Banner Health offices and the lead offices of the prime architect, lead mechanical-
electrical-plumbing (MEP) engineer and one of the construction managers. Though commutable, this distance increased costs (e.g., travel, hotels and meals) and time commitment to the project. However, the benefit of site access and ease of user participation outweighed these problems.
Resources
Initially, two Tucson sites were seriously considered for the big room. The first involved converting an old theater less than a mile away, while the second utilized shell space in Banner Health’s Diamond Children’s Medical Center overlooking the site.
The theater had the advantage of size and adjacent parking, but costs and renovation time proved prohibitive. Converting the shell space in the hospital initially seemed limiting in area for a team of up to 80 people, but its proximity and minimal renovation requirements made it a clear winner.
In time, the selected location proved to be an unparalleled choice. The ability to meet with users, tour existing clinical spaces and point to and walk the site were all unequivocal assets throughout the project.
Organization and leadership
Coordinating many individual firms on a single project is highly complicated. The big room brought key project stakeholders together in one place, including the owner, so that team members could literally turn to one another to get answers, rather than chasing emails, phone calls or navigating different time zones to reach team members.
In addition, multidisciplinary cluster groups were established to further break down large constraints, goals and decisions into smaller components for more efficient communication around each discernable scope of work. Each cluster comprised an owner representative, an architect, a general contractor/construction manager, and a specialty trade contractor who all shared their expertise. The cluster group leader was not necessarily the person with the most expertise or seniority, but the person who could challenge the team to innovate and lead patient-oriented thinking.
One of the best things about the big room was the unexpected emergence of leaders from every firm. Perhaps because co-location creates a brand-new entity with evolving processes and limited or undefined hierarchies, there was plenty of opportunity for individuals to step up and take on new responsibilities.
The BUMCT co-location team saw growth and development across all participants, noting three main qualities of a successful team member: agility, risk taker and the ability to respond to the needs of the project.
Guiding principles
Prior to moving into the big room, a number of mandatory and facilitated daylong exercises were held to allow for camaraderie and shared process development — including rules of engagement, participation and an understanding of the guiding principles:
- Through co-location and the breakdown of individual company silos, team members developed a better understanding of the shared project goals and started making decisions for the good of the project. With time, this fostered trust that everyone had the best intentions for the success of the project.
- In the big room, egos are relinquished and time is spent on collaboration rather than competition with peers. Through this shared vulnerability and open learning environment, strong relationships are established that reinforce a sense of camaraderie where it is safe to take risks and face conflict together.
- The idea that processes could be tried and tweaked for improvement was accepted teamwide early on and essential to the success of the big room. Both monthly surveys and ongoing plus/delta evaluations captured what was working and what required incremental adjustments, minimizing resentment and obstacles for productive workflow. A “half-time show” was also scheduled halfway through the design to allow for reconsideration of processes.
- The nature of the big room evolved based on the progression of the project and key players, but morale was a significant measure of success. Consistent team-building exercises were ways in which the BUMCT team promoted stronger relationships and personal investment in the project.
Scheduling and process
Co-location alone does not solve the problem of how to design and document a project; there must be a process that directs the right input at the right time. The BUMCT team found its solution in a scheduling method called rounding, which worked well on a previous, large bed-tower project for Banner in Phoenix.
Instead of turning the project over in traditional design packages, the building was divided into 40,000-square-foot “rounds” of discernable areas similar in program or structure. Each round on this project was brought from schematic design to construction documentation, and passed among architect, engineer and contractor. Rounding made it possible for the engineers and trades to become involved earlier in the process because the work was completed in segments.
Some of the other benefits included allowing coordination and innovation to take place during design; the ability to fast-track the project; and opportunities for more focused user meetings over a shorter duration.
There were many prerequisites, such as MEP systems having to be designed more holistically and comprehensively, requiring a more traditional delivery method. But, while rounding had its complexities, it was this type of ingenuity that challenged the status quo and fueled the big-room environment.
Lessons learned
Ingenuity and continuous improvement are at the heart of any big room. Logistics were created and customized for the BUMCT big room that provided participants with insight for future co-location projects, including:
- Starting from a blank slate with a small budget, big-room renovations were minimalistic and included lighting and window treatments, carpet, kitchenette fit-out, a mostly open workspace with partitions for conference areas, additional power and teledata provisions, and temperature control. A focal point of the space was access to daylight and views to the project site, which made for a healthier and more productive workplace. Carpeting, while originally deemed a low-value item, ended up being significant. Not only did it make the space more welcoming, it also helped with acoustics and cleanability. While nominal funds achieved big-room objectives, more attention and resources might be paid to power improvements, temperature control and acoustics in the future.
- The big room was made up of three main spaces: workstations, conference rooms and a kitchenette/break room. The majority of the big room comprised workstations (60-70 at any given time) that were created using movable tables that could be repurposed in the hospital upon project completion. This setup kept costs low, but unexpectedly increased flexibility and collaboration.
- The absence of any type of partition shaped a nonhierarchical environment where conversations across work areas and seat reconfigurations were easy. For more organized meetings, there were two enclosed and two open conference rooms. These areas allowed for more private user-group meetings and informal impromptu meetings, respectively.
- In addition, a more costly but valuable kitchenette provided shared space for meals, spontaneous conversation and informal breakouts. The interest and activity in the kitchenette proved its worth in the big room, highlighting a need to re-evaluate size and seating for future spaces — seating for approximately 16 made the kitchenette a bit crammed during high-traffic times.
- Overall, the shell fit-out was a successful use of space. However, future project teams may consider that a lack of small, private areas led to corridor conversations within the hospital; space allocated to enclosed conference rooms was too small based on the number of team members; and open-air conference rooms increased noise levels, at times making concentration and individual work difficult.
- Collaborative technology. Technology played an important role on-site, but also as a connection to people and resources in other locations. The big room was equipped with four large, mobile ClickShare screens, a space schedule monitor, printers and plotters, videophones and two business-class cable internet connections. The greatest technology assets were found to be the ClickShare screens and videophones, which proved to be valuable visual tools both on-site and out of the office. The architectural team also was able to utilize a virtual private network tunnel direct to the Phoenix office network, allowing for seamless connections to phones and digital office resources. However, some teams had to use the health care organization’s wireless system to connect to their respective offices, making access to information difficult.
- The big room’s collaborative, active essence made security an interesting challenge. As a bustling hub of the project, the big room had many visitors throughout the day. However, for the safety of team members and security of equipment, all big-room occupants were badged. A door in the corridor leading to the space had previously required badge access, and the other entrance was adorned with an additional push lock. This provided the team security, but also made visitor access difficult.
- At the commencement of the big room, there was already an increased parking demand for the medical center because much of the site had been a large parking lot. Consequently, there were a limited number of dedicated spaces for big-room occupants, which proved to be vastly insufficient. The old theater, one mile away, was utilized to provide additional parking and occupants were shuttled.
- Staff toilets. Additional toilets were not provided as part of the big-room renovation. As a result, there were too few facilities. Dedicated toilets would be a strong suggestion for any future big room.
The biggest benefit
At the end of the day, innovation is the biggest benefit of co-locating and unleashing that potential is the ultimate goal of a big room.
As with any co-location, there will be things that work better than in traditional models, and things that don’t. The promise is a culture dedicated to continuously improve with the project’s interest at its core.
For these reasons, the project team found the bigroom to be a successful strategy and is eager to advance what it learned on future projects.
Jennifer Aliber, FAIA, FACHA, LEED AP, is principal and Michelle Mantegna, AIA, EDAC, is an associate at Shepley Bulfinch. They can be reached at jaliber@shepleybulfinch.com and mmantegna@shepleybulfinch.com.
About this article: This feature is one of a series of articles published by Health Facilities Management in partnership with the American College of Healthcare Architects.