Using building energy modeling to devise an HVAC plan
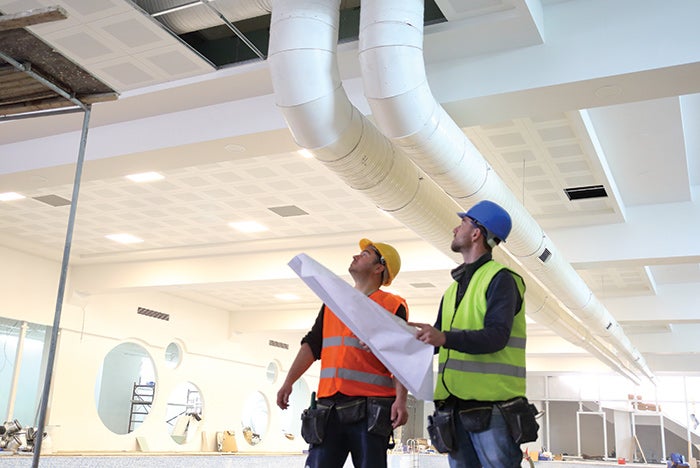
Health care HVAC systems serve many functions, including air filtration, dilution and removal of indoor pollutants through code-mandated air-change rates of supply and outdoor air, as well as the precise control of space temperature, humidity and pressurization.
These requirements are extensively described in the American Society of Heating, Refrigerating and Air-Conditioning Engineers (ASHRAE) Standard 170, Ventilation of Health Care Facilities, and contribute to the mechanical systems being among the largest portions of most health care facilities’ construction budgets.
While it is crucial to provide a healthy, comfortable environment for patients and staff, to be high-performance HVAC systems, they must accomplish this by the most energy-efficient methods feasible.
You may also like |
2015 Sustainable Operations Survey |
HVAC systems rise to health care’s demands |
2011 Energy Management Survey |
|
Building energy models can help. They have been used for years to help design teams comply with local building codes, utility incentives or beyond-code programs such as the LEED rating system.
When they are reserved for use until the very end of a project, they can be seen as simply a necessary evil to satisfy the requirements of a code official or U.S. Green Building Council reviewer. However, when used during the design process, energy modeling is one of the best tools that engineers have to design high-performance, cost-effective buildings and HVAC systems.
Energy model uses
In general, building energy models can be used for three different purposes, depending on how a model is built, the required effort to build it and the value gathered from it. They are:
To demonstrate compliance. For decades, energy models have been used to deviate from the prescriptive design criteria of the energy code by demonstrating that such deviations will result in annual energy consumption equal to or less than that resulting from compliance with those criteria. This asks the user to create a model of the proposed design described in the documents and compare that to a model of a hypothetical baseline design based on specific performance criteria. A different baseline may be required, depending on whether compliance is desired for tax credits, LEED certification, local codes or utility incentives.
To inform design. Energy models can be used as a comparative-analysis tool during the design process. Models can and have been used to evaluate the benefits of potential energy-conservation measures, uncover counterintuitive building relationships, identify synergies to reduce mechanical and electrical system sizes, and find areas of highest potential impact. They also are a key ingredient to a life-cycle cost analysis.
To provide predictions. Estimating utility costs is a legitimate concern for building owners but, unfortunately, energy models are not great at predicting the actual energy use in buildings with a high level of accuracy, especially for new construction projects. This is because many unknown variables are outside the energy modeler's control and can have a significant impact on performance, such as variations in occupant behavior patterns, system control, maintenance, scheduled building use, weather and energy rates. However, an energy model may begin to predict energy performance where a range of anticipated energy performance is based on a sensitivity analysis of key unknowns or where a model of an existing building has been calibrated to an acceptable margin of error based on at least 12 months of actual energy performance.
Modeling a system
In an integrative design process, a few things should be done before analyzing system options, such as defining the health care organization's project requirements, identifying climate- and building-specific design strategies, and reducing cooling and heating loads .
The next logical step is to decide which HVAC system is appropriate for the facility. Codes and standards for health care facilities require HVAC systems to meet particular criteria for filtration, ventilation, air circulation and thermal comfort.
Traditional design methods can be utilized to show that multiple HVAC system types can meet these functional requirements. However, because buildings react dynamically to changes in weather and internal loads, a tool such as an energy model must be used to show which system performs more efficiently during a typical year of operation. Facilities professionals must consider the following:
Equipment load capacity and distribution. All mechanical design engineers with more than a few months of experience have calculated heating and cooling loads. Typically, these calculations take into account preferred indoor design conditions, worst-case outdoor design conditions and appropriate inputs for the building envelope and internal loads. Then, by choosing design temperatures for air and water, appropriate flow rates are calculated.
However, this does not always ensure that thermal comfort is maintained throughout the year. Controls that reset supply air temperature setpoint based on outside air temperature or grouping rooms with drastically dissimilar usage patterns on the same thermostat can create discomfort at times. Rather, an hourly, annual simulation of the building’s operation can identify these potentially uncomfortable conditions resulting from unmet load hours. With this knowledge, duct sizes or design airflow rates can be adjusted or problem areas can be more appropriately zoned.
Equipment efficiency. Knowing the rated equipment efficiencies within an HVAC system is crucial to judging its energy performance compared with other systems. However, it’s important to recognize that manufacturers often list efficiencies, such as coefficient of performance (COP), energy-efficiency ratio and kilowatts per ton, in terms of rated conditions dictated by equipment standards. These conditions may differ from how the equipment is being designed to operate, resulting in a lower operating efficiency.
For instance, the Standard 550/590, Performance Rating of Water-chilling and Heat Pump Water-heating Packages Using the Vapor Compression Cycle, published by the Air-Conditioning, Heating, & Refrigeration Institute, certifies the efficiency of water-cooled centrifugal chillers at test conditions of 44 F leaving chilled-fluid temperature at 2.4 gallons per minute per ton (gpm/ton) evaporator fluid flow, and 85 F entering condenser-fluid temperature at 3.0 gpm/ton condenser fluid flow.
A potential problem may occur if the design engineer selects a chiller with a rated efficiency of 6.28 COP but an operational efficiency of 5.79 COP because of operating conditions of 42 F leaving chilled water and 2.81 gpm per ton condenser water flow. Having an energy model that can take rated and operational efficiencies into account is crucial for accurate comparisons between systems.
Part-load performance. While HVAC systems are sized for worst-case conditions, they only operate at these levels for a few hours a year. The rest of the time they operate at part-load conditions, and both the capacity and efficiency of the equipment are affected as ambient conditions and equipment operation vary.
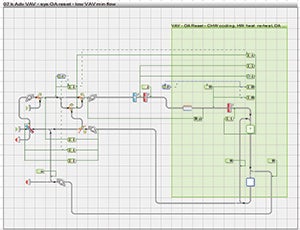
Energy models can be used during design to test potential control sequences for their ability to save energy while maintaining adequate indoor environmental quality.
Graphic courtesy of Clark Denson, P.E., CEM, BEMP, LEED AP BD+C
Traditionally, part-load performance of equipment such as chillers has been represented by polynomial equations — typically quadratic, biquadratic or cubic — developed from regression analysis of the manufacturer’s published design data. For instance, chiller capacity can be represented by an equation as a function of leaving chilled-water temperature and entering condenser-water temperature. Additionally, chiller efficiency can be represented by a combination of two different equations: one as a function of leaving chilled-water temperature and entering condenser-water temperature, and another as a function of part-load ratio.<
To adequately evaluate the energy performance of an HVAC system at part load, an energy-modeling program must be capable of using these part-load performance curves. The challenge is that not all manufacturers have processes in place to readily provide this information, and there is no industry-standardized method of consistently representing part-load performance data across a wide variety of equipment categories.
HVAC controls. Despite the known benefits of keeping HVAC system operation simple, modern energy codes and the desire to design ever more efficient buildings have increased the complexity of HVAC controls. With energy simulation, modelers are able to provide a new and important service of “pre-commissioning.”
For instance, aggressively resetting supply air temperature setpoints in a multiple-zone, variable-air volume air-handling unit during part-load conditions can save significant amounts of cooling and heating energy. However, it can potentially result in unacceptably high indoor humidity and increases in fan energy that negate other energy savings. Rather than waiting for equipment to be installed before testing, energy models allow for controls to be tested and optimized during the design process to ensure that buildings save energy and maintain adequate indoor conditions at both full-load and part-load conditions.
Analyzing the options
Even though energy analysis can show that some strategies — such as load-reduction measures — save both first costs and energy costs, high-performance HVAC systems often have higher first costs than other designs. As a result, projects tend to use cost-benefit analysis to justify these higher costs. While the three-year payback period is a common metric for judging cost effectiveness, its limitations are that it results in solutions with quicker returns but not necessarily the most value over the life of the solution, and it does not take into account the time value of money or fuel-cost escalation rates.
An alternate and more robust financial analysis is the life-cycle cost analysis, which is meant to find solutions that maximize wealth but not necessarily the fastest return of capital. It takes into account capital costs, energy costs adjusted for fuel-cost escalation rates, operating and maintenance costs, replacement costs and the salvage/residual value of potential solutions over the lifetime of the project. It then discounts future costs and benefits to a present value using a discount rate or the interest rate that the facility uses to make financial decisions. The solution with the lowest life-cycle cost over a given study period is deemed to be the most cost effective.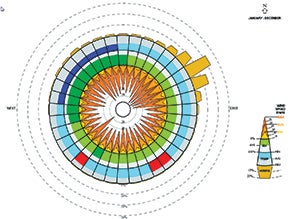
Studying the local climate and energy-consumption patterns in a prototypical hospital can identify project-specific strategies to be investigated further.
Graphic and chart by Clark Denson, P.E., CEM, BEMP, LEED AP BD+C
To make well-informed decisions, facilities professionals should use the results of their financial analysis in conjunction with a comparison of qualitative properties for each HVAC system alternative. As a best practice, this qualitative comparison should be a collaborative, team effort among the architects, engineers, contractors, owners and operators of the facility because they all may have unique knowledge and perspectives. Facilities professionals should consider the following steps:
Decide on the HVAC systems to compare. Ensure that each system that warrants further discussion already meets key criteria within the health care organization’s project requirements.
Decide on the criteria. Have team members list important aspects of any HVAC system. This likely may include quantitative criteria such as first costs, life-cycle costs and potential LEED points than can be determined objectively as well as qualitative criteria such as controllability, redundancy, spatial requirements, security, acoustics and maintainability.
Prioritize the criteria. Allow team members to prioritize each criterion as necessary, with higher priorities being numerically greater and potentially eliminating criteria that are unimportant by giving them an importance factor of zero.
Rank each system under each criterion. Have team members discuss the advantages of each system alternative. Then apply a numerical ranking to each system for that criterion, with higher numbers signaling a higher preference.
Calculate the score for each system. Once all criteria have been discussed, the importance factor of each criterion is multiplied by the raw ranking for each system alternative. Then, these adjusted rankings are summed to give the overall score for each system. The system alternative with the highest score is deemed to be the preferred system.
While this process is not perfect, it can allow quantitative and qualitative criteria to be compared together. And, by soliciting the opinion of multiple project stakeholders, it builds consensus and reduces individual biases toward one system over another.
Upcoming standards
Getting accurate part-load performance data for HVAC equipment in a consistent data format is a challenge, but the ASHRAE Standard 205, Standard Representation of Performance Simulation Data for HVAC&R and Other Facility Equipment, still under development, is likely to make this easier. Likewise, the ASHRAE Standard 209, Energy Simulation-aided Design for Buildings, also under development, will emphasize that the exercise of modeling various HVAC system types is an important part of designing a high-performing building.
Clark Denson, P.E., CEM, BEMP, LEED AP BD+C, is building performance engineer at Smith Seckman Reid Inc. in Nashville, Tenn. He can be reached at cdenson@ssr-inc.com.