Temperature monitoring system keeps meds safe
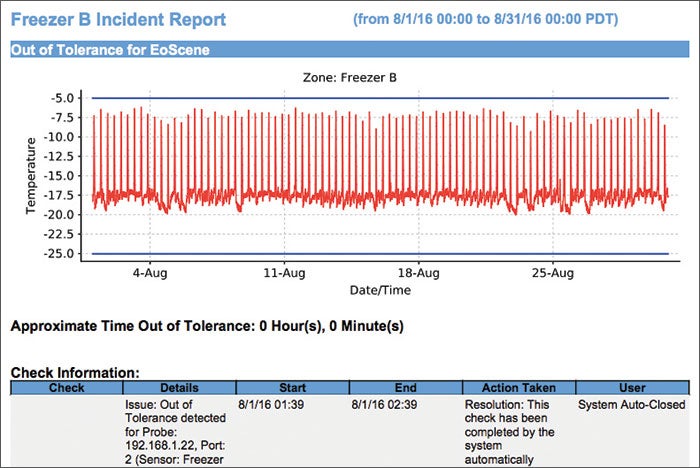
The automated system provides real-time and historical reports of all automated temperature data collected to ensure compliance with CDC guidelines.
After too many out-of-tolerance temperature alarms had ocurred without notification or follow-up on critical vaccine inventories, Jim Cartwright, facilities supervisor at Bend (Ore.) Memorial Clinic (BMC), knew it was time to find a reliable solution.
Cartwright needed a temperature-monitoring system to cover 58 refrigerators and freezers across five clinics that provided real-time alarm notifications to multiple managers and supervisors on their work phones. He could no longer risk having to rely on a text alarm being sent to a single location.
When a temperature threshold was exceeded, Cartwright also wanted a system that produced the required regulatory and audit documentation within seconds, ensuring timely evaluation of the safety of the medicine.
As in many organizations, one of BMC’s biggest temperature-management challenges has been the manual staff activities required by the Centers for Disease Control and Prevention (CDC) and local health departments to ensure the validity of automated systems as well as analysis and documentation of temperature readings.
Moreover, Oregon Public Health requires notification of vaccines stored outside of appropriate ranges and can request complete temperature logs at any time. Temperature logs are required to be documented and maintained for a minimum of three years in Oregon and sometimes longer in other states.
BMC increased its temperature management visibility, compliance and patient safety by implementing the EoScene AssureTemp automated temperature management system.
Along with immediate out-of-tolerance temperature notifications, EoScene's system provides real-time and historical reports of all automated temperature data collected, and also a scheduling and notification system to ensure that daily manual checks are completed and documented according to CDC guidelines.
By utilizing the data and reports provided by the system to establish a temperature-management process baseline, BMC also used Lean management principles to reduce costs and make process improvements to its patient care delivery.
Data provided by the new temperature-monitoring system enabled BMC to identify and replace faulty equipment, determine where process capabilities were inadequate and identify problem departments.
Reliable alarms with facilitywide access enabled facility staff to eliminate time-consuming calls in response to possible equipment problems. Cartwright used reports to identify problem areas and decrease alarm events by more than one-third over a recent four-month period.
“AssureTemp’s temperature graphs make it easy to create reports on waste, broken into seven components. We identified the number of alarms generated over the past year and the departments that were responsible for most of the events,” he says.
Cartwright says the information enabled them to determine that the staff weren’t utilizing refrigerated equipment locks properly, which precipitated staff education and training to eliminate the dangers of leaving doors open or unlocked.
By determining the root cause and correcting the problems, BMC stopped sending critical facility-maintenance employees to close refrigeration units and, more importantly, reduced the number of after-hours, on-call incidents.
Establishing a baseline and determining areas for improvement are essential to the Lean process-improvement methodology used by BMC. EoScene supports Lean initiatives by providing a tool to measure compliance to specific policies and procedures as well as collecting data and involving staff as needed to complete work, and to measure and evaluate process improvement.
Cartwright and BMC plan to continue utilizing the system’s Lean improvement reports to identify additional waste components to be able to make process-improvement recommendations to management.