Moving from hospital construction to daily operations
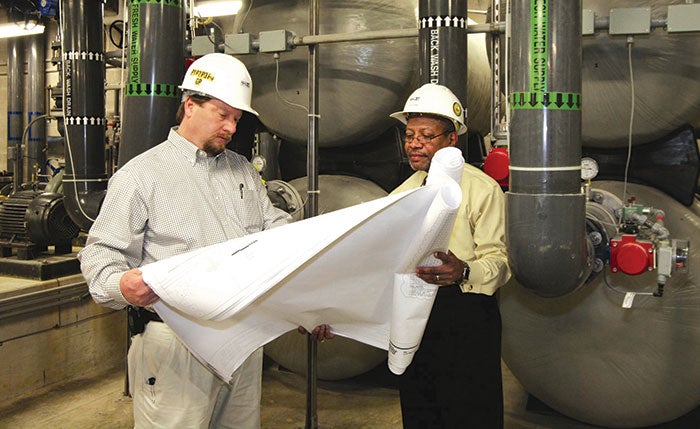
A post-occupancy program may include retaining one of the key design/construction team members to remain on-site to drive home system training and operations.
A health care organization constructs a world-class medical facility, taking all the right steps, setting all the right goals and allocating all the right resources. The project is designed and built, systems and components are started up and their performance validated, and system integration is coordinated and verified.
Building automation and control systems receive sequence-of-operation procedures and testing. Commissioning is executed, confirming successful overall compliance with owner requirements and objectives. Regulatory compliance is completed and certified. Operations and maintenance (O/M) staff receive basic systems training, and the facility is equipped and occupied.
And yet, somehow, within the first year of operation, the organization begins to notice faltering building performance, including high energy consumption, occupant complaints and subpar control system function.
What happened?
As a once-efficient and well-tuned facility begins to degrade, a health care facilities professional is left to wonder what happened between construction and occupancy and, more importantly, how to get the facility back on track.
Also in this article |
Health care’s speed-to-market challenge |
|
Based on evidence from a series of postmortem project debriefs and interviews with design and construction executives, major contributors to this situation are industry-standard training that historically has focused on specific system components one at a time, or each system at a time, often missing the critical integration and interoperability between components and systems; the push to lower facility operation costs, leading to leaner O/M resources, requiring individual staff members to cover more square footage and maintain tighter schedules; and the exploding complexity of engineered building systems and automated controls.
With regard to facility staff, training on the integration between the mechanical components within the building automation system (BAS) often gets overlooked. In one case, for example, training for a new facility with a geothermal ground source heat pump system did not adequately cover integration between the heat pump chillers and heating components, between the chilled water and condenser water components, nor between the heat pumps and the ground loop controls. This resulted in periodic loss of environmental control and a general sense of system instability.
Additionally, training often fails to include how the BAS is integrated with the fire alarm system and fire protection system so that alarms in one system trigger proper responses from other systems. There also is a timing component, because without O/M staff exposure to live conditions and real-time events prior to contractor-to-owner transition, training tends not to be absorbed and much of the initial knowledge tends to degrade. The speed-to-market dynamic of most health care projects [see sidebar, below] amplifies this factor.
Expanding on the impact of leaner O/M resources, time available for staff to engage and learn new facilities being brought online is limited, if available at all. Staff members typically have regular duties and generally are considered too busy to engage in learning the new project. For new expansion or greenfield facilities, the maintenance staff often are brought on board just in time to begin operations, to minimize labor costs. Not enough time is devoted in early project stages to learn and understand system concepts as they are developed and as the design progresses. O/M staff are more likely handed a facility with systems they don’t understand or know how to manage. And with the increased complexity and integration between systems, this has become a bigger impediment.
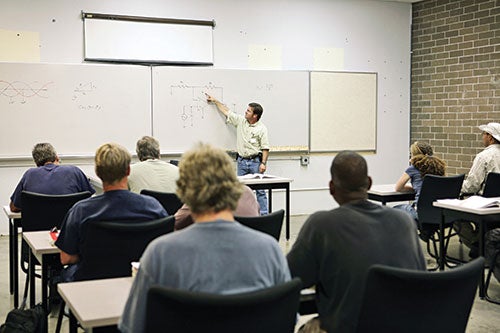
A robust training program includes mandatory training sessions for all staff members responsible for system operation and management — including night staff.
Additional contributing factors include:
- The first year of operation coincides with the traditional one-year warranty period and many issues get pulled into the dispute arena where the issue resolution process often becomes a distraction for O/M staff trying to learn the systems.
- Difficulty in pinpointing specific causative factors, and whether problems are related to individual components (and their respective vendors) or related to the overall integrated system at large, have significantly different resolution challenges.
- Exact implementation of clinical processes and the planned patient care delivery model into live case load conditions often translate into different demands on the facility infrastructure and layout.
- Facilities that often open to a full census and heavy patient load can tax systems while still in the startup and initial operational phases.
Finally, computer systems are programmed to integrate performance of the environmental equipment — performance that is dependent on programming, integration, device calibration and device communication. When any of these critical elements fails, fails to communicate or its performance is changed by other factors, it will impact the facility environment. The response of maintenance staff who are not properly trained can be as detrimental to system performance as the failure itself.
A radical approach
Facilities built today can be considered radical in terms of advanced building systems and technology compared with facilities of 20, 15 or even 10 years ago. These modern facilities cannot be supported by a training and education program for O/M staff that is any less radical. The structure, content and delivery of such a program have to be radically different from simply scheduling various vendors to make generic presentations on their systems and equipment, some of which might not be tailored to the exact scope of the project.
One proposed solution would be the development of an integrated education curriculum that includes not only vendor- or system-specific information, but also focuses on facility system operations at the macro level. Rather than typically being led by the contractor and related vendors, this effort would be led jointly by those responsible for creating and delivering the project for the owner, and those who know the project the best: the engineer of record (EOR), installing contractors and the commissioning agent (CxA).
The radical aspect of this approach is that it will cost more money and require a remarkably deeper level of commitment. But, one must consider the costs of not doing it. Owners are investing in sophisticated and complicated systems to achieve high-performance buildings. If the costs of a commensurate education and training program seem radical, the costs of poor performance are even more so.
A comprehensive education and training program might include the following:
- Collaboration between the EOR, builder (i.e., mechanical-electrical-plumbing coordinator and major subcontractors) and CxA to identify specific, critical education needs, such as those aspects of the project design and function that are imperative to get right.
- Determination of the basics of an overall curriculum in terms of what information is needed and who will deliver, combining the expertise of vendors and installing subcontractors with the overall vantage of the EOR and CxA.
- Material that addresses detailed review of design concepts and overall system layouts, including measurement and verification means and monitoring requirements; review of expected system performance; system operations in normal mode and emergency or error/failure mode; specific vendor training, component by component; and particular focus on system overlap, where systems interact and integrate in terms of operational responses.
- A detailed delivery schedule of information, based on project specifics, that considers design-phase reviews before and during construction; training on system basics prior to initiation of the commissioning (Cx) process; training on system operation during the Cx process to allow staff to witness proper operation so that they recognize improper operation; and repeated follow-up training 30, 60 or 90 days after occupancy to follow up on specific issues and reinforce proper system operations.
- Coordination and integration with the overall project activation schedule, which will require early planning and understanding of project phasing.
- Determination of critical staff to be involved and allowances for being sequestered for periods of intense system training without interruption or distraction.
- Consideration for evaluation and testing of O/M staff at key points in the process to determine retention and application of training material, including the development of system performance scenarios that would require response and correctional action from the O/M staff to use as learning opportunities.
- The retention of one of the key design/construction team members to remain on-site full-time for a 30- 60- or 90-day period to drive home system training and operation.
You may also like |
Working with AHJs on building projects |
Hospital construction success factors |
Commissioning for hospital infrastructure systems |
|
Covering the basics
A robust training program also must make sure that the basics are covered first. This includes videotaping all training sessions and archiving them for future staff. It also includes making training-session attendance mandatory for all staff members responsible for system operation and management — including night staff. If necessary, live sessions should be repeated to cover all staff members.
Facilities professionals should demand accurate and detailed O/M information ahead of project turnover. This information must be project-specific. It must detail the integration of systems and not silos of information stored individually. Serious consideration must be given to requiring more sophisticated facility management tools with special interrelated documentation and embedded equipment and system information.
There is no substitute for allowing the O/M staff to learn system concepts and layouts as the design progresses and as the systems are installed. Staff frequently report that the first time they have any exposure to the systems is when they take possession and are expected to manage them. Purposeful design review meetings with the EOR, testing procedure overview and observation with the CxA, and periodic project walk-throughs with the project team are simple yet powerful steps toward a successful start-up period.
Facilities professionals also should use a predictive, control system monitoring service to provide daily review of system setpoints, actual conditions and possible conflicting data points to pre-empt and avoid issues. This tool would be monitored by the EOR or CxA. This process offers real-time control point data feedback and identifies negative system trends and inefficient operation before they impact utility bills and almost before the staff is aware of changes in the environment.
Such assistance offers the O/M staff daily access to professionals who know how systems must operate and how they are required to perform. It is effectively an on-the-job training program that allows staff to become familiar with these complex systems while being able to rely on someone for support. This approach bridges the gap during the most critical initial stages of occupancy and teaches the O/M staff how to respond to issues without overriding the intended efficiencies and integration.
The bottom line is to create a strong sense of ownership on the part of the O/M staff. From being part of the design process, to receiving training and development, to being empowered to make educated decisions about the systems, these types of radically different approaches to O/M training offer the best chance for the staff to be diligent and proactive in managing the systems to peak performance.
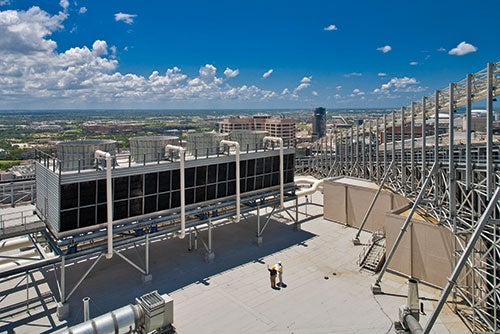
This cooling tower array at Houston Methodist is a critical component of the HVAC system and operational training must integrate the overall central plant control strategy./p>
A top-notch facility
Successful transition from construction to operations requires an integrated team of designers, builders and commissioning agents to deliver a top-notch facility and an educated and prepared team of facility operators and managers ready to maintain the facility’s high performance.
In a rapidly evolving environment that assumes improved patient outcomes with lower risk and dramatically lower cost, expectations are no less for capital projects and the resulting built environment.
Facilities professionals cannot afford to allow this transition to be the weak link in an otherwise strong and successful project delivery process.
Rusty Ross, PE, LEED AP BD+C, CxA, EMP, is principal and Clay Seckman, PE, HFDP, is senior principal with Smith Seckman Reid Inc., Nashville, Tenn. They can be reached at rross@ssr-inc.com and cseckman@ssr-inc.com, respectively.