ASHE draws blueprint for planning, design and construction
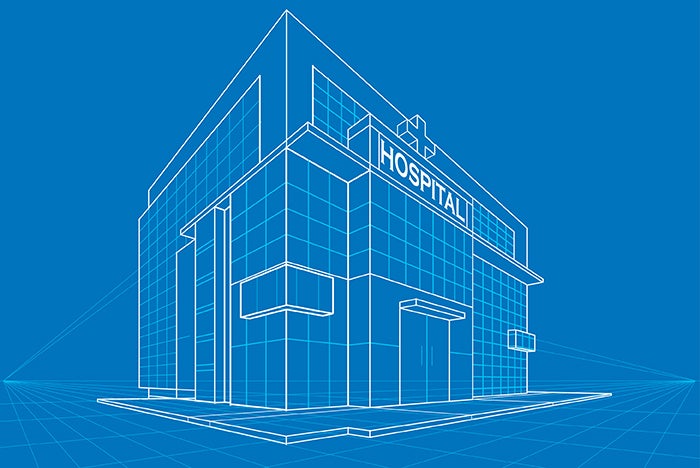
Image from Getty Images
For a health care organization, and especially its facilities department, construction is often a highly anticipated event — the culmination of hope, ambition, fundraising and public awareness campaigning, all of it driven by a desire to better serve the needs of the local community.
Many individuals will play key roles in the project: owner’s representative, planner, designer, builder, facilities manager and others. All are important in achieving a successful completion.
Released earlier this year, the American Society for Health Care Engineering’s (ASHE’s) The Facilities Manager’s Handbook for Health Care Project Management lays out these processes and flow.
It takes a sequential approach to each topic, addressing planning first, then the various design phases, construction of the project, and the operations and management throughout the project and afterward.
The ASHE handbook, from which this article is excerpted and edited, is organized into five parts, each detailing a major step in this process.
Planning
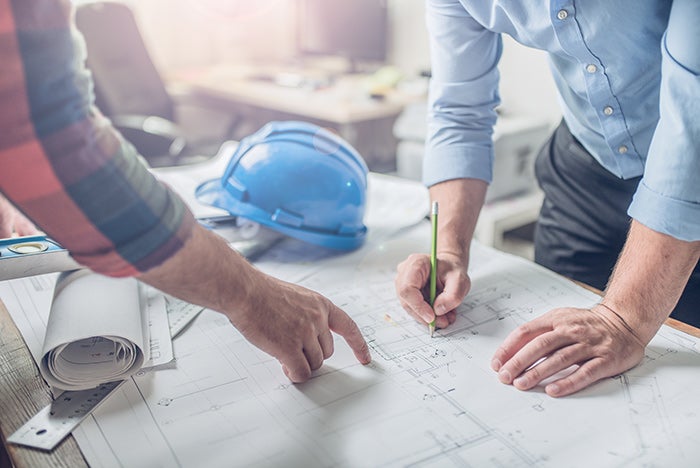
Image from Getty Images
Working with an organization’s thought leaders from the outset establishes a baseline and understanding of how a project fits into the overall strategies of the organization. Planning is also the right time to establish measures of success for the project and the processes needed to meet these measures.
Project planning and design processes have a few consistent key elements. These include upfront planning and budgeting, assembling the right team and using that team well throughout the process.
Master planning. Each health care organization should, and many do, establish long-range or master plans that articulate goals for the organization’s services and the facilities that house them. These are usually tied to an in-depth business plan and are accompanied by strategic plans that set a timetable and identify tactics or strategies for achieving their aims.
The decision to engage in a capital improvement project may result from a range of facility needs. While most building programs comprise maintenance efforts, renovations and additions, rather than completely new facilities, a long-range plan is a critical element in the process.
When preparing for facility construction or renovation, planners should undertake a thorough analysis of multiple factors, including the community, existing facilities, feasibility and physical site.
Creating the functional narrative. The functional narrative articulates the health care facility’s priorities: operational intent, staff requirements, care model, and desired patient and resident outcomes. It explains why the proposed construction project needs to happen and how it will benefit the organization and enhance its ability to serve its patients and the community.
A functional narrative document should be created as early in the process as possible so that leadership can make the operational, financial and business decisions that influence design and construction.
- Pre-construction risk assessment (PCRA). Owners will require a thorough PCRA that considers a variety of factors that impact the facility and its occupants both during the process of construction and in the final product after work is complete. A PCRA considers the full range of people who might be present during construction. It also considers potential damage to structures and equipment. While a new build may not need to contend with a health care organization’s daily business, a PCRA of remodeling and addition projects must consider the ongoing need to provide care.
Infection prevention. Infection control is another concern that escalates with the decision to replace or reconstruct portions of a building or to build an addition. Health care-associated infections (HAIs) are a major concern in a health care facility’s day-to-day functioning, and the disruptions caused by even a modest construction project increase this risk.
To combat this, the owner establishes an infection control risk assessment (ICRA) team. The ICRA, at a minimum, will address any potential airborne or waterborne transmission of biological contaminants during the construction and commissioning of the project. Infection control measures should also be considered when the project is a building addition, even if there are no occupants nearby, to minimize infection control issues during future renovations.
The owner should prepare the ICRA but review it in detail with the architect and the contractor. This work is often done using the ASHE ICRA 2.0™ Toolkit. More specific guidelines for infection control risk mitigation recommendations (ICRMRs) can be found in the most recent versions of the Facility Guideline Institute’s Guidelines for Design and Construction documents.
Project phasing and logistics. The phasing of a modernization program must be worked out in close cooperation with the administration of the health care facility. Expected phases should be carefully spelled out in the contract documents or project narrative and specifications no matter which delivery model is determined to be best for the project.
When preparing for the renovation and expansion of an existing structure, a logistical analysis of systems and patterns of circulation must be undertaken. Areas of new construction must be compatible with current, optimized logistical patterns.
Construction planning also provides an opportunity to reexamine existing patterns with an eye to modifying and improving programmed supply systems. Patient, staff and visitor traffic flow should also be carefully studied.
Building commissioning. Building commissioning is the process of determining that systems have been designed, installed and functionally tested for effective operation and maintenance to meet the owner’s operational needs.
Commissioning should be part of the conversation at each stage of the process. Research cited in the ASHE handbook indicates that commissioning “remains a cost-effective way to improve the operation of your building while lowering energy use and mitigating other risks associated with poor building performance.”
- Budget estimates and feasibility studies. The project budget and a budget for construction should be developed to include line items such as the construction estimate, equipment and furnishings estimate, architects’ and engineers’ fees, consultants’ fees, legal fees, real estate brokers’ fees, site survey and soil investigation costs, filing fees, cost of money during construction, contingency amounts, escalation factors, and cost of technology and telecommunications systems.
- Project delivery methods. As health care facilities have evolved over time, so have the methods used to design and build them. An integrated project delivery approach benefits health care clients by integrating people, systems, business structures and practices; a second method involves retaining a construction manager (CM) early in the design process to act as a cost consultant, helping to determine appropriate methods for framing the structure and HVAC in the building; and a third project delivery method sometimes used for health care projects is design-build delivery.
- Contracting professional services. The scope of architectural and engineering services depends on the nature of the project, the planning and programming capabilities of the owner, and the extent of construction administration services desired by the owner. Small projects may require the services of only a few professionals, while more complex construction requires more players. The complexities of modern facilities, changing construction techniques and materials, changes in environmental controls and the increased importance of complying with the project budget have introduced many more consultants.
Design
Traditionally, building construction has been considered a linear process: planning proceeds design, which proceeds occupation, which proceeds use. In today’s health care environment, organizations have access to several other options.
Project management handbook author, contributors and partners
Lead author
- Dana E. Swenson, PE, MBA, SASHE, is the managing member of ExecHFM LLC, a consulting firm specializing in health care facilities management.
Contributors
- Fred Betz, Ph.D., LEED AP BD+C
- Ken Cates, SASHE, CHC
- Thai Dinh, AIA, ACHA, ACHE, NCARB
- John Farnen
- Michael Hatton, MBA, CHFM, FASHE
- Mark Howell
- Mark Kenneday, MBA, CHFM, FASHE, CHC, CM-Lean
- Kent Ley, AIA, ACHA
- Karri May, AIA, ACHA, LEED AP
- Angela Mazzi, FAIA, FACHA, EDAC
- Spencer Moore
- Benjamin J. Policicchio, AIA, ACHA, CHFM
- J. Patricio Rios, P.Eng, CEM
- Joe Sprague, FAIA, FACHE, FHFI
- Steve Templet, AIA, ACHA, CHID, LEED AP
Special thanks
In one facility, small jobs may occur on a rolling basis without a need for public bidding. In another, bidding for a large project may begin before all the documents are in order. In still another, design and bidding may happen for one aspect of a project as construction proceeds on a separate aspect of the same project.
Even in this evolving environment, the best practices remain the same. Assemble a team of well-trained and seasoned professionals, communicate closely with all segments of the facility’s user base, and gather the necessary data with intention and deliberation.
The planning, design and construction (PDC) team. As an organization moves from planning to the design phase, it will select a PDC team to take the lead moving forward. This team is made up of at least three entities: the owner or owner’s representative, the design lead and the contractor. Each will represent other participants retained to assist them with their duties and responsibilities.
The owner will authorize the selection and hiring of some or all of this team, often with input from the organization’s board of trustees, the building committee of the board or facility administration. For some government-owned facilities, a contracting agency may select team members.
Some large facilities and health care systems will have a director of PDC or a similar role. In these cases, facilities managers are typically tasked with building operations while the director of PDC handles construction projects. Both should be consulted in the design process.
User input. The design team should listen to the perceived needs of medical and nursing staffs, department heads, other facility employees, patients and visitors. The community should also be considered among a facility’s users, which is one reason why a community analysis is an essential portion of health facility master planning.
Hands-on exercises and diagramming can be easy ways to engage users in the design process. For example, participants in a brainstorming session can use simple blocks and strips of paper to play with different configurations for major clinical and support functions. Many users find this approach more engaging and fruitful than trying to decipher a narrative or set of schematics.
Design phases. The designer needs to know how the building and equipment will be used, where it will be located, what the site conditions are, how large the building will be, how much it should cost and when it should be completed, along with any specific desires of the owner.
To make this information available, every building project must begin with programming. This process includes the development of a functional program, architectural space program, pre-design and schematic design. From this information, a preliminary schedule and budget are generated.
After the owner approves the functional and architectural programs and gives the design organization notice to proceed, the formal design stage begins with preliminary drawings. It continues through the preparation of contract documents and does not end until a certificate of substantial completion is issued.
The design lead must carefully analyze and work to control all aspects of the project budget at each phase.
Authorities having jurisdiction (AHJs). The design team must pause and formally submit their work to the owner and AHJs at the conclusion of each phase of the traditional design services, which serve as important project milestones. Documentation at each phase conveys to all parties the intent of the design and its adherence to or deviation from the written program, the budget and the time schedule.
Periodic discussions and conferences with AHJs increase understanding and appreciation of the design on the part of the reviewer, expediting official plan reviews. This contact also gives the AHJs the opportunity to make suggestions or issue directives regarding compliance early in the design process.
Jurisdictions frequently overlap, which can result in duplication of inspections, plan reviews and approvals. Sometimes agencies have conflicting requirements. Considering these complexities, it is wise to work closely with AHJs throughout the design and construction process.
- Mock-ups. At first glance, creating life-sized models of functional spaces or room elements may seem like a lot of work and expense. However, mock-ups often provide several benefits, from identifying possible redundancies to testing options for workflows and processes.
- Sustainability and design. Because energy codes and related standards are becoming more stringent and owners are increasingly likely to add sustainability requirements, sustainable design professionals have much to offer a PDC team. Larger and more complex projects may need multiple sustainable design professionals with architectural, engineering and construction backgrounds.
Fire and life safety planning. Questions of fire and life safety should be part of the conversation from the earliest part of the design phase. They should be considered in every activity, including the selection of the design team members. All risks should be mitigated as far as possible through proper arrangement of the spaces, equipment, traffic flows and systems.
All new construction must comply with the latest applicable codes and best practices for fire prevention and life safety. Additionally, fire and life safety planning must be executed for the benefit of the people who will be on the property for the duration of the project.
Interim life safety measures. The safety assessments and recommendations identified during the planning phase (e.g., PCRA, ICRA and ICRMRs) must be reviewed and, if necessary, modified by the design team during the pre-design phase. These should be continually reviewed and monitored throughout design and construction.
The team should identify the risks particular to the project in question, as different facilities and types of construction projects may present different hazards. Threats must be considered to human life and to the organization’s property and equipment. Appropriate protocols will need to be developed for the different groups of people likely to be present during the construction process, including medical care providers, visitors, vendors and construction workers.
ASHE offers an Infection Prevention & Life Safety Checklist for identifying threats on a walk-through of a facility. Accessing this tool during the design phase can help the team anticipate concerns long before they materialize in the facility.
Bidding
Bidding examines the complex phase of negotiating contracts for various aspects of construction. Budgeting, financial terms and payment structures will be outlined, as will the scope of work, responsibilities and expectations that are covered in construction agreements.
Traditional methodologies for construction projects follow a simple, linear process: design, bid, build (DBB). In this process, each phase is distinct, and each concludes before the next phase begins. While some contemporary projects continue to follow this methodology, it is now only one of several methodologies an organization might follow to achieve their desired result. In some cases, an alternative to the traditional DBB method may produce quicker, more efficient and less costly delivery.
No matter the chosen delivery method, at least one bidding process will likely take place to find and hire construction professionals to execute a remodel, addition or new construction.
Construction bidding negotiation. Three concerns that drive bidding deliberations include finding providers who are well-qualified and experienced, determining a reasonable cost for the work and structuring the contracted project delivery to minimize cost overruns.
Budget estimates that have been refined through both the planning and design phases provide a reasonable range for bid submissions. Bids that are significantly higher or lower may indicate some questions and discrepancies in contract documents such as drawings and specifications.
Construction agreements. Once a bid has been accepted, it is important to allow for up to several weeks of “soft time” in which contract negotiations are conducted, permits are prepared and the facility’s internal paperwork process is executed.
Because the consequences of accepting a contract exclusion often do not manifest themselves until after construction is underway, the owner should discuss these requests with the PDC team and other affected parties before an agreement has been executed so the full impact of the requested exclusions can be discussed.
- Value engineering. The best time to influence the expenses related to a construction project is during the planning phase because changes become increasingly complicated as the design and construction phases proceed. Nevertheless, value engineering does occasionally become necessary, as setbacks and unforeseen challenges happen. For any project, a design lead or CM may be requested to find cost savings throughout the duration of the work. This should be done only after careful analysis of the potential consequences.
Construction
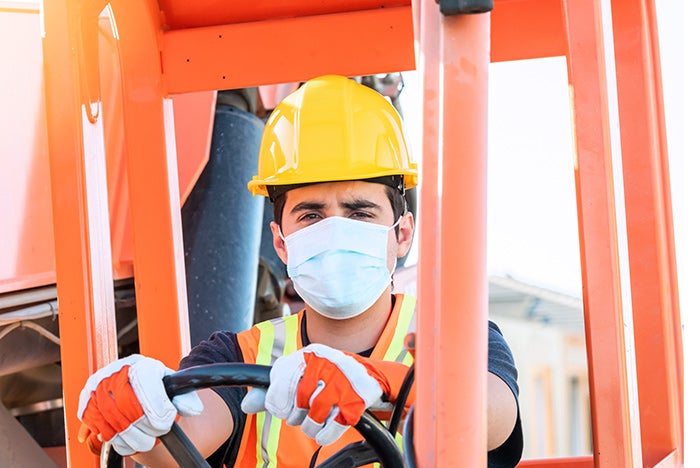
Image from Getty Images
The construction phase officially begins when a notice to proceed is issued to the contractor or when the owner-contractor agreement is executed. The contractor, with the support of the design team, will begin the work of adding or modifying the necessary structures, while attempting to minimize disruptions to the facility’s daily operations.
The focus here shifts from preparation to execution. Topics will include scheduling; working with contractors and other professionals; human life and safety considerations; working with building officials, regulators and stakeholders; monitoring the project as work proceeds; everything leading up to the closeout; and, finally, assuming occupancy of the space.
Pre-construction activities. A notice to proceed or owner-contractor agreement must be approved by the health care organization and by any bonding, grant or loan agencies. Before a notice to proceed is issued for construction, all approvals must be received from relevant AHJs, the owner or contractor must have obtained all necessary permits, and all insurance certificates must be in order, too.
The owner’s representative should review approvals, permits, insurance policies and financial arrangements, including cash flow. The design lead may assist with this review. The project budget must be refined to include final estimates for items such as cost of construction, professional fees, prepaid items such as the site survey and soil investigation, construction loan and equipment costs. The budget should also include the cost of insurance and appropriate project contingency funds.
Between the notice to proceed and the start of construction, a period called “buyout” occurs; it addresses any issues not settled before the owner-contractor agreement is signed. During buyout, all subcontractor contracts and systems purchases are finalized. Purchase orders may be issued for materials that require a long lead time for delivery to the construction site.
Typically, the contractor submits a copy of the construction schedule to the owner and the design lead. On this, long-lead items and critical path activities should be clearly identified. The order in which subcontractors must be approved, as well as schedules for purchasing and fabricating materials, products and systems, will be determined as the contractor prepares the work plan.
In some project delivery methods, such as fast-track construction, the buyout process may occur during design or bidding; early buyout may also occur in cases where it is desirable to lock in known material costs when increases are anticipated.
The PDC team during construction. During construction, there will be scope and design modifications in the form of revisions and requests for clarification or instruction sheets. Approvals for samples, substitutions and shop drawings all require design decisions. The approval of one sample or piece of equipment may trigger a series of design changes.
Thus, once construction is underway, the contractor and the design lead may have very distinct roles, but both will be actively engaged. Other project participants and stakeholders, including representatives of AHJs, may also remain active during the construction phase.
Administrative activities. All construction projects entail certain administrative activities, including requests for information (RFIs) and managing changes in the work.
Project specifications require specific parties to provide certain information, such as the site survey from the owner, contract documents from the design lead or the submittal schedule from the contractor. Initially, the RFI process was used only by the contractor to obtain information from the design lead, but it has evolved into a universal exchange of questions and answers.
Change orders can present scope additions, deletions or modifications. They may also be issued to correct discrepancies in the contract documents, to accommodate program changes or to adjust for unforeseen site conditions. Some level of change should be anticipated, and cost contingencies for these inevitable changes should always be included in the project budget.
Payment processes. Before the first application for payment is submitted, the contractor typically provides the design lead with a schedule of values to determine dollar amounts for each portion of the project. Once approved by the owner and the design lead, this schedule is used for reviewing the contractor’s applications for payment.
Scheduled payments to the contractor should reflect a reasonable value for work in place and materials stored on-site. If specifically provided for in the owner-contractor agreement, the application for payment may cover materials stored off-site as well, provided they have been paid for by the contractor and typically are stored in a secure, bonded warehouse.
The design lead must guard against overpayment to the contractor, as this may adversely affect the performance and payment bonds. The bonding company is obligated only to perform and pay for work the contractor is obligated to perform and pay for. If there has been an overpayment to the contractor, insufficient funds may remain to allow the bonding company to complete the project.
The design lead may approve an amount less than that requested by the contractor or may withhold the request entirely. The latter action should be taken only when the design lead is acting to protect the owner from a potential loss due to third-party claims, the contractor has failed to pay subcontractors or suppliers fairly and promptly, or defective work has not been corrected.
The design lead is prohibited by law from certifying payment for work designed by other licensed professionals, such as payment for the work of a separate interior architect or engineers contracted directly to the owner.
Project closeout. The closeout phase of a project begins when the construction work nears substantial completion.
For the contractor, closeout includes all activities necessary to prepare punch lists, resolve construction items remaining for completion or correction, train facilities management staff in how to operate the building and assemble the required closeout documents.
For the design lead, closeout includes the activities necessary to determine substantial and final completion, determine whether the contractor has provided the required closeout documents for submission to the owner, issue the final change order to resolve outstanding contract issues and issue the final certificate for payment.
For the owner, closeout includes possessing and occupying the building; assuming responsibility for security, maintenance, heat, utilities and insurance; and making final payment to the contractor.
Operations
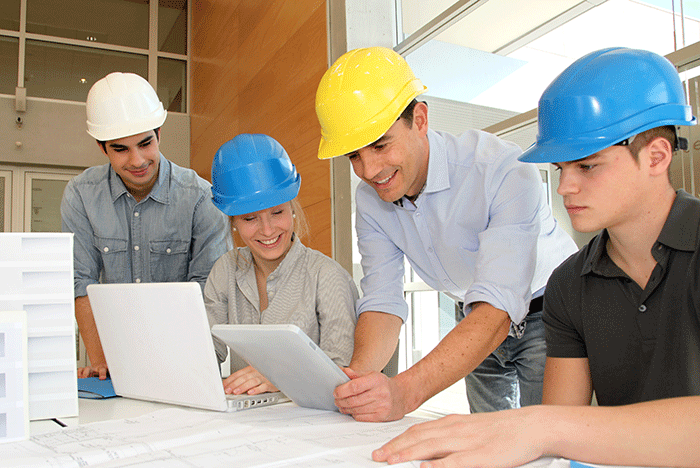
Image from Getty Images
Operational considerations are best addressed throughout all phases of PDC and ongoing use. Input from building operators is perhaps the most obvious means of foregrounding operations during the process.
The owner’s representatives on the PDC team may or may not include the facilities staff who participate in and clearly understand the daily needs of the facility. If the team does not have a permanent representative from within facilities maintenance staff, regular check-ins with this team will provide critical input, such as confirmation that they can maintain systems specified for the project, whether staff will need to be hired or trained, or whether an outside contractor will be needed to maintain critical systems.
Maintenance, upgrade and renovation concerns. Certain projects will not require general contractors but vendors who come in to do the work of installing, renovating or upgrading equipment. Other projects may involve scheduled maintenance or emergency repairs by facilities staff. While it may be that no new ground is being broken or no walls are being moved, facilities management will still be responsible for planning efforts.
Essentially, if a change requires anything more complex than simply rolling an item into a room and plugging it into a wall, planning, communication and coordination must be done. With even the smallest project, if the process is neglected, human life and safety could be jeopardized or a large-scale project could be impacted down the line.
Infrastructure systems include heating, ventilation, air-conditioning and refrigeration; plumbing for water, waste and gases; electrical systems; building automation and control; information technology and communication; pneumatic tube systems; fire alarms and suppression; and other clinical technology. A failure in any of these systems can cause patient harm or loss of life, as well as threaten the safety of facility personnel.
Closeout documents, operations and maintenance training. As part of the requirements to be met before approval of the final payment, the design lead determines whether the contractor has provided all contractually required closeout documents to the owner.
These documents should be carefully cataloged and packaged in a manner that makes retrieval of information as rapid and accurate as possible. Should a breakdown in a critical system occur, quickly locating all relevant documents may be crucial.
Most equipment guarantees and warranties are rendered null and void if an item is not properly operated and maintained. For this reason, the contract for construction typically requires the contractor to set up appropriate training of facilities staff by the product manufacturers and installers. A program of staged, preventive maintenance planned with and approved by the manufacturer should commence while the project is still under construction.
At this point, the commissioning process calls for a commissioning agent to represent the health care facility as the building systems are brought online. This agent witnesses the installation, testing and operation of all systems and equipment, and oversees the training of all personnel. The agent is also fully aware of the location of all controls, valves, switches and safety devices; has firsthand knowledge of any critical air-balancing problems; and has participated in the initial move-in of the facility.
It is also advisable to train staff in the use of spaces that have changed from previous configurations or purposes.
Initial move-in and post-occupancy evaluation. When a new health care facility, addition or major renovation has been completed, an evaluation period is required after the building is occupied. Simulations and test runs provide important data, but many issues reveal themselves only during day-to-day operations.
The initial evaluation period in a large health care facility can take six months or more, and this should be taken into consideration when contracting for the design lead’s services. At the end of the evaluation period, the architect should be asked to conduct the first post-occupancy evaluation (POE).
All parties should treat POEs as a positive learning experience. There is always a chance that a POE will reveal errors in building design. In some instances, all parties may have failed to recognize a need that was not obvious at the programming stage.
The wise owner will ask the design lead to follow up with a one-year evaluation prior to the expiration of the contractor’s one-year warranty. Some owners may elect to have the design lead conduct a five-year evaluation, as well.
Experienced participants in the PDC process for health care facilities understand that design is an ongoing process in a facility type that must continuously evolve to keep up with medical advances and ever-changing building technology.
This article was excerpted and edited by Health Facilities Management staff from the American Society for Health Care Engineering’s The Facilities Manager’s Handbook for Health Care Project Management.