Developing a lockout/tagout program
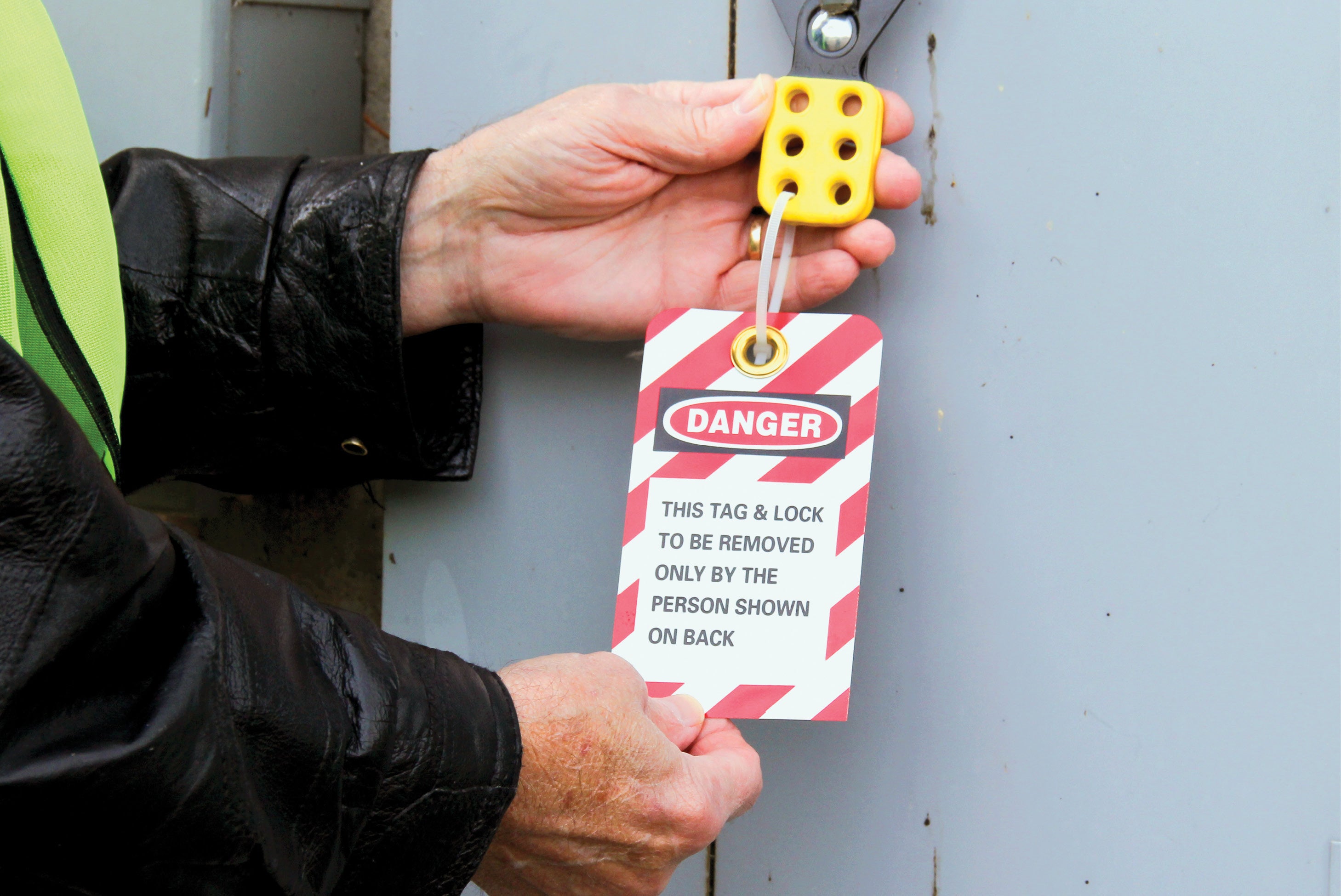
A LOTO program is used to ensure that all general industry workers are isolated from potentially hazardous energy.
Image by Getty Images
Many health care organizations misunderstand or are unaware of the control of hazardous energy (lockout/tagout [LOTO]) as required per the Code of Federal Regulations (CFR) 1910.147, which is enforced by the Occupational Safety and Health Administration (OSHA). Often, they do not have a compliant or effective program, while others do not have a program at all. Yet LOTO was sixth in the 10 most frequently penalized OSHA standards in hospitals during the period of October 2021 through September 2022, according to OSHA’s website.
A LOTO program is used to ensure that all general industry workers (including employees, vendors and contractors) are isolated from potentially hazardous energy, and equipment is locked out and/or tagged out before employees perform any servicing or maintenance activities on equipment where the “unexpected energization, startup or release of stored energy” could occur, according to OSHA’s LOTO eTool tutorial at osha.gov/etools/lockout-tagout.
Not only does a noncompliant or missing LOTO program pose a danger to everyone who might be involved in equipment with hazardous energy, there are also fines and potential lawsuits associated with noncompliance. In fact, over the period discussed above, hospitals received 12 citations and penalties of $50,153, according to OSHA. This means that the average penalty was more than $4,000.
To avoid incurring these fines and, more importantly, to help ensure the safety of employees, vendors and contractors working on-site, health care facilities must become aware of common OSHA LOTO violations, including failure to identify and isolate all energy sources, failure to shut down equipment, failure to de-energize equipment, failure to drain residual energy, failure to provide LOTO training, failure to create equipment-specific LOTO procedures, failure to conduct periodic LOTO inspections, failure to establish a LOTO program, and failure to develop and enforce a LOTO policy.
Developing a program
This article reviews the standard’s requirements for the development, implementation and practice of an effective LOTO program. More detail can be found in OSHA’s “Tutorial on Control of Hazardous Energy (Lockout/Tagout)” webpage at osha.gov/control-hazardous-energy.
CFR 1910.147 also lists which activities are not a part of this standard, including the preventive maintenance and service of equipment, which occurs during routine operations by employees to whom exposure to the unexpected energization, startup or release of stored energy would not normally occur. This assumes that the safeguards required by the standard are in place and effectively prevent any applicable employee from such exposure.
Resources
OSHA also makes exceptions for workers to use alternative means of protection safeguards during routine processes such as “minor tool changes and adjustments, and other minor servicing activities … which are routine, repetitive and integral to the use of that production equipment,” as well as for service or maintenance on equipment connected to electrical energy via a cord and plug, provided that such equipment is disconnected from the source electricity and the “authorized employee” has sole control over the plug, according to the OSHA eTool tutorial.
This standard applies to workers who perform maintenance and service operations on equipment, where they may be negatively impacted by “the unexpected energization, startup or release of hazardous energy from sources such as mechanical, hydraulic, pneumatic, chemical, thermal or other energy,” the eTool tutorial states. Some examples of applicable work performed are “constructing, installing, setting up, adjusting, inspecting, modifying, maintaining and/or servicing machines or equipment, including lubrication, cleaning or unjamming of machines or equipment, and making adjustments or tool changes, where employees could be exposed to the unexpected energization or startup of the equipment or release of hazardous energy.”
Another event triggering the standard is when a safeguard or other safety device must be removed to perform routine maintenance or service or when an employee in the course of their work is required to place themselves into the machine or in the proximity of the machine’s operation.
The standard requires health care organizations to adopt and implement policies and practices for preventive maintenance and repairs to be made when the equipment is powered off, isolated from its power source, and to prevent the release of any type of hazardous energy while those operations are performed. Such policies and practices must include training, retraining and inspections to ensure the effectiveness of the program.
OSHA has some definitions in the standard to clearly indicate what specific terms mean. Each is an integral part of any competent energy control (i.e., LOTO) program.
The program must have policies defining practices specifically outlining the particular knowledge the authorized employee must use to perform LOTO, including the extent of application and the specific processes that must be followed when using LOTO.
The standard also requires both the policy and practice of routine observations of LOTO be performed before preventive maintenance or service is started to determine if the potential exists for the unplanned energizing or startup of equipment or the release of stored energy.
According to OSHA, LOTO policies must contain the scope, purpose, authorization, rules and techniques used to both control any hazardous energy and which process is used to ensure the policies and procedures are followed.
Policies must include how the practice is to be applied in any situation for every type of equipment and include the steps to follow to control hazardous energy through the shutdown, isolation, blocking and locking down of the equipment. They must also include the means to install LOTO devices and define responsibility for them by authorized employees.
The standard requires both initial and ongoing training of the policies and practices to ensure comprehension and competency in the use of LOTO.
The training is specific about not attempting to reengage equipment that has been locked and/or tagged out and speaks to the limitation of tags alone, including the lack of suppression of operation compared to a lock. Tags must be readable and easily comprehended; made of sturdy materials to withstand the environment in which they are used; securely affixed and not to be removed, ignored or defeated; and their role in the overall LOTO program must be explained so they do not provide a false sense of security.
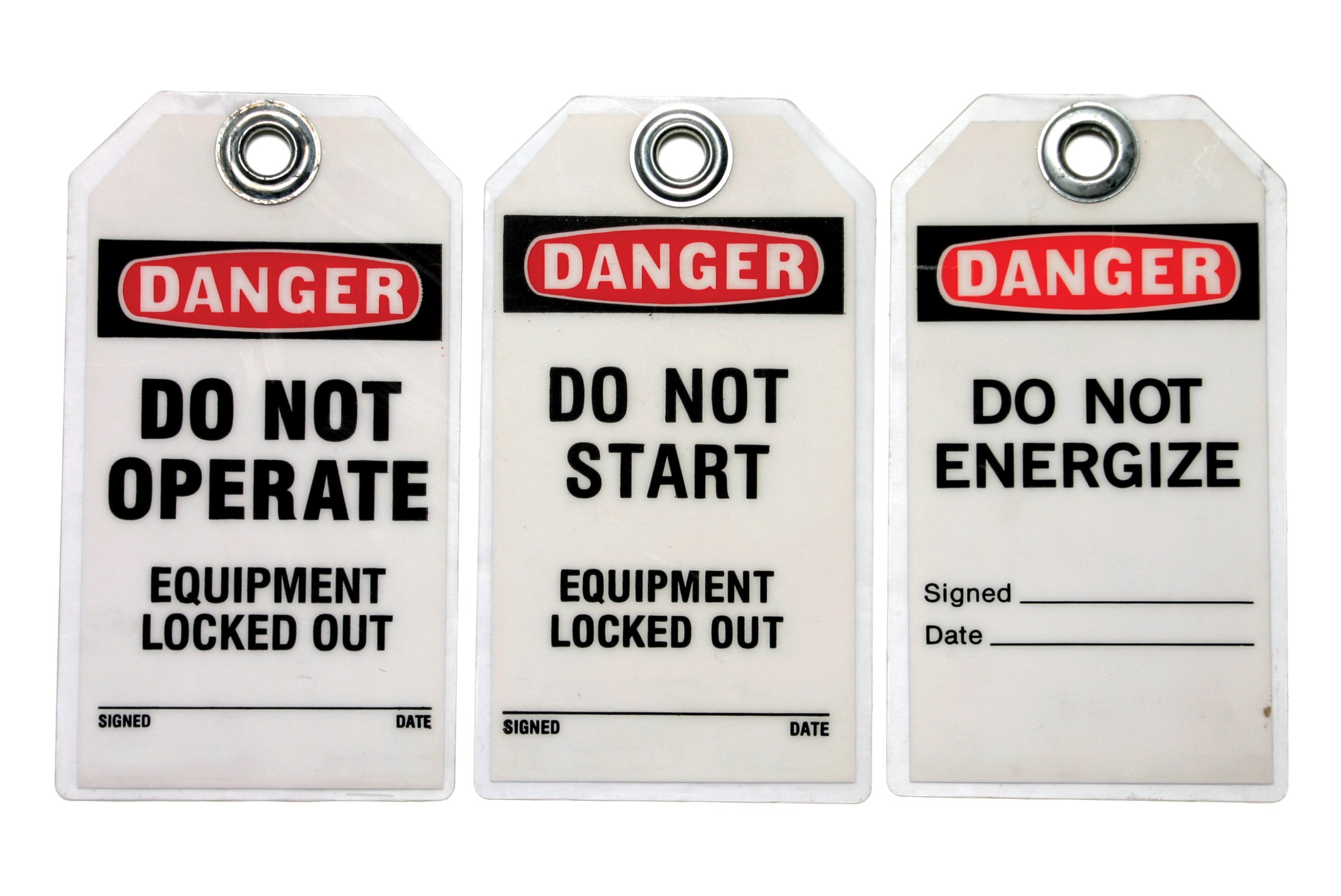
Tags must be readable, easily comprehended and made of sturdy materials to withstand the environment in which they are used, among other requirements.
Image by Getty Images
Retraining must happen when a new duty is assigned, new equipment or practices are used, or when observations reveal the need. The purpose is to educate on the new equipment or practices and ensure employee comprehension and competency.
Finally, all training must be documented and current, and include the employees who were educated and the dates. All training is required annually and throughout the year during LOTO events to ensure continued safety.
Even the observations have requirements, including the confirmation of the effectiveness of training and competency testing. Any issues discovered must be documented as to the corrective action taken and steps to ensure the situation does not recur. Routine observations during LOTO events must include the specific equipment, the employees educated, the date and the observer’s name.
If only lockout is used, the practices required for that piece of equipment must be reviewed with the authorized employee, but if only a tagout is used, both the authorized employee and any affected employees must review the required practices prior to the use of the tag.
As of Jan. 2, 1990, all new equipment as well as those with major upgrades or repairs are required to have the means to lockout the energy isolation device. All those must use a lockout device unless the employer is able to show the tagout and practices employed are just as effective and safe. Other equipment that does not have the means to employ a lockout must use a tagout.
The employer is also responsible for providing all LOTO equipment that is required for all equipment at that location that could be energized, started or release hazardous energy. Both lockout and tagout devices have multiple requirements, including being of sturdy construction, able to weather the environment in which they are placed, being individually identifiable, standardized and having warnings, as well as several other requirements.
The standard has specific elements that must be addressed in the policies and in practice, including preparing for the shutdown by ensuring an understanding of the hazards it may create, the steps used for the shutdown, applicable/available energy isolation devices, LOTO methodology, relief of stored energy and verification of both isolation and de-energization.
The standard also has requirements that must be addressed in the policies and in practice for the removal and restoration of the function of the equipment. This includes a survey of the equipment area for tools, parts or debris that should be removed prior to startup, and ensuring that all machine or equipment components are intact and ready for operation. A survey of the work area is to be performed to ensure all employees are out of harm’s way and all employees affected by the startup have been notified that it is occurring.
The devices or tags used must only be removed by the person who placed them on the isolation device. On the rare occasion when one of the employees is not available to remove their LOTO, the organization may authorize someone else if protocols have been developed and trained prior to the event. There must be specific documentation that the employee is not on-site, that efforts were made to reach them and that the employee is made aware of the removal of their LOTO device prior to their return to work.
The standard also covers temporary restoration for testing and group LOTO procedures as well as ensuring there is continuous protection for employees through each shift or when new employees are introduced to the work area. This includes how the LOTO protection is continuous during shift changes.
A lifesaver!
These are the basic elements required by the CFR 1910.147 standard to develop an effective “control of hazardous energy” program. The control of hazardous energy is also addressed in several other OSHA standards, including Safety and Health Regulations for Construction (part 1926) electrical (subpart K) and concrete and masonry construction (subpart Q); and General Industry (part 1910) electrical (subpart S).
Careful attention should be paid to ensure the standard is fully implemented. There have been unfortunate outcomes of incidents in health care facilities where the LOTO program was either not in place or followed, and the results were injuries or death. These include being crushed to death by an elevator while changing the smoke detector at the top of the elevator shaft, severe burns from steam due to not performing LOTO, and arc flash burns, blindness and loss of hearing as a result of failure to de-energize equipment prior to service.
A LOTO program is not just a compliance thing. It’s a lifesaver!
Using forms and procedures to boost LOTO compliance
Lockout/tagout (LOTO) programs are all about controlling energy sources such as electrical, mechanical, chemical, thermal or other types of energy found in utilities, systems, machines, equipment and other entities. During the servicing or maintaining of equipment and machines, the unexpected startup or release of stored energy can result in serious injury or death to workers such as:
- A steam valve automatically turns on and burns workers who are repairing a downstream section of the piping.
- A jammed blanket folder chain drive unexpectedly releases, crushing the fingers of a worker who is trying to free the chain drive.
- Internal wiring within an electrical panel short-circuits, shocking a worker who is repairing the panel.
Proper LOTO practices and procedures safeguard workers from hazardous energy releases. Having a properly developed program that uses forms and procedure documentation significantly helps to ensure that the proper precautions are enacted and proper steps are taken throughout the maintenance and servicing activities, thus keeping those involved safe from hazardous energy sources.
A great example of how forms and procedures can help assist a LOTO program is that of a lock inventory form used in conjunction with an energy control procedure form. A sample of the lock inventory and energy control procedure forms can be accessed by American Society for Health Care Engineering members through the resource box in this sidebar.
The use of a lock inventory form allows individuals to document which locks are assigned to them and how these locks are being used within the LOTO program, thus providing oversight of lock usage and control.
The energy control procedure form provides detailed information not only on lock usage but also important information on the specific equipment or machinery involved and the energy source being controlled. The important step of listing all energy sources present is a vital step to avoid unintended activation of the equipment or machinery. Including the steps to remove equipment from service also ensures that all steps are taken to not only ensure control of energy sources but also to avoid potential damage to resources if the equipment or machinery are not properly shut down.
Including the LOTO information within the energy control procedure form also ensures that proper steps are taken to remove the locks prior to re-energizing the equipment or machinery.
While detailed LOTO program documentation will take additional time and effort, it is vitally important and well-spent time to ensure the safety of workers from the unexpected startup or release of stored energy that could result in serious injury or death.
About this article
This is one of a series of articles contributed by members of the American Society for Health Care Engineering’s Member Tools Task Force.
Jeffrey E. Henne, CHC, FASHE, CHSP, CHEP, CHFSM, CHPCP, is safety and emergency manager at Penn Medicine — Hospital of the University of Pennsylvania, and Shay Rankhorn, SASHE, CHFM, CHC, FTHEA, is vice president of facilities management at Quorum Health. They can be reached at jeffrey.henne@pennmedicine.upenn.edu and srankhorn@qhcus.com.