Moving from PDC to accreditation
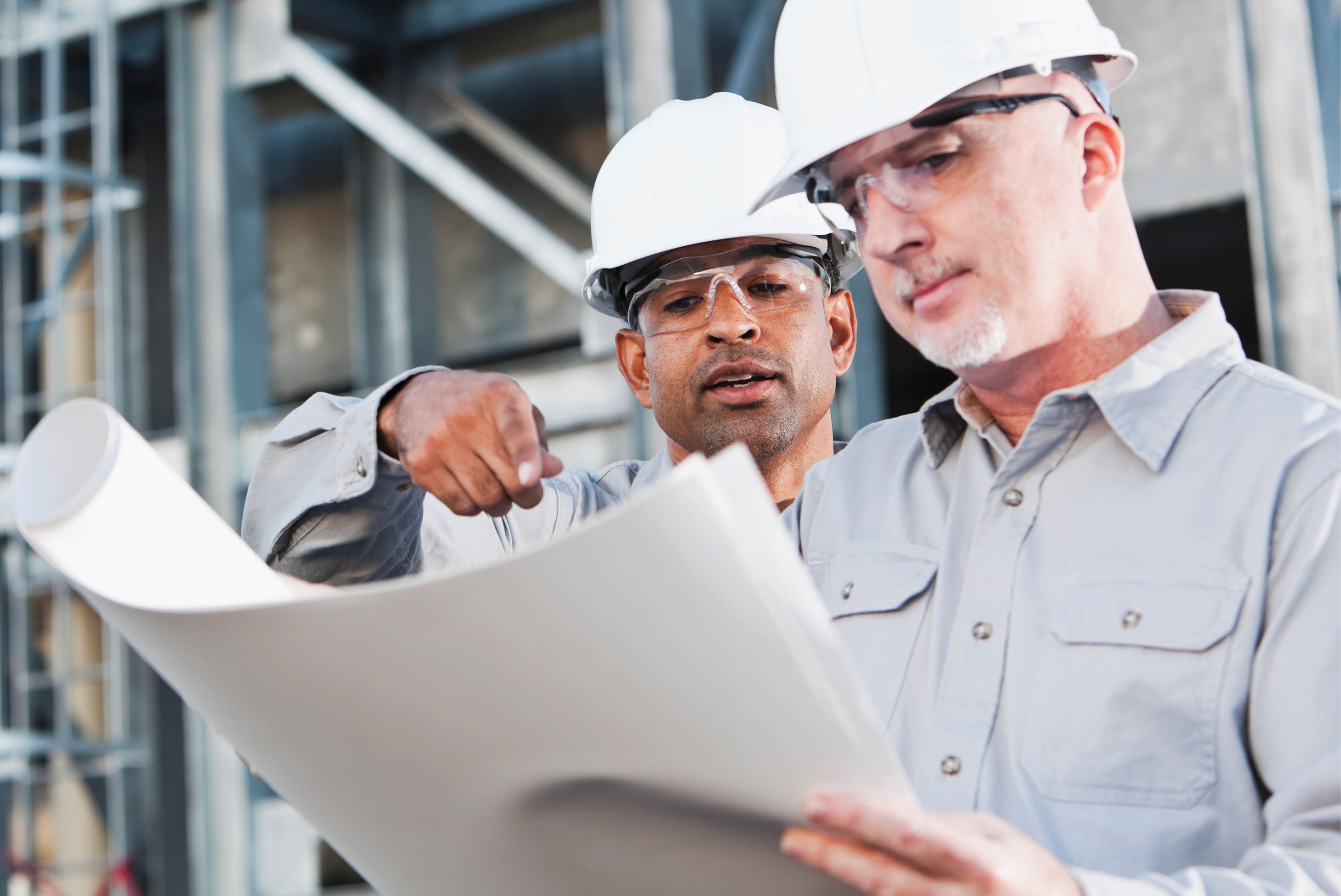
The project team monitors and manages during the construction phase.
Image by Getty Images
Too often, health care facilities are not ready for accreditation the day after construction, nor are they prepared for certification. Traditional construction processes must be reviewed and evaluated to identify and resolve potential gaps by applying industry best practices.
Construction planning is most successful when it occurs across two individual efforts: master planning and project planning.
Master plans are developed using population growth modeling, utilizing data from electronic health records to forecast current and future needs as well as physical plant needs to provide a framework to determine and define upcoming project requests.
Once an individual project has been approved, a project plan is created. It should contain a schedule detailing all project-related activities as well as the budget, the contribution team and its member roles, and a description of how progress and results will be measured.
The major steps in the planning, design and construction (PDC) process and its transition to a fully operational and accredited health care facility are discussed below.
Design and construction
The design and construction segments of the health care facility project plan occur over several phases, including the following:
Design. This typically occurs in three phases: schematic design (SD), design development (DD) and construction documentation (CD).
The purpose of SD is to translate the project plan into drawings of space. The project team determines the areas, physical requirements and relationships of required building spaces and components, confirming or revising the total building square footage and comprehensive project budget.
In the DD phase, the schematic plans and elevations are revised and expanded to incorporate details and specifications required for construction. Designers ensure compliance with all applicable local, state and federal codes and statutes.
The design drawings and specifications define the facility’s size, function, configuration, spaces, equipment and construction materials. With this information, the project budget, schedule and related building plans are finalized and, upon final review and approval, DDs become CDs.
Construction. This is the process in which contractors build structures and grounds in four phases: startup, construction, occupancy and closeout.
In startup, contractors create a baseline schedule for the construction phase. The construction phase begins and ends the building of the project.
The project team — including the owner, architects, engineers, interior designers and construction project managers — monitors and manages the project during the construction phase.
Occupancy of a building occurs when the project is complete enough for the fire marshal and other applicable authorities having jurisdiction to issue a certificate of occupancy (CO).
Upon substantial completion, various documents are produced or obtained that complete the construction documents. These include as-builts, record drawings, markups, closeouts, maintenance, operation manuals, permits, warranties and other documents necessary to occupy and maintain the facility.
Commissioning of systems
A best practice used by many health care facilities is to perform the commissioning of systems. Commissioning is the process of planning, documenting, scheduling, testing, adjusting, verifying and training to provide a facility that operates as a fully functional system per the owner’s project requirements (OPRs).
Commissioning typically includes verification of test and balance results of mechanical systems and lighting levels as designed. Additional consideration should be given to the National Fire Protection Association’s NFPA 3, Standard for Commissioning of Fire Protection and Life Safety Systems. NFPA 3 outlines the commissioning process and integrated testing of fire protection and life safety systems to ensure systems perform in conformity with the design intent.
Verification ensures that building systems and the building itself meet the requirements of applicable codes and standards for health care facilities. Accreditation is rarely achieved solely by meeting codes and regulations. Compliance commissioning demonstrates system design, documents and programming of building systems. Additional requirements may be considered, such as applying NFPA 4, Standard for Integrated Fire Protection and Life Safety System Testing. It outlines test scenarios to confirm the operation, interaction and coordination of multiple individual systems to perform their intended functions.
For commissioning to be most successful, the scope of services must be clearly defined and the commissioning team engaged before design to develop design criteria around the client’s OPR. These OPRs are produced by various operational, facilities management, compliance and leadership teams to create the framework for measuring commissioning.
Facilities operations
Owners often wait until substantial completion to consider how the building will be operated and maintained. This routinely results in high operational costs and impedes or prohibits their ability to comply with applicable standards of operation. A best practice would be for operations to be engaged in all project phases.
A best practice at the operational level may be to develop or amend the strategic asset management plan during construction. Strategic asset management is an approach for maintenance and operations in which a time-based plan is made and executed to maximize stewardship of defined assets.
Strategic asset management should begin in parallel with the PDC process. Essential information and data are available during construction and at various handoff stages. A method to collect this data will add to the success of the strategic asset management plan.
Establishing a building and location hierarchy and an asset hierarchy is a fundamental step in strategic asset management (see draft guidance at ashe.org/HFDS_sheet). Furthermore, an asset identification process performed in conjunction with the installation, acceptance, commissioning, testing or training of these assets should be established and followed during the PDC process.
Responsibilities should be set in advance and clearly defined in project specifications and scope of work. This data should be collected and delivered so that the health care facility can ingest it into its computerized maintenance management system (CMMS) to accurately track inventories and establish and verify preventive maintenance schedules, all required by accreditation.
Hospital accreditation
Accreditation is a survey validating that a hospital meets predetermined quality standards in order to receive payment from the Centers for Medicare & Medicaid Services (CMS) for care provided.
Surveyors evaluate each step of patient care to ensure that doctors, nurses and other staff comply with regulations to treat patients safely and effectively. Surveyors also evaluate the physical environment, looking for proper system function and documentation of each maintenance, inspection and repair activity.
Noncompliance with standards may result in denial of accreditation, leading to business disruption, productivity losses, fines, penalties and settlement costs.
The necessary components of a successful construction project and operational responsibilities are clearly defined earlier in this article, but what are common accreditation gaps and how do they impact the facility?
To bridge the gap between PDC and accreditation, consideration must be given to a more collaborative approach to the process from beginning to end. For example, many can mistakenly assume that once a new hospital has received its CO, it is ready for accreditation. While a CO is a legal document certifying a structure to be safe to inhabit and that the property is built to required building codes, there is a distinction between meeting design and building codes and being accreditation ready.
It is possible, and even probable, that a new facility receives its CO one day, only to begin remodeling, alterations, or repairs to meet accreditation requirements the next. This impacts the facility’s ability to achieve accreditation, negatively impacting revenue and capital expenditure availability.
One key reason for that gap is a misalignment of outcomes and responsibilities. The PDC team is charged with protecting the budget and the schedule. The operations team has long-term commitments to maintain and steward the newly completed project, its assets, accreditation and compliance.
To succeed, these responsibilities should be merged into a comprehensive OPR and incorporated and utilized throughout the process, from planning through operations. Without creating and following a comprehensive OPR for the PDC process, owners are left with specifications and drawings that may ignore critical issues related to accreditation.
The implications of treating the PDC process and accreditation requirements as independent of each other leads to significant waste such as defects and rework. This waste is caused by construction outcomes not being aligned with operational excellence outcomes required by accreditation. Additionally, it can lead to waiting for renovation of the newly constructed building to meet accreditation requirements.
Long after construction is complete and warranties are satisfied, the ramifications are felt operationally, whether appearing in incorrect or misidentified barrier management systems, equipment selection outside of system or facility norms, value-engineered substitutions, or construction methods and practices not in alignment with system expectations. The totality of these gaps tax the capital and operational finances, which should be allocated elsewhere.
Research conducted by Emerson Reliability Consulting titled “Operational Readiness: Bridging the Gap Between Construction and Operations for New Capital Assets” suggests significant and costly gaps. This research indicates that up to 30% of the data created during the design and construction phases is lost by project closeout.
Additionally, according to the General Services Administration, the cost associated with understanding project closeout packages is 10 cents per square foot. According to a National Institute of Standards and Technology study, the cost associated with lack of access to accurate information required to service equipment is 23 cents per square foot.
Successfully performing a project from planning to operations that results in accreditation requires all involved parties to be committed to a unified outcome. Facility leadership, the PDC team, facilities management, quality, infection prevention and other related departments can work together and achieve long-term success.
A healthy PDC-to-accreditation process will include commissioning, life safety commissioning (per NFPA 3), integrated system testing (per NFPA 4), a comprehensive asset management program and accreditation assurance.
Accreditation assurance
An accreditation assurance program begins in the planning and design phases. While life safety design and installation are among the engineering disciplines, it is recommended that the accreditation assurance program be administered by an individual or team versed in code requirements and accreditation survey requirements.
A comprehensive accreditation assurance program begins with specifying the accreditation requirements in the OPR. The requirements should be used for all phases of the project, from initial SD to substantial completion. A continuous review of construction drawings for accreditation compliance should occur throughout the project, as change orders and requests for information can modify the project deliverable mid-construction, significantly impacting accreditation readiness.
Routine and scheduled project progress surveys should occur to ensure the facility meets building codes and achieves accreditation. Once the design standards are approved, monitoring of construction means, methods and practices to meet accreditation requirements should be performed at various critical intervals, including rough-in and top-out.
These inspections should include findings and recommended remediation of potential accreditation hindrances. Inspections should occur to address the proper installation and functioning of life safety-related equipment and building features such as fire-rated doors, fire and smoke dampers, and smoke evacuation systems. This should be done through code-required acceptance testing, verification and reporting.
Frequently, fire doors are improperly installed from the beginning, which becomes an operational and capital expenditure incurred by facilities. Additionally, these life safety features that are required by CMS and accrediting organizations must be repaired in a compressed timeframe, often adding substantial cost. This is also true for dampers, electrical panels, remote power supplies and other elements that are often hard to access and costly to replace or repair.
As construction nears substantial completion, the accreditation assurance team must perform a final gap analysis survey. This survey resembles a mock survey (usually completed in preparation for an accreditation survey). Again, these reports should include findings and recommended remediation of potential accreditation hindrances and be promptly delivered to the hospital and PDC team.
As life safety systems are being installed, it is the perfect time to develop baseline inventories complete with naming conventions. These inventories should be captured in the CMMS. Once collected and entered into the CMMS, facilities professionals should establish a system for compliance document compilation, whether electronic or paper. The accreditation assurance team can assist in creating the systems and workflows to support this effort.
Life safety drawings are a vital part of PDC, and it is recommended that the accreditation assurance team review and approve the life safety drawings due to their familiarity with accreditation requirements. This will ensure acceptance and utilization during a survey.
Bridging the gap
Bridging the gap between PDC and accreditation is possible. Still, it will require all stakeholders to collaborate from the beginning and remain active and engaged throughout the entire PDC-to-accreditation process.
The key to success is creating a culture in which accreditation is integral from master planning throughout each of the construction processes to operations once construction is complete.
Once this culture is established, developing the needed processes, strategies, systems, and checks and balances as a unified team will allow any organization to succeed in closing and potentially eliminating this gap so the facility is ready on day one.
Inspection, testing and maintenance in an accreditation assurance program
Authorities having jurisdiction are beginning to enforce the adoption of newer code editions of the National Fire Protection Association’s NFPA 101®, Life Safety Code®. These changes will add the requirement of creating and implementing NFPA 3, Standard for Commissioning of Fire Protection and Life Safety Systems, and NFPA 4, Standard for Integrated Fire Protection and Life Safety System Testing.
As such, the need for the development and management of inspection, testing and maintenance (ITM) systems and processes will move to the forefront for facilities managers across the board.
- Life safety commissioning. NFPA 3 was developed in response to a request from the National Institute of Building Sciences. It outlines the commissioning process and integrated testing of fire protection and life safety systems to ensure systems perform in conformity with the design intent.
- Integrated testing. NFPA 4 outlines test scenarios to confirm the operation, interaction and coordination of multiple individual systems to perform their intended function.
As these requirements are enforced, they will become life safety features impacting accreditation. As a condition of accreditation, it becomes necessary to further consider developing a comprehensive accreditation assurance program. Planning and building an accreditation assurance program includes an integrated life safety ITM program. The development of these programs can be a lengthy and complicated process. While ITM programs are essential, health care facilities managers often lack the necessary guidance and subject matter expertise to develop effective programs.
ASHE has created a valuable desktop resource called Developing Code-Compliant Integrated Fire Protection and Life Safety Inspection, Testing and Maintenance Programs. It was developed by some of the top subject matter experts in their respective fields to aid in the development and implementation of successful plans and programs to meet or exceed rigorous accreditation requirements.
About this article
This is one of a series of monthly articles submitted by members of the American Society for Health Care Engineering’s Member Tools Task Force.
Shadie (Shay) R. Rankhorn Jr., SASHE, CHFM, CHC, is vice president of facilities management at Quorum Health, Brentwood, Tenn., and president of ASHE; and Scott Mason is senior manager of strategic asset management – professional services for Brightly Software Inc., Cary, N.C. They can be reached at shay.rankhorn@gmail.com and scott.mason@brightlysoftware.com.