Preparing for adverse weather emergencies
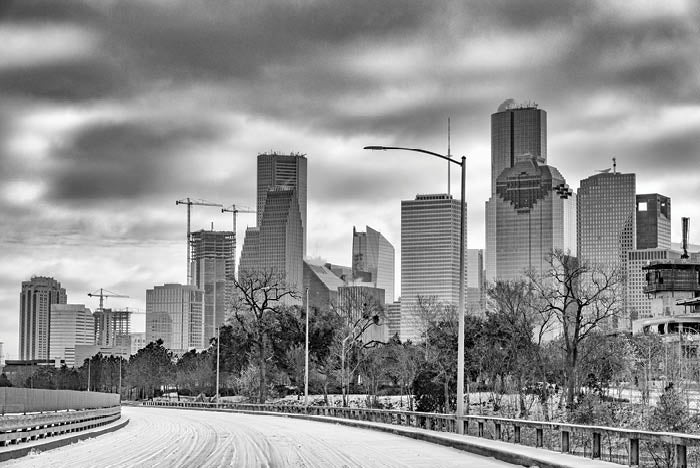
During the winter storm of 2021, Texas facilities experienced outages of natural gas and shortages of diesel fuel deliveries as a direct result of power outages at fuel depots or hazardous road conditions limiting the transportation of fuel delivery trucks.
Image by Getty Images
According to the World Meteorological Organization, a specialized agency of the United Nations made up of 193 member states and territories, the number of weather-, climate- and water-related disasters has increased by a factor of five over the 50-year period of 1970–2019.
Health care facilities must be prepared not just for the known events, like a hurricane or forest fire, but for the unexpected events of severe wind gusts and extreme rain. An unexpected event might also come in the form of a broken water main or unplanned utility outage caused by severe weather.
Facilities managers all plan and prepare for events in their emergency operations plan (EOP), but how many facilities truly experience everything that is included in an EOP? With the diversity of weather events experienced across the United States, the preparation for each geographic area will be unique. Northern states might experience extreme cold as the norm, while Southern states will experience extreme heat and humidity.
Ultimately, weather events will affect all health care facilities in different ways, regardless of geographic location, and the following offers some suggestions to assist them in preparing for such severe emergencies.
Building envelope
The building envelope is the first line of defense against the perils of Mother Nature. In operating a health care facility, there are several factors related to the building envelope besides the building itself.
Facilities managers must assess the entire property and layout of a design including surface parking, parking garages, canopies, ambulance entrance access, Americans with Disabilities Act accessibility, heliport access and Federal Aviation Administration regulations related to the heliport.
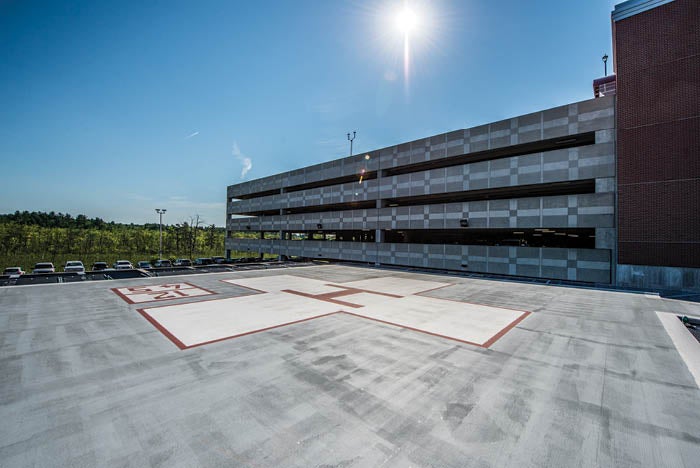
Facilities managers must assess the entire property and layout of a design, including heliport access.
Image courtesy of ASHE
Additionally, they should consider roof membrane and roof drain maintenance, water intrusion points such as exterior sliding doors, unsecured items outside that could potentially turn into projectiles from excessive wind gusts, windows and larger glass walls, and areas prone to flooding conditions from runoff or excessive rain. The list is endless, depending upon the geographic location and surrounding terrain.
The building envelope is the physical separator between the conditioned and unconditioned environment of a building that also provides resistance to air, water, heat, light and noise transfer. Ensuring that the building envelope is functioning properly is an important maintenance activity, yet it is even more important when considering the impact of severe weather events.
Ensuring that roofs don’t leak and that the envelope is keeping extreme cold and heat at bay as designed and constructed is best managed through a maintenance plan. This plan should include regular visual inspections as well as scheduled specialty inspections such as infrared surveys and detailed inspections of system components.
To combat building envelope issues, managers should assess whether the tools and supplies are on hand to mitigate any damage that might be associated with a severe event. Examples include barricade material, sandbags, plastic sheeting material, shop vacuums or water extraction equipment, ice melt and sand for walkways and parking lots, floor fans, portable cooling or heating units and plywood, as well as other materials needed to address impacts from severe weather.
Landscaping often is overlooked as a factor in determining vulnerability to the building envelope during severe weather events. But has the beautiful healing garden in the middle of the courtyard with a water effect been overlooked as a potential water intrusion risk when a tree falls from excessive winds and the retaining wall collapses? What about the patio furniture becoming projectiles during excessive wind downdrafts and gusts?
Evaluating the landscaping throughout the facility campus to determine potential severe weather impacts during all seasons is important to ensure that plans are in place to respond when events happen.
Infrastructure systems
Health care facilities are served by numerous utility infrastructure systems and their related equipment, all of which are critical to providing patient care. This is why the Centers for Medicare & Medicaid Services requires utility management planning. One of the vital elements of utility management planning is to consider the safe operation, maintenance and emergency response procedures for these critical operating systems.
Thought must be given to what might happen if there was a sudden loss of any critical building systems, and what workarounds or temporary solutions are available to get them back online during an emergency. Consideration should be given to, at minimum, the systems described below.
Additional systems may need to be considered based on an organization’s specific situation. How could a severe weather event affect each of these systems, and what measures can be taken to help mitigate the impact and/or improve the response? Additionally, failure of any one component within each of these systems could ultimately result in a failure of the entire process, so consideration of specific components also may be necessary.
Water and steam systems. Water is not only an essential life-sustaining need for patients and staff but also is a vital component of many facility utility systems. Ensuring that water is readily accessible and that potable water is clean and available is vital, and this need can be magnified significantly during an emergency. Having a water management program in place is a required step to ensuring that water supply does not negatively impact patient care. Some of the vital systems that water impacts are:
- Chilled water systems. Thought must be given to what might happen to the chilled water system if the ability to provide makeup water to the cooling towers is impacted by an extended water utility disruption, or what might happen if a tower experiences damage from a severe storm.
Managers should consider the chilled water system as a multipiece system consisting of chillers, chilled water pumps, condenser water pumps, cooling towers, water treatment related to the chilled water system and the overall capacity of the system. If any one of the single components fails, the system could fail.
- Heating water system. Heating water systems are closed loop systems and, as such, the required water makeup will be minimal compared to chilled water systems. Heating water systems also are multipiece systems consisting of pumps, heat exchangers, boilers and control valves.
- Domestic cold water. Loss of domestic cold water has a global effect on a facility. Not only is there potential to lose the power plant, but also direct patient care infection control issues. It is important to establish relationships with the utility supplier for notification of boil water notices, loss of pressure or when utility maintenance is being performed on the system that might affect delivery.
- Sanitary sewer systems. Sanitary sewer events are commonly overlooked as a severe weather event, but what might happen if the utility downstream lift station loses power or is flooded and cannot handle demand? Can the facility manage if sewage starts bubbling up from manholes in the middle of the parking lot?
- Steam systems. Steam is a universal and powerful utility. Steam can be used to heat water, sterilize surgical instruments and provide warm air. The steam system is a critical component to maintaining the sterile processing department that supports surgical services.
- Water softeners. Water softeners treat the incoming utility water supply through the process of ion exchange, replacing the calcium carbonate ion for a sodium chloride ion. The ion exchange process allows for chelation of water on metal. This is a requirement to provide “critical water” in sterile processing for reprocessing of surgical instrumentation.
Gas and oil systems. Natural gas, propane and fuel oil are fuel sources that support emergency generators, food and nutrition services, heating hot water, steam boilers and air handlers.
During the winter storm of 2021, Texas facilities experienced outages of natural gas and shortages of diesel fuel deliveries as a direct result of power outages at fuel depots, or hazardous road conditions limiting the transportation of fuel delivery trucks.
Consideration of these fuels when developing emergency response plans is important.
Medical gas systems. Medical gas systems are unique in the fact that every possible gas can be supported through bottles (except vacuum).
- Medical vacuum. Most medical vacuum systems are air-cooled package units. However, there are some vacuum systems that use chilled water for heat transfer. If a facility has a water-cooled unit, is there an alternative source of cooling media if the primary cooling source is lost due to a storm-related utility disruption?
- Medical air. Hospitals that produce medical air for patient support might want to consider a redundant electrical feed to support the equipment if the primary electrical branch circuit fails, or have an exterior emergency connection point with power capacity if a temporary compressor package is needed from a storm-related event.
- Oxygen. Oxygen systems can be liquid bulk systems, bottled or a combination of both bulk and bottled systems. Facilities managers should work with their supplier to ensure they have a properly sized tank and evaporator to handle demand. Some facilities have installed a connection point, much like an emergency oxygen supply connection, for its ability to connect a secondary reserve tank to support a facility until an emergency support source is located. Contrary to popular belief, emergency oxygen tanker trucks require some lead time to deploy.
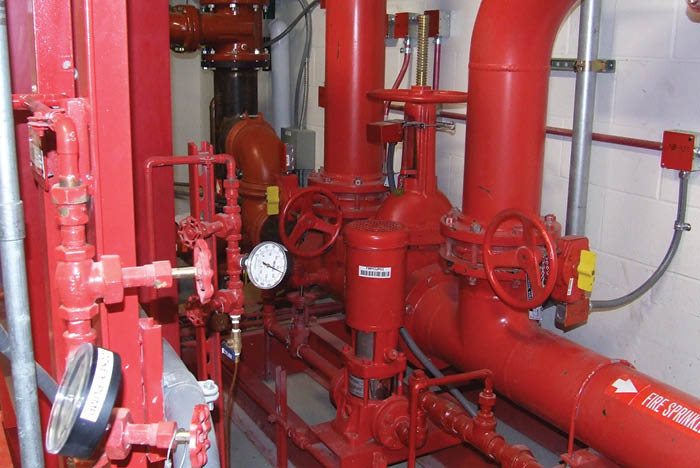
Fire sprinkler systems are dependent upon the public utility water source and delivery means.
Image courtesy of ASHE
Fire systems. Fire alarm and fire sprinklers are designed to alert occupants and suppress fires until emergency services arrive.
- Fire alarm. The fire alarm system consists of devices designed to detect and alert occupants of a building that a potential issue may be present. In the case of a major event, there might be a situation where water enters a device, causing a ground fault condition that will place the main fire alarm control panel in jeopardy and temporarily disabling that specific circuit for monitoring the space. It is best practice to have all primary point of contact information on the inside of the panel and also at a remote location for emergency response situations.
- Fire protection (sprinklers). Sprinklers are designed to suppress, not extinguish, a fire. A facility may have several types of sprinkler systems, including pre-action, dry, antifreeze, special hazard and, most commonly, wet systems. Fire sprinklers are dependent upon the public utility water source and delivery means. If a tornado strikes the water tower near a facility, the situation must be mitigated.
Power systems. Facilities are dependent upon reliable power sources to support the physical environment. Just how reliable is the public utility source, and are there any potential transmission issues that might be a risk to the facility? Facilities managers should partner with the local utility provider to test transmission lines and utility alternate feeds and substation maintenance.
It is imperative to test emergency power systems at a regular interval to ensure functionality in the event of an emergency. Facilities managers should look at the system as a whole component and not only as several separate pieces. Elements such as proper maintenance of fuel supplies, fresh air and exhaust air damper operation for the prime mover, transfer switches, synchronous gear for multiple generator sets, transfer switches, load shedding capabilities, distribution breakers and circuitry, battery backup emergency lighting, electrical riser diagrams, sequence of operation, emergency connection points for external load banks or temporary rentals and thermal imaging studies are just a few items in the overall emergency power system to consider as failure points.
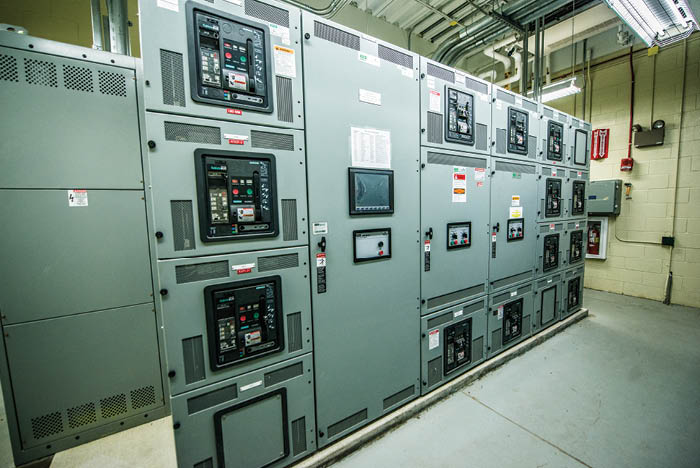
Synchronous gear for multiple generator sets is one of many items in the overall emergency power system to consider as a failure point.
Image courtesy of ASHE
BAS and HVAC systems. The building automation system (BAS) has the capability to do more than monitor and control the HVAC equipment. An integrated BAS can give a facilities manager the ability to monitor and control an entire building remotely using a secure web portal.
One must remember that any BAS is a diagnostic tool, and user interface actions must be field verified for accuracy of action. As technology advances, so does the ability to integrate systems into a robust BAS. Facilities managers must know their systems and the weak points in the chain of operation to mitigate an emergency.
HVAC functions are imperative to the operation of the physical environment, from specially pressurized rooms to patient comfort. When the HVAC system fails, the domino effect of clinical support fails. Pharmacy, radiology, surgical services, the sterile processing department and critical patient environments also fail. What is the redundancy and reliance of such systems?
The BAS and mechanical equipment work as a system to maintain the physical environment for patient care.
Other systems. Lighting systems are becoming more complicated than a simple switch to turn lights on and off. Is there a process to override the system in the event of a system failure? Improper lighting, or lack of lighting, can affect the moods of visitors, staff and patients, and can lead to errors and accidents.
The pneumatic tube system is a vital piece of building infrastructure supporting multiple departments with goods and products. A large campus might have miles of pneumatic tube, user stations and transfer stations all controlled by a central server. What implications are there if a patient laboratory sample gets lost or damaged in the tube system and a repeat sample must be obtained?
Other items to consider are supply chain issues related to obtaining goods and services needed to support the facility in an adverse weather event.
Frequent and widespread
Adverse weather events are becoming more frequent and widespread. Adverse weather-related events that might have existed in the past may no longer be the norm for the future.
The extreme cold temperatures experienced in Texas during February 2021 are a good example of how impactful this can be, bringing widespread impacts to large areas and many communities when temperatures are reached that facilities are not typically designed for nor equipped to address.
Regardless of the normal type of weather an area experiences, it is important to consider varying weather extremes in organizational EOPs.
Coordinating emergency ops with hospital utility failure plans
In last month’s “ASHE Tools” column, Jordan Plyler and Dave Dagenais provided an overview of the importance of the hazard vulnerability analysis (HVA) in emergency preparedness planning. As they reminded readers, an HVA is the foundational element used to develop a facility’s plan to mitigate, respond to and recover from emergent situations.
While the HVA is used to help develop the emergency operations plan, it is often not used as the foundation for developing utility failure plans. This is because these plans are generally developed under the scope of utility failure without reference to the cause of the failure. Understanding that a “hiccup” in the essential electrical system could be a sign of a larger issue within the system that could impact patient care if it is not properly communicated is often overlooked in utility failure planning.
Taking a much broader view, including the information developed within the HVA, along with operational processes for the various utilities within a health care facility, is vital for the proper development of utility failure plans.
For more information on the development of comprehensive utility failure plans, readers can access the Compliance+Operations article, “Comprehensive utility failure plans,” from the September 2019 edition of Health Facilities Management and available at hfmmagazine.com/articles/3761-comprehensive-utility-failure-plans.
Article by Michael Huff, CHFM, CHC, CHCPE, CPMM, CRCST, CHL, facility manager at Baylor Scott & White Health. He can be reached at autoclave1@hotmail.com.Sidebar by Jonathan Flannery, MHSA, CHFM, FASHE, FACHE, senior associate director of advocacy for ASHE.
About this article
This is one of a series of monthly articles submitted by members of the American Society for Health Care Engineering’s Member Tools Task Force.