Eight steps to sustainability
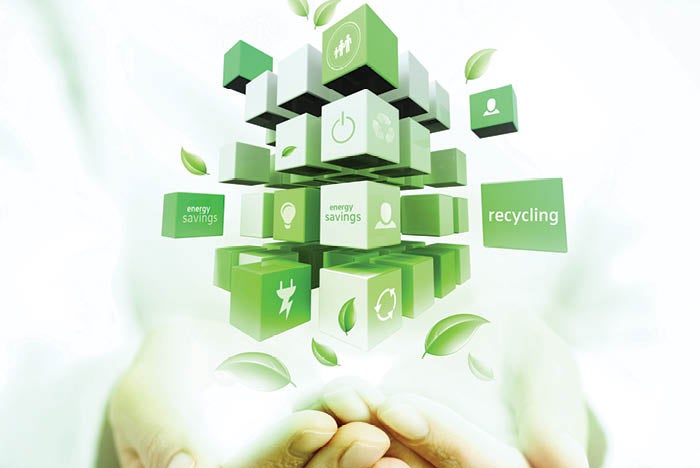
Image by Getty Images
The American Society for Health Care Engineering’s (ASHE’s) new “ASHE Sustainability Guide” provides step-by-step directions for developing and executing a sustainability program for a health care facility.
The guide, from which this article was excerpted and edited, focuses on facilities management but could inform other programs.
Whether facilities managers are embarking on a new journey or solidifying an established effort, the guidance can help define a path to sustainability. Advice in the guide covers the following eight steps:
Step 1: Establish a green team
Implementing sustainability initiatives requires participation from individuals and departments throughout an organization, from senior leadership to front-line workers. Like any organizationwide effort, successful sustainability programs require skilled, accountable staff; adequate resources to meet organizational goals; and a clear understanding of roles and responsibilities.
Responsibilities for sustainability programs are often decentralized, which makes implementation of institutional goals and action plans a challenge. This section of the sustainability guide suggests methods for creating committees or teams, but the main objective of each approach is to create a framework that brings together decision-makers and those who implement their decisions.
Green teams (or other formal energy working groups) are critical to the success of an energy-reduction plan. If a green team already exists, facilities managers should consider adding energy management as a standing topic to its agenda. They should ensure they have the correct stakeholders engaged at the table, including a sustainability champion; the chief financial officer or one of their direct reports; an executive sponsor, ideally a champion from the C-suite; operational leaders from departments such as facilities, environmental services, space planning, supply chain and nutrition services; clinical leaders who have influence throughout the organization; a project or construction manager to help manage implementation and coordination efforts; a communications, marketing or public affairs leader; and passionate front-line staff, including doctors and nurses.
Unless responsibility for environmental programs is someone’s full-time job, most participants on these committees serve on a volunteer basis. For the most successful committees, it’s important to find a balance between staff who must participate, and motivated staff members who want to participate.
Step 2: Create an energy management plan
The foundation of any sustainable program is its data, and to achieve success, facilities managers will need to have a comprehensive understanding of their operations, energy consumption and improvement opportunities. The following activities are designed to help evaluate existing efforts, understand and inventory energy use, and provide an assessment of priority activities.
Assess the program. The first step in creating an energy management plan involves an analysis of where a facility’s program currently stands. Facilities managers can use the ENERGY STAR® Energy Program Assessment Matrix to compare their energy management practices to the best practices outlined in the Environmental Protection Agency’s (EPA’s) “ENERGY STAR Guidelines for Energy Management.”
Track energy use in the Energy to Care Dashboard. ASHE developed the Energy to Care Dashboard, a confidential and complimentary energy management tool to help health care facilities track, manage and communicate energy savings. The dashboard, designed for easy use and to reduce user burden, offers a tailored, at-a-glance view of a health care facility’s energy and water use and provides an array of capabilities to help health care facilities achieve their goals, including tracking greenhouse gas (GHG) emissions.
The dashboard integrates with the ENERGY STAR Portfolio Manager®, a free tool developed by the EPA that can be used to benchmark energy consumption and compare a facility’s performance to similar buildings nationwide. As monthly utility data is entered in Portfolio Manager, the Energy to Care Dashboard automatically updates to reflect these changes.
Establishing a baseline against which future reductions will be measured is an important first step in tracking progress. Once a baseline has been established, an organization can continue to track consumption on an ongoing basis and quantify the savings from reduction efforts. It’s important to begin to track energy and GHG reductions to verify they are meeting the intended goal, to track cost and operational savings, and to report on all successes or failures to inform next steps and give them traction.
Develop an energy use profile. An energy use profile will demonstrate how energy use is distributed among building systems as well as identify the energy source for each system. Breaking down energy consumption data by discrete systems allows a more strategic approach to targeting improvement efforts. Further, including cost in the baseline and energy use profile will make it easier to recognize best opportunities for improvement.
Step 3: Complete a GHG emissions inventory and set targets
GHG emissions inventories account for the quantity and sources of GHG emissions that can be attributed to an organization based on its operations. Aside from the fact that some communities and states require organizations to prepare GHG emissions inventories through mandatory GHG programs, there are several reasons why taking the time to account for an organization’s GHG emissions is a valuable exercise.
By developing a GHG inventory, a health care facilities team can better understand the organization’s impact on the environment, identify opportunities to reduce GHG emissions and achieve recognition for reporting successes. Because GHG emissions link directly to energy conservation efforts, accounting for emissions is a key next step in an organization’s pathway to sustainability.
The EPA Center for Corporate Climate Leadership recommends the following steps, which align with the global standard for calculating corporate GHG emissions as developed by the World Resources Institute and the World Business Council for Sustainable Development: 1) Scope and plan inventory; 2) Collect data and quantify GHG emissions; 3) Develop a GHG inventory management plan; and 4) Set a GHG emission reduction target, and track and report progress.
By defining targets with fossil fuel emissions in mind, an energy use analysis may account for on-site renewable energy and utility company renewable supply sources, reductions in energy demand, and renewable energy credits that can help the facility team realize its goals to reduce both energy use and emissions.
Facilities managers should use the data gathered during baseline-setting, energy use profile and GHG inventory processes to establish reasonable, SMART (Specific, Measurable, Achievable, Realistic and Timely) goals that are consistent with a basic, intermediate or advanced approach. The target goals will inform which performance improvement measures to implement to achieve them.
Step 4: Execute efficiency measures
Once an organization’s energy is tracked, goals are set and other sustainability priorities are identified, facilities managers can use this information to develop a strategic action plan outlining steps to be taken and project implementation details. This plan should include an integrated approach to all aspects of energy management, including short- and long-term reduction strategies.
Managers should implement projects identified in the strategic action plan that will result in energy and emissions reductions for their facilities. They may consult Energy to Care’s energy conservation measures, which is a comprehensive list of measures or projects, designed to allow facilities managers to choose those most supportive of their goals.
Step 5: Address other aspects of sustainability
Environmental sustainability requires dedicated effort and a continuous series of incremental improvements in multiple operational areas. Fortunately, facilities managers can follow a framework similar to that outlined in Step 2. Like energy, sustainability management in other operational areas begins with benchmarking. A look at some other areas of sustainability includes:
Water. According to Michigan State University, the rate of increase in water and sewer costs is outpacing every other utility in the U.S. Scarcity, climate change, political changes, aging infrastructure and water quality are all contributing factors to these price increases, though the specific driver will vary depending on location.
Facilities managers can use ENERGY STAR Portfolio Manager to track their facility’s water consumption and learn more about how efficiently the organization is currently managing water use. Just like energy data, they will need to gather water bills to account for all water sources used by the facility. Major sources of water consumption in hospitals are typically heat rejection from cooling towers, water use in process equipment like sterilizers and reverse osmosis machines, domestic fixtures, food service and irrigation, depending on the facility’s location.
Waste reduction. Hospital waste is generally classified in four categories: recyclables, general waste, red bag waste and hazardous waste. With each waste classification comes a different level of cost and environmental impact. ENERGY STAR Portfolio Manager can be used to track and assess how a health care facility currently manages waste.
Nutrition. The environmental impact of food has emerged as a hot topic in sustainability circles as more information becomes available and alternate solutions are developed. Meat in general, and beef in particular, have been targeted for their environmental footprints.
Hospitals can track the food portion of their organization’s nitrogen footprint using SIMAP®, a web-based carbon- and nitrogen-accounting platform that can track, analyze and improve their campuswide sustainability.
To do so, facilities managers will need to work with their dining providers to collect information such as the weight of individual food items purchased, description of food items purchased and time frames for food purchases.
Refrigerants and specialty medical gases. Refrigerants and specialty medical gases are potent GHGs that are often hundreds or thousands of times more impactful than carbon dioxide in terms of their global warming potential and low ozone depletion potential.
Unfortunately, most current benchmarking tools do not provide a mechanism for tracking refrigerant and medical gas use. However, facilities managers can use data from their GHG inventory to inform this effort and vice versa.
Step 6: Develop a measurement and verification protocol
Facilities managers should develop a measurement and verification (M&V) protocol to quantify savings and determine a method to report these savings to stakeholders to clearly demonstrate the sustainability program’s effectiveness over time. An M&V plan should verify energy savings thoroughly, such that all relevant parties are reasonably comfortable with the accuracy of the savings identified.
It is important to identify an M&V protocol as early as possible in a sustainability program, including establishing a baseline. Unlike office buildings, health care facilities typically undergo frequent additions, renovations, equipment upgrades and more. This dynamism must also be considered when designing an M&V program. Facilities managers should be prepared to maintain changes to the baseline data in a way that will allow others to understand and follow its progression.
Typically, energy projects will sustain some level of “snapback” or “backsliding” each year depending on the type of effort as a result of normal building operations, such as responses to broken equipment or complaints. These small instances can often be forgotten and slowly add up to reduction in energy savings. For large projects or investments, this can represent a significant cost, and an effective M&V strategy can be utilized to maintain results.
Once the M&V methodology and plan is in place, facilities managers should make sure it is followed. They should staff the effort accordingly and ensure updates are communicated to the sustainability team and sponsors on a regular basis.
Step 7: Create an operations and maintenance training plan
Proper training for health facilities operations and maintenance (O&M) personnel is key to optimum building performance, with performance defined by maintaining appropriate space temperature, humidity and pressure using the least-possible energy consumption.
This is particularly important in health care with its complex space uses, code requirements and ages, and building shapes and configurations. Operators must understand the systems used to provide the performance as well as the intention behind those systems if they are to effectively maintain or optimize building performance.
Regardless of a facility’s age, size or equipment sophistication, every organization should have an O&M training program and track staff qualifications to ensure they are adequately trained to operate and maintain existing and planned systems. A recurring training program should account for the skills required, the available labor pool in the geographic area and staff development opportunities. The training must explain the systems’ purpose to allow the operators to make informed decisions. Additional significant benefits from job training include productivity and job satisfaction, which are critical in staff development and retention.
O&M training should cover two important topics: equipment training and systems training. Equipment training covers the specifics required to operate and adjust devices, while systems training educates operators on what the equipment is supposed to do and how it fits in the overall system function to meet building performance.
Step 8: Educate, promote successes and celebrate!
Effectively communicating the need for sustainability and providing training and guidance on how to implement specific strategies can help an organization achieve greater reductions and gain more support for initiatives.
Success is easier to achieve when users understand the reasons for any changes (the goals), receive training on work practice changes (how to engage) and are regularly informed on how action plan progress is matching up to goals (progress reports). Education should be formal, with specific learning objectives, such as compliance or policy-related trainings that should be documented; and informal, with educational materials including posters, newsletters, e-blasts and other media.
Because much of what facilities staff members do can go undetected, it’s especially important to highlight sustainability initiatives and bring awareness to every level of the organization. Doing so will demonstrate the value that the health care facilities team and green team bring to the organization and engender an environment for positive change.
Information on Energy to Care
The American Society for Health Care Engineering’s (ASHE’s) Energy to Care Program helps facilities management professionals reduce energy consumption, providing value to the organization and improving patient care. The Energy to Care website at energytocare.org contains an abundance of resources to assist health care facilities on their sustainability journeys, including:
- Energy to Care Toolkit. These resources help health care organizations reduce energy use and get the most value out of ASHE’s Energy to Care Program.
- Energy to Care Benefits Calculator and Talking Points. The ASHE Energy to Care Benefits Calculator is an estimating tool that uses actual results and data provided by ASHE Energy to Care Program participants to highlight a tailored range of program benefits; the Energy to Care Talking Points document helps facilities managers make their case for joining the Energy to Care Program to senior leadership.
- Success stories. This enables facilities managers to learn more about the health care facilities that have seen energy savings through the Energy to Care Program.
- Monographs. Facilities managers can browse through ASHE’s extensive collection of publications that cover topics in clinical/biomedical engineering, facility engineering, design and construction, and safety and security management.
This article was excerpted and condensed by Health Facilities Management magazine staff from the new “ASHE Sustainability Guide."