Handling indoor air quality concerns
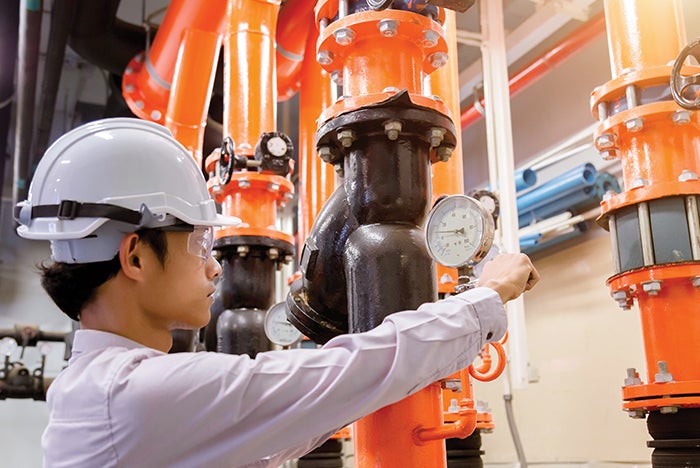
Whether a facility’s HVAC maintenance is contracted out or performed in-house, the level of competency of the maintenance providers is critical.
The old adage, “An ounce of prevention is worth a pound of cure,” holds true when addressing indoor air quality (IAQ) concerns. Consequently, looking at a facility holistically and from different angles allows facility managers to put multiple safeguards in place to minimize the probability an IAQ issue will develop.
One of the best accident causation models of this practice is the “Swiss cheese” model conceptualized by James T. Reason (2000). The purpose of the model is to identify and improve the multiple layers of protection (i.e., slices of Swiss cheese) between the hazard (i.e., poor IAQ and mold) on one side of the model, and patients and employees on the other side.
The slices represent the engineering and maintenance elements a facility may or may not have in place to keep the hazard from reaching the patients or employees. The size of the holes in the cheese represent the various opportunities or failures within the current system that need to be addressed to either fill the holes or reduce them in size.
If a facility manager reduces or eliminates the number of holes in a facility’s Swiss cheese, the possibility of the hazard reaching patients or employees is greatly reduced. Following are a few of the layers of the Swiss cheese that a hospital leadership team can evaluate or introduce to a hospital maintenance program to eliminate or minimize the potential of IAQ issues from developing:
Design and installation. An often overlooked element in the prevention of IAQ issues is the proper design and installation of HVAC systems. Two significant considerations for a manager during any project, especially those involving HVAC projects, is time and money.
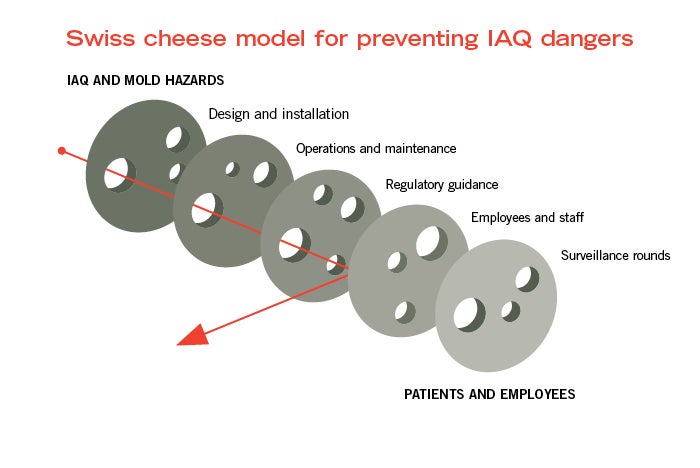
The overemphasis on these items particularly at the design stage can result in long-term problems that often consume more time and cost more money in the long run. Therefore, the ability to articulate value for money with hospital leadership will go a long way toward the prevention of IAQ issues.
Operations and maintenance. Whether a facility’s HVAC maintenance is contracted out or performed in-house, the level of competency of the maintenance providers is critical. If these activities are performed in-house, facility managers should ask: Do the maintenance personnel truly understand the functionality of the systems they are maintaining? Do they understand the criticality of the role they fulfill when maintaining the equipment? Do they understand all the parts and components and ask questions when something is not fully understood?
Resources
Pride and years of experience are valuable attributes but often can be given too much credit when it comes to maintenance functions. Employees, especially experienced ones, need to understand that maintenance tasks are highly complex and ever-changing. Being transparent and reminding these employees to ask questions when they are unsure is important. Facility managers must determine if scheduled maintenance activities are being performed on time and correctly. Making unannounced visits to a few select maintenance tasks might result in ideas for process improvement.
The employees maintaining these systems must receive ongoing education and information on the systems they are maintaining. This training often can be performed by manufacturers of the equipment being used at the facility. Inviting manufacturing representatives for a visit may be warranted, not only to collaborate and discuss ongoing education, but to identify key personnel when assistance is needed on future issues.
If HVAC system maintenance is contracted to an outside firm, the relationship the facility manager develops with them is critical. The competency of these firms and their employees must be verified as well as the quality of their work. Are vendors meeting the required scheduled maintenance deadlines? What are the qualifications of the personnel they are sending to the facility? Is the facility department getting what it pays for?
Finally, staying current with required and proactive maintenance takes a comprehensive program. Not only does a computerized maintenance management system (CMMS) serve as an electronic repository for maintenance records and files, it is a living system to ensure that utility systems are being properly maintained according to manufacturer requirements, best practices and other regulatory agencies.
The CMMS, which often runs the facility work order system, allows a facility manager to view and track the scheduled maintenance for each piece of equipment in a facility. The improper maintenance of this equipment is “ground zero” for many of the IAQ issues that receive coverage in the media.
Regulatory guidance. Several agencies have issued publications on IAQ. Some of these organizations have focused specifically on health care, and others have provided general guidance that can be utilized across multiple fields. The two most common standards referenced in health care environments is ASHRAE Standard 170, Ventilation of Health Care Facilities, and ASHRAE Standard 62.1, Ventilation for Acceptable Indoor Air Quality. The Facility Guidelines Institute (FGI) also has incorporated IAQ specifications into its guidelines and incorporated these specifications under the various hospital utility systems, including electrical, plumbing and mechanical.
Other governmental agencies, such as the Centers for Disease Control and Prevention (CDC) and the National Institute for Occupational Safety and Health, have addressed IAQ concerns and provided several guidance documents, especially as it pertains to general buildings and schools. These are a good source of information that can be easily incorporated into a hospital environment and corresponding policies and procedures.
A CDC document titled “Guidelines for Environmental Infection Control in Health-Care Facilities” is another good source for additional information. This document is broken into sections and covers key areas for the mitigation of IAQ issues.
Another item to note is the recent addendum to ASHRAE Standard 170-2013. This addendum, currently in public review, outlines the establishment of a ventilation management committee to oversee ventilation issues within hospitals. This committee is similar in structure and format to the ASHRAE Standard 188, Legionellosis: Risk Management for Building Water Systems, water management committee. This is something facility managers should keep on the radar as this addendum works its way through the approval process.
Employees and staff. An organization’s environmental, health and safety (EHS) professional is often a vital source of information on IAQ issues and solutions. They are responsible for overseeing employee safety and health throughout the facility and, therefore, are involved in injury and illness reporting and investigation, near-miss and hazard reporting, along with hazard management. Facility management must investigate these claims and complaints to determine validity and root causes, ultimately implementing corrective actions. Another source of information is the environment of care (EOC) committee, which may have data on employee complaints and solutions.
To start, facility managers can look into the Occupational Safety and Health Administration injury and illness records. These reports record the name, occupation and specific location of an incident. Once a location has been identified as a concern, investigating these issues can start with a simple worker interview or survey of the employees from that location or department. Facility managers can ask questions regarding odors, symptoms (e.g., headaches and respiratory irritation) of the suspected illness- or injury-causing environment or agent. Additionally, managers can consider worker complaints or hazards that have been reported through an organization’s hazard reporting process or via the EOC committee.
The EHS group also will have information taken during a survey or walk-down of the area of concern. This survey is conducted by the safety professional, along with other members of management, such as a facility engineer or maintenance manager and members of the EOC. During this survey, the following criteria may be documented: room size, HVAC system evaluation, temperature, humidity, air flow, carbon monoxide/carbon dioxide and volatile organic compounds. These results may indicate the need for further investigation involving an industrial hygienist or environmental sampling performed by an outside laboratory.
Non-EHS employees and staff are another good source of information about IAQ issues. The follow-up and investigation of staff concerns may provide a facility manager with the opportunity to address small issues before they become concerns. An employee complaining of watery eyes and cold-type symptoms may be the result of a potential indoor air quality issue. Therefore, a basic review of the work environment may be warranted. Checking for water infiltration and conducting basic temperature, humidity and carbon dioxide measurements are often inexpensive and may not require intrusive processes.
These basic checks should give facility managers enough information to determine if the situation warrants further investigation or whether there is some other underlying cause of the complaint. At a minimum, these checks often will stop the small issues from becoming large issues as well as letting employees know that IAQ is a priority and their concerns are taken seriously.
If further investigation is needed, an outside firm with expertise may be engaged. Pre-planning and coordination of these projects with internal and external personnel is critical to success. The relationships developed with external parties and vendors will help identify their strengths and weaknesses as they pertain to testing, inspection and abatement. More importantly, some of this testing and inspection may be destructive in nature and have substantial impacts to patient care and facility operations. It is important to have a plan in place before an indoor air quality issue develops rather than guessing on the next steps when an issue is identified.
Surveillance rounds. The completion of hazard surveillance rounds helps comply with Joint Commission Standards EC 02.06.01 and, specifically, EC 02.01.01, which states “the hospital must implement a process to identify safety and security risks associated with environment of care that could affect patients, staff and other people coming into the hospital.”
In addition, under Standard EC. 02.05.05, the hospital, when performing repairs or maintenance activities, “must have a process to manage risks associated with air quality requirements; infection control; utility requirements; noise, odor, dust and vibration; and other hazards that affect care, treatment, or services for patients, staff and visitors.”
The performance of hazard surveillance rounds, as it relates to IAQ, provides a key opportunity to identify IAQ issues. Again, it is critical to be involved and take action in these activities to eliminate potential concerns before they become real problems.
A good first step involves facility managers working collectively with infection prevention and EHS specialists to identify potential issues. Including a comprehensive hazard surveillance rounds checklist that includes items that correlate to proper IAQ will provide some guidance as well as data trends for future rounding.
Some things to evaluate include the presence of water stains on walls and tiles. The observation of these conditions may indicate an ongoing issue. Other questions include: Are room pressurizations correct? If the rooms are monitored and data logged, are these data being reviewed and corrected when a deviation occurs? Are these corrective measures being documented?
Overall, is the facility maintaining the humidity, temperature and air exchanges according to ASHRAE 170 and other governing bodies? Are IAQ issues being incorporated into rounding? Are facility staff looking above ceilings and periodically checking roof areas to ensure the building envelope is watertight and the roof and equipment drains are clear.
During construction-related activities, the inclusion of IAQ items can be evaluated jointly with hospital infection prevention staff, which begins with the thorough completion of an infection control risk assessment and pre-construction risk assessments. (Log on to www.ashe.org/icraassessment to access ASHE’s Infection Control Risk Assessment Matrix of Precautions for Construction & Renovation).
Without proper planning and control of dust mitigation, construction projects can be linked to the development of IAQ issues and hazards. The planning and mitigation of all potential concerns will go a long way to prevent the small issues from becoming major problems.
Evaluating IAQ concerns from different angles and with different controls — including engineering, management, personnel, facility, environmental and safety — is critical to their prevention because most incidents have multiple contributing causes.
Complex and challenging
The thought of indoor air quality issues can be complex and challenging for facility managers. This advice hopefully provides a starting point and some direction to proactively address IAQ issues.
In the end, group collaboration is a good strategy and may help managers fill the holes in the Swiss cheese model to provide patients and staff with a safe and secure care environment.
Joseph Losko, D.Sc., CSP, CHMM, and Rona Smeak, Ph.D., CSP, are assistant professors in the safety management department at Slippery Rock (Penn.) University. They can be reached at joseph.losko@sru.edu and rona.smeak@sru.edu.