Fuel polishing aids facility in emergency power readiness
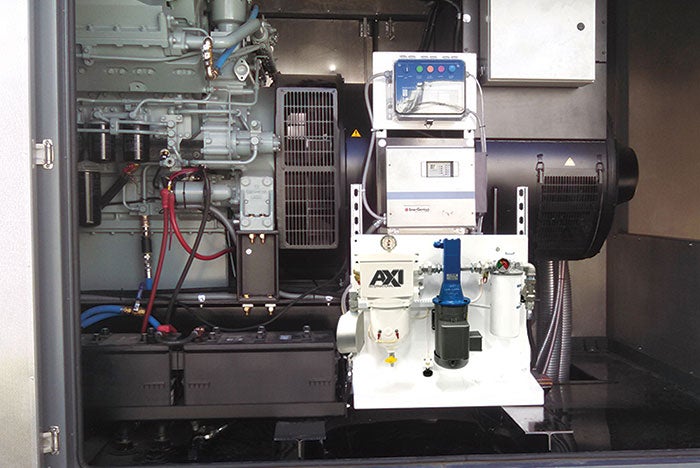
Fuel polishing helped the medical center to maintain optimal fuel quality for its emergency power.
All health care facilities like the Penn State Health Milton S. Hershey (Pa.) Medical Center count on their backup power systems to function effectively during an outage. As a critical component of the backup power system, diesel fuel stored for emergency use must be maintained in optimal condition to ensure startup and runtime of backup generators.
Jeffrey Dove, associate director of facilities and maintenance at Hershey Medical Center, and his team understand the importance of maintaining a clean fuel supply for the medical center’s emergency backup system. To address the need, they installed automated fuel maintenance systems.
Fuel supply quality is important for meeting National Fire Protection Association (NFPA) 110, Standard for Emergency and Standby Power Systems, paragraph 7.9.1.3. It says that fuel “tanks shall be sized so that the fuel is consumed within the storage life or provision shall be made to remediate fuel that is stale or contaminated or to replace stale or contaminated fuel with clean fuel.”
In addition, the Centers for Medicare & Medicaid Services has increased emphasis on fuel quality. Its Conditions of Participation for the Final Rule at 42 CFR 482.15(e)(3) states: “Emergency generator fuel. Hospitals that maintain an on-site fuel source to power emergency generators must have a plan for how it will keep emergency power systems operational during the emergency, unless it evacuates.”
The quality of the fuel also impacts the lifespan of equipment it powers and the fuel system itself. Fuel usage at Hershey Medical Center is minimal. In fact, the only fuel that the facility uses is for mandatory 30-minute burn tests on backup power generators. At times, 90-minute to four-hour tests are performed during load bank testing.
“That’s part of the problem,” Dove says. “We keep 30,000 gallons of fuel on hand, but we don’t go through it quickly.”
Stored fuel that sits is prone to microbial growth, sludge and other forms of contamination. Contaminated fuel wreaks havoc on a system in the event of a power outage by clogging fuel filters and destroying injectors, potentially preventing the backup power system from working effectively or at all.
If overlooked, improperly maintained fuel can create immediate operational liability and a self-propagating cycle of accelerated asset depreciation in the form of fuel system corrosion and component failure.
According to Dan Chisholm Sr., chairman of the NFPA 110 technical committee and a consultant on health care emergency power supply systems, fuel problems are the No. 1 cause of generator failures after the generator has started and is online. “The purity of the fuel reaching the injector pumps and injectors is of paramount importance,” he says.
Before the installation of the fuel maintenance systems, the facility typically would polish its fuel supply using a portable fuel polishing unit.
“We’ve always done an annual fuel test,” Dove says. “This involves taking a diesel fuel sample from our 30,000-gallon storage tank and sending it to a lab to have it tested for dirt, suspended solids, microbial growth and other contaminants.
“Although the samples always passed the tests, the mobile fuel polishing systems would still remove 200 gallons of sludge from the fuel tank,” he says.
Dove and his team knew that their current fuel maintenance procedures could be improved for future generator and fuel tank installations. After considering different options, they decided on installing two AXI International FPS-LX-F fuel polishing systems in their generator enclosures to maintain optimal fuel quality. Each of the automated systems services a 13,000-gallon belly tank.
By automatically separating water from the fuel, filtering out contamination and conditioning the fuel, the polishing systems can achieve and continuously maintain the quality of the stored diesel fuel.