Monitoring construction vibration
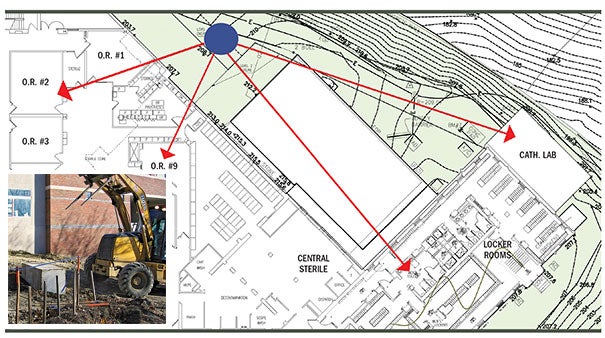
Left: Drop-weight testing for vibration. Above: A map showing the source and response locations of a drop-weight test.
While a new building provides a health care organization with an exciting state-of-the-art facility, the construction process itself can impact the overall operations of the organization.
For instance, it is well-known that construction activity produces vibration. What is less clear is the effect the vibration will have on nearby buildings.
Organizations hope that work in adjacent buildings can continue as usual during construction, but this may not be the case depending on many factors, including the type of construction, the proximity of the site and the sensitivity of the equipment. Fortunately, it is possible to assess the vibration sensitivity, predict potential impacts, provide mitigation and keep tabs on the vibration during construction.
Quantifying sensitivities
Construction vibration monitoring is required at most building sites and is usually provided by the contractor. The primary purpose of this monitoring is to address structural damage to nearby buildings and it is usually accompanied by pre- and post-construction crack inspections.
However, these are not the only problems experienced by health care facilities professionals. In addition, some activities and equipment can be affected by extremely low levels of vibration, in many cases far below the level of human perception.
In a hospital environment, vibration concerns relate to such sensitive areas as operating rooms, microsurgery suites, procedure rooms, pathology labs and in-patient areas; and such devices as magnetic resonance imaging (MRI), computed tomography (CT), nuclear magnetic resonance, cyclotrons for proton beam therapy, microscopes and lab equipment. The Facility Guidelines Institute’s 2014 Guidelines for Design and Construction of Hospitals and Outpatient Facilities recommends that floor vibrations be limited to 6,000 microinches per second (mips) in patient rooms and 4,000 mips in operating and other procedure rooms.
This is a velocity measurement that is evaluated in 1/3-octave frequency bands, which are commonly used to describe structural vibration and have the curious property of getting wider as the frequency increases. For example, the 5-Hertz (Hz) band includes vibration energy from 4.47 Hz to 5.62 Hz, whereas the band at 40 Hz extends from 35.5 Hz to 44.7 Hz. As a point of comparison, 4,000 mips is about the threshold of perception for the most-sensitive humans.
The manufacturers of most vibration-sensitive equipment provide clearly defined criteria for acceptable levels of floor vibration. In many cases, these criteria depend on the frequency of the vibration. For example, the criterion for a particular electron microscope is 130 mips at 5 Hz, but it is 1,100 mips at 20 Hz, more than eight times higher. When considering the effects of potentially disruptive vibration, both the magnitude and the frequency are equally important in determining whether there may be an issue. This is significant because conventional construction vibration monitors typically are not capable of measuring extremely low levels of vibration, nor are they able to measure the vibrations at multiple frequencies simultaneously. Specialized sensors and analyzers are required to do this.
Depending on the instrument, specific criteria may not be available. This is particularly true for custom-made research equipment. In such cases, a set of generic vibration criteria is available from the American Institute of Steel Construction (AISC) to characterize the vibration sensitivity of various equipment types.
The AISC Design Guide 11 outlines generic criteria that are commonly known as vibration criteria (VC) curves and are identified by letter grades. VC-A is equivalent to a level of 2,000 mips and is commonly used as a criterion for general lab areas where equipment such as benchtop microscopes are used. The VC curves refer to floor vibrations and are also defined in terms of 1/3-octave frequency bands.
Vibration predictions
Vibrations from construction equipment are difficult to predict. The vibrations depend on many factors, including the type of equipment, the soil, proximity to the construction and the building response. The soil is important because it affects the amount of vibration generated at the source and how the vibrations propagate from the source to neighboring buildings.
Representative equipment tests. On-site tests with representative construction equipment provide the best way to evaluate how much construction-related vibration can be expected in neighboring facilities. Live tests are attractive because they utilize the actual construction equipment: the vibrations propagate through the soil into the building and the building responds as it would during construction. Additional factors need to be considered, such as the location of the activity with respect to the building, but these can be addressed within the test plan where, for example, the tests can be conducted at various distances from the sensitive facility.
The principal drawback of a full-scale test is the need to mobilize equipment. A typical test can be completed in a day. However, there is still a cost associated with getting the equipment to the site and in providing operators. Also, depending on the conditions at the site, it may not be possible to get the equipment to the required location or to conduct representative construction work, such as at a planned construction site where a building is not yet demolished.
One other benefit of a full-scale test is that it allows occupants to experience the vibrations firsthand. If users are aware of the testing, they can monitor their equipment and look for anomalies. Most users find the construction-related vibrations to be underwhelming in the sense that they are not nearly as bad as they thought they would be. This has an obvious benefit of managing expectations once construction begins.
Controlled source tests. A reasonable alternative to representative equipment tests makes use of a controlled source to excite the soil. The source levels then can be scaled to mimic specific pieces of construction equipment. While the source levels must be estimated, the rest of the parameters in the propagation chain, the soil, and the building response, are still as they will be during construction.
At New England Baptist Hospital in Boston, for instance, a large concrete weight was dropped at a location on the planned building site. The vibration from the drop test was measured at a reference location 25 feet from the impact point. At the same time, the vibrations were measured at four locations inside the hospital. The measurement locations included operating rooms, an MRI suite and a CT suite. The vibration transfer characteristics between the reference point and the hospital locations were evaluated from the drop tests. The construction-related vibrations inside the hospital then were calculated by scaling the reference vibrations based on the equipment to be used on a frequency-by-frequency basis.
The analysis for this particular case study showed that some operating rooms and the MRI and CT suites would not be usable during some phases of construction, such as excavation and soil compaction. This allowed the hospital to schedule procedures accordingly during the project.
Non-testing calculations. Finally, it also is possible to obtain rough estimates of construction-related vibration without testing. Representative source data are available for various types of construction equipment. General soil propagation models are also available and it is possible to predict building response based on its structural configuration. These calculations do not provide the best prediction, but they can be used to obtain rough estimates of the level of vibration that might be expected during construction.
Vibration mitigation
When the prediction process results in significant impacts on neighboring facilities, there is usually an effort to investigate alternate means and methods to reduce vibration. It also might be possible to accommodate construction-related disruptions by way of scheduling, either the construction itself or the timing of the sensitive activities.
Even with alternate means and methods and scheduling, there still may be equipment items that cannot be used during construction. If this is not acceptable to the institution, it might be possible to provide local mitigation to protect the equipment. Various commercial isolation products are available for vibration-sensitive equipment.
These range from tabletop isolation platforms to isolated workstations to isolated cradles and tables. Most of these systems utilize air-spring vibration isolators that require a supply of compressed air using house air or a nitrogen bottle (air consumption is minimal once inflated).
Commercial isolation systems are extremely effective, especially at the frequencies that are typical for construction vibration. A good commercial system should be able to increase the vibration tolerance of an instrument tenfold by attenuating the floor vibrations before they reach it.
A supplemental isolation system installed at the University of Minnesota, for instance, was needed to protect a mass spectrometer from nearby construction vibration. Although it was a research application, the approach works equally well in a clinical situation. The system uses a cradle-type isolation platform, which is generally employed to minimize the height that the instrument is raised off the floor. With this isolation system, the mass spectrometer could be used throughout the entire construction cycle.
Construction monitoring
The prediction process provides a very good indication of the sensitive adjacencies that may be adversely affected by construction vibration and when. Many institutions have found it useful to monitor vibrations in real time during the actual construction process. In recent years, the explosion of wireless connectivity has made it possible to monitor vibrations remotely and to access this information in real time.
Project managers and contractors alike have found the live data feeds to be an invaluable tool in maintaining the vibration environment in nearby sensitive spaces. Furthermore, the users of these spaces take comfort in the knowledge that someone is actively watching out for their interests.
A typical monitoring system consists of a set of sensors, an analyzer and a computer with an Internet connection. The sensors are chosen to match the sensitivity of the instrument. The analyzer settings likewise are configured to match the instrument manufacturer’s criteria. The computer stores data locally and can be accessed remotely for download and operation, to change settings, for example.
More importantly, the Internet connection provides the ability to send warning and alarm messages by text or email when preset levels are exceeded. Because the contractor or facility manager typically receives the alarm feed, he or she can anticipate problems and take steps to stop or modify the activity to maintain the low-vibration environment.
Taking action
A small amount of up-front analysis can produce a good understanding of which activities in nearby facilities may be affected by construction. The answer may be positive in that there is no anticipated impact, or it may be negative in that the vibrations are expected to exceed the instrument limits.
But, knowing this allows the project team to use alternate means and methods, schedule construction activity, schedule sensitive activity, make use of supplemental isolation or perhaps move instruments to another location.
Once construction is underway, real-time monitoring is a valuable tool that can be used to continually check that the vibration environment in nearby facilities remains as expected.
jzapfe@acentech.com and mnewmark@acentech.com, respectively.
is president and is senior consultant at Acentech Inc., Cambridge, Mass. They can be reached atControlling construction noise in nearby patient spaces
In addition to vibration, construction sites also produce a considerable amount of airborne noise. The noise can be an issue for sensitive adjacencies like patient rooms, particularly those that have an exterior facade.
Natural light is important for patient satisfaction and the healing process. Unfortunately, windows are the weak link when it comes to noise transmission through an exterior wall. The transmission loss of a double-glazed exterior window might be 20 decibels (dB) worse than a typical 8-inch thick masonry wall. In simple terms, the transmission loss is the ratio between the sound level on one side of a partition to the other. A transmission loss of -20 dB means the sound pressure on the far side of the partition is 10 times lower.
The keys to improving the sound attenuation of a window treatment are layers and air spaces. A single layer of 1/8-inch glass with a 4-inch air space can improve the transmission loss of the window by 10–15 dB. Added layers do not have to be glass. For example, if plywood screens are installed to protect the windows from flying objects, these also can be designed to provide additional sound attenuation.
If window treatments are not enough, sound masking inside the patient rooms can be considered. Sound-masking systems such as white-noise generators make the construction noise less noticeable by raising the background noise in the room.
One issue with sound-masking as a solution is that masking systems are designed to mask human speech, and the windows do a pretty good job of attenuating these frequencies already. Unfortunately, the construction noise that makes its way into the patient room is predominantly low-frequency, and masking systems do not cover these frequencies as effectively.
If isolation and masking do not provide enough benefit, then it is probably necessary to avoid using the patient rooms during construction, or to use them for other purposes. Fortunately, as with vibration, it is possible to make this determination through testing and analysis well before construction begins.
Occasionally, one other source of noise in patient rooms can occur. If the construction produces high-frequency vibration inside the building, these vibrations can produce sound. Essentially, the vibrating walls, floor and ceiling in a room radiate sound much like giant loudspeakers. A good example of this would be a jackhammer being operated directly on the building foundation.
The sound from the jackhammer usually can be heard a long way from the work site. Unfortunately, there is little that can be done to attenuate this vibration once it is in the building structure. However, such work typically is short-lived and can be scheduled at times when the noise is less of an issue.