Performance-based finishes
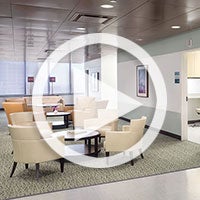
View "Performance-based finishes" Gallery
The body of knowledge and research in the industry is increasing dramatically for designers to one day quantify interior materials as significant tools in meeting the health care organizational goals of improving safety, well-being, worker performance and facilities management.
Circumventing adverse events is a top priority for health care organizations, and evidence-based design professionals are continuing to build a database of usable information to help. To complement this material, however, design professionals also can access evidence from the research specialty of material science.
Complete standards and test result threshold values can be obtained from ASTM International, American National Standards Institute, National Electrical Manufacturers Association, International Surface Fabricators Association, American Association of Textile Chemists and Colorists, or by contacting manufacturers' technical consultants.
This can offer an objective approach to material selection. Moreover, it also can facilitate the removal of subjectivity when key decision-makers are at a standstill in finalizing the desired aesthetic and brand for a new facility.
Hospital requirements
Health facilities professionals can develop matrices to help facilitate performance-based decisions among hospital user groups. This method is incorporated in response to four theoretical hospital requirements — patient safety, patient well-being, staff performance and satisfaction, and functional performance and aesthetics over time — in the following areas:
Public spaces. Reduction of stress and anxiety for optimal patient and visitor well-being is often a top priority for a hospital's public spaces. Health care executives often expect these spaces that form first impressions, such as lobbies, lounges and educational areas, to facilitate customer service, patient access and learning in a beautiful and supportive environment.
The research is strong in testing labs and in the field that materials that absorb sound at the frequency range of human speech will reduce ambient noise. However, the use of softer materials in public spaces often is rejected for fear of excessive maintenance and concerns that the material will not perform over time. These concerns can be eased by accessing industry ASTM testing information. The Carpet and Rug Institute is another source for purchasers and designers to keep informed of updates in technology in meeting the rigors of health facility environments.
Considerations of the abrasive nature of local soil, intensity and frequency of inclement weather conditions, and ease of maintenance and repair also can be addressed by accessing manufacturer testing information.
If there is concern regarding performance over time in areas of high foot traffic, product information for the textured appearance retention rating, and resistance to changes in texture and color might offer reassurance. Other testing results for soft surfaces regarding performance over time include edge-ravel resistance, delamination resistance, moisture-penetration resistance and roll-chair data.
Health care facilities often compromise on a hybrid approach by providing hard material in high-traffic areas with soft-surface flush insets to leverage the performance characteristics of both product classifications in achieving functional and aesthetic performance goals over time.
The modularity of products is another characteristic that is important to address in the material selection process. Smaller modules are easier to remove and replace than products manufactured in larger modules.
Clinical spaces. Health care organizations are strategizing internally to obtain 100 percent hand-washing compliance across all job descriptions. The focus of infection preventionists not only is to modify behavior, but also to modify entire systems to work in concert based on established protocols. The research is conclusive that unwashed hands can transmit organisms to vulnerable patients.
Often the most cautious staff members might accidentally contaminate a recently cleaned or gloved hand by touching an unclean inanimate object close to the point of care. Empirical evidence reveals that an increase in surface cleaning results in decreased organisms available for accidental transmission. Thus, surface materials should work in concert with facility expectations by facilitating the cleaning of hard environmental surfaces, particularly high-touch areas like door knobs, light switches, areas immediately around the patient and surfaces in frequently used work areas.
Referencing the evidence and requirements of the 2003 Centers for Disease Control and Prevention's (CDC's) Guidelines for Environmental Infection Control in Health-Care Facilities can help the design professional to meet this particular patient safety goal.
To facilitate cleaning, hard surfaces must be compatible with the cleaning agent and its dwell time, compatible with rubbing friction and have an appropriate surface assembly, seam and joint integrity. Thus, it is crucial that design professionals check with a manufacturer's representative for testing results regarding compatibility with cleaning agents used in the facility.
About this article
This feature is one of a series of quarterly articles published by Health Facilities Management in partnership with the American Academy of Healthcare Interior Designers.
Solid-surface products offer a tight chemical structure that provides a nonporous property. This correlates to minimal or no water absorption, which is important in wet areas such as hand-washing sink locations. However, solid surfaces can be vulnerable to cracking when exposed to high heat. Comparison of test results across a variety of manufacturers will provide a basis for areas of specification in relation to elements other than work surfaces, such as sinks.
Solid work surfaces also resist impact. When they are specified in highly pigmented colors, however, it is important to note the chemical resistance of the material being considered. This includes the susceptibility to discolor or lose surface luster when exposed to facility cleaning agents and methods. If a particular highly pigmented or dark color is desired, high-pressure decorative laminates might hold up to facility cleaning protocols while offering color performance over time.
Likewise, thermofused, high-pressure decorative laminate is a smart choice for finishing work surfaces in budget-sensitive projects. The thermosetting resins on the top surface of high-pressure laminate provide a nonporous surface layer. However, if surface cracking does occur under the incidence of impact, care must be taken to replace the product to avoid water absorption to the substrate material.
Whether facility leaders decide on modular furnishings or built-in casework, performance over time can be ascertained by comparing test results of the work surface material. When a solid-surface material or a high-pressure, laminate work surface is selected without accessing test results, it can result in dulling surface gloss, surface etching (e.g., milky surface appearance) and a reduction in surface appearance over time.
Up-front due diligence including access to ASTM laboratory results for resistance to chemical substances and resistance to abrasion will ensure meeting facility requirements of functional and aesthetic performance over time in addition to meeting the patients' expectations.
Design professionals can contribute further in meeting hand-hygiene goals by providing hand-sanitizing amenities within sight lines and nurses' process flow. This has been documented to improve frequency of use and increase hand-washing compliance.
Collocation of hand-washing stations in nurse work areas often warrants splash guards to eliminate water droplet contamination of surrounding high-touch surfaces. Eliminating splashes on surrounding hard-surface flooring also meets another patient safety goal by eliminating slippery conditions that can contribute to falls.
Guaranteeing the integrity of surface seams and joints includes specifying products with test results that meet the requirements of dimensional stability with exposure to heat or humidity, the strength of the bond to the substrate and at adjacent material connections (e.g., edge to edge), and surface thickness that provides the required surface area for adequate sealant coverage to reduce water absorption.
Review of material performance through the characteristic of dimensional stability reveals that high-pressure laminate will change dimensions with changes in environmental humidity, thus impacting seams over time. This is an important consideration for facilities located in coastal regions. Up-front discussions with manufacturers' representatives regarding sealants for optimal seam integrity over time is recommended for meeting the facility's infection prevention goals and expectations of performance over time.
Meeting staff satisfaction goals can be accomplished by bringing ergonomic solutions and visual comfort to the practitioner work areas. Considerations include height of sinks and surfaces, glare-reducing surface finishes, and medium-range light reflectance values for surface colors. Non–textured wrist blades in addition to comfortable sink heights will contribute to user satisfaction while facilitating ease of cleaning.
Reducing glare in the nurse work areas can be accomplished by accessing manufacturers' gloss ratings as measured by a gloss meter in accordance with ASTM D523. For instance, a surface with a gloss rating of less than 30 (on a scale of 0 to greater than 100) is correlated with an increase in visual comfort and productivity by reducing glare in the environment. A matte surface gloss with a gloss rating of less than 10 is available in solid-surface products as well as high-pressure decorative laminates.
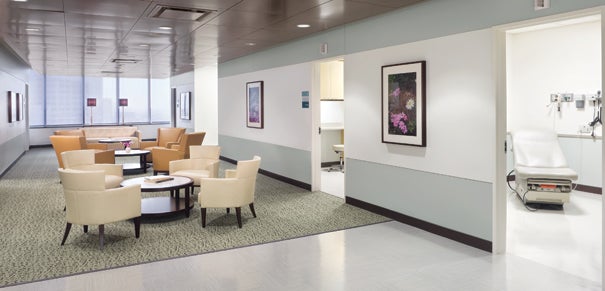
This subwaiting area at Houston Methodist Hospital outpatient center uses a hybrid application of soft- and hard-surface flooring to handle noise and traffic loads.
Selecting flooring colors with light reflectance values of 20 to 40 percent also is recommended for optimal worker comfort with work surface light reflectance values of 30 to 50 percent.
Operating rooms. The most delicate procedures requiring unparalleled focus, concentration and attention occur in the operating room (OR) and other interventional procedure rooms. Yet, specification of environmental conditions correlated with enhanced human performance, such as sound-absorbing materials and nonreflective surfaces, is difficult in the OR.
Rigorous cleaning protocols, prevalence of medical technology and excessive weight loads of medical equipment typically set the priorities in hard and durable material selections. Meeting the four theoretical hospital requirements in this department poses challenges to designers. However, careful consideration of ASTM testing results will help to determine which attributes will meet the facility's priorities.
Because the operating suite is a high revenue-generating space, downtime for product repair is something facility directors do not want to experience. How long are products expected to last? Facility expectations often direct the design professional to a particular classification of products.
To that end, specification for performance over time might be the top priority. Specification for mechanical performance over time in a busy OR setting would entail finding products that can handle known abuses such as heavy static loads, dynamic rolling loads and rigorous cleaning methods.
These expectations can be met by ensuring that products have characteristics such as compressive strength meeting 1,500- to 2,000-pound weight loads, a strong bond to the substrate, seam integrity, dimensional stability, chemical and abrasion resistance, and material thickness. Test results allow the design professional and the hospital to discuss objectively the strengths and weaknesses of products.
Another key goal is reducing noise generated in the OR. Materials containing rubber can help to reduce impact noise from footfalls and falling equipment. Evidence is currently inconclusive if this attribute also reduces leg fatigue.
Will all performance characteristics that address staff requirements be made null and void by issues of weight loads and cleaning methods? Not necessarily. Design professionals can access information on human factors and ergonomics to create environments that are supportive of workers with high cognitive loads.
For instance, paint colors with a light reflective value between 40 and 60 percent can help to make an environment visually comfortable. Provisions of adjacent flooring and other surfaces with gloss ratings less than 30 on the gloss meter rating scale in addition to light reflectance values of 20 to 40 percent for flooring colors will reduce the amount of glare.
Selecting surface textures that are conducive to cleaning protocols is important. Easy removal of bodily fluids with water and detergent is the first step for subsequent disinfection protocols to be effective, according to the CDC's Guidelines for Environmental Infection Control in Health-Care Facilities. Additionally, surfaces must withstand disinfection protocols.
Selection of a material that does not contain organic components and will not provide a food source for microbes is imperative. Resinous, liquid-applied flooring offers integral seamless flooring by virtue of the mode of installation. Other appropriate flooring products include solid rubber and homogeneous sheet vinyl.
Maintenance of tight joints within the flooring material is essential to avoid mold growth in the substrate. Flooring choices also should be evaluated according to their ability to form smooth transitions from horizontal to vertical surfaces, to maintain seamless joints within the material over time, and to form a tight bond with the wall surface.
Choosing performance
Product construction, product chemistry and installation methods are crucial to product performance over time, up-front costs and time to market.
All these factors influence success in achieving performance relative to patient safety and well-being as well as work performance and satisfaction.
Establishing performance expectations early can save time and money by considering and evaluating projects objectively to the hospital's key goals in addition to the subjective, aesthetic goals.
Laurie Waggener, IIDA, AAHID, EDAC, is research and evidence-based design leader at WHR Architects Inc., Houston. She can be reached at lwaggener@whrarchitects.com.
Asking the right questions
Asking questions that guide the interior designer to an action that is measurable is crucial in evidence-based design. Most hospitals are interested in surface materials that facilitate the following organizational goals:
- Patient safety, including preventing infections, reducing falls and avoiding medication errors;
- Patient well-being, including enhancing sleep quality, reducing stress, and improving patient and family satisfaction;
- Staff performance and satisfaction, including improving facility attractiveness and cleanliness, and reducing noise and glare;
- Functional performance and aesthetics over time, including making maintenance and repairs easier and less frequent.
By pairing safety, cost and service goals with the age and needs of the patient population, and then leveraging laboratory test results with available design research regarding application of products in the field, design professionals are able to present the best materials to meet hospital expectations.