Maintaining exterior and interior barrier protections
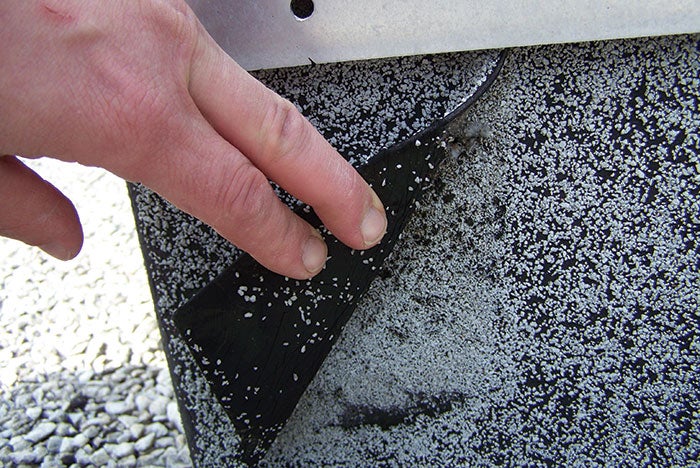
Roof inspections can identify sources of water infiltration, such as de-bonded roof flashing.
Providing safe, high-quality patient care is fundamental to the performance of a hospital or other health care facility. While patient care teams and protocols are foremost in meeting objectives for patient care, privacy and satisfaction, these objectives only can be fully realized in a facility that maintains appropriate environmental conditions in every space to ensure staff safety, operational performance and high-quality results in laboratory environments.
The building enclosure encompasses a critical boundary separating outside and inside environments as well as boundaries separating interior spaces with different environmental conditioning and contaminant-control requirements. Air tightness, vapor-flow control and thermal efficiency, coupled with HVAC design and interaction with the enclosure, are critical to meeting these patient care and facility performance objectives.
Symptoms and diagnoses
Early investigation and analysis of the symptoms of building enclosure issues are fundamental to developing cost-effective and efficient solutions. Common signs and symptoms of water infiltration problems include staining of cladding, walls and ceiling finishes. Even a visible silver dollar-size stain is indicative of greater damage behind the scenes, such as an issue at the window or curtain-wall system, roof or roof drain.
Moisture collection on fenestration systems (i.e., condensation) is another common problem. Depending on the weather conditions in which it occurs, this sign can be significant in determining the cause. It might be traceable to HVAC interaction with the facade, layout of thermostats and other HVAC controls, or improper installation of window blinds or furniture placement, which can result in blocking heat flow to the fenestration.
Patient complaints about comfort are also symptomatic of problems in the building enclosure or HVAC system performance, especially if there is a consistent trend. For example, patients may complain repeatedly that the space is too hot or cold, stuffy, drafty or damp.
In all of these scenarios, the risk of mold growth often is associated with moisture problems.
Facilities professionals can gather evidence and narrow the range of possible sources on their own by digitally photographing a stain and tracing possible sources to their origins; for example, by removing a dropped-ceiling panel to examine pipes or going up on the roof to determine if a ceiling stain aligns with a roof drain. If there is no immediately obvious cause, they can photograph and log the incident, clean the stain and recheck to see if it comes back.
You may also like |
Inspecting hospital building envelopes |
Resilient health care design |
2017 Hospital Construction Survey |
|
Note that water from roof and plumbing leaks can travel far from the sources. When the results of the internal investigation are included in a request for proposal, or even in informal discussion beforehand, it saves contractor or consultant time and associated fees by enabling them to narrow the scope of work. In turn, it contributes to developing the most efficient, cost-effective solutions.
Professionals whose facilities are due for a new roof or replacement roof may consider installing an electric field vector mapping (EFVM) system, which is a noninvasive method of electronic leak detection that pinpoints breaches in the roof membrane by tracing the flow of an electric current across the membrane surface. If the current is interrupted and the system is connected to an alarm system, it can alert the facilities professional to walk the roof with a handheld device to pinpoint the source of the leak.
Although there is a slight upcharge for an EFVM system compared with other detection technologies like electric capacitance meters and infrared cameras, the life-cycle cost avoidance can be considerable, particularly in a facility with a concrete roof deck, which might have to be torn up, or a vegetative roof that would need to be cleared to trace the leak source as a crack, say, 20 feet away.
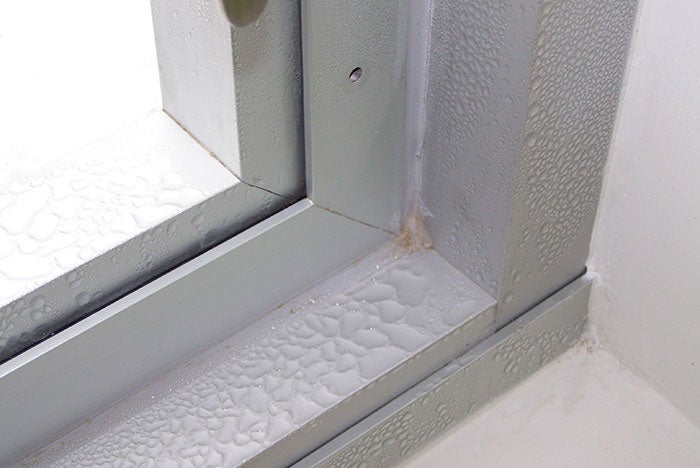
Window condensation may be caused by HVAC interaction with the facade, layout of HVAC controls or improper installation of interior finishes and furnishings.
When performing in-house investigations, facilities professionals must be sure that the surrounding space has been contained properly before opening a ceiling or wall panel. As a health care facility, the same rules of contaminant control and air tightness and control apply to this space and investigative process as they do to a construction project.
For example, facilities staff should wait until a patient room has been vacated, then seal door cracks and air supply and return ducts, and provide a zippered access door. Then they can negatively vent the space to the exterior with a portable contaminant-control system that is properly filtered and directed well away from building air intakes.
If it is an open space, such as a waiting room, it can be sealed using a plastic wall with a zippered door, and portable contaminant-control HVAC systems can be used following the mold and contaminant control guidelines of the Environmental Protection Agency and authorities having jurisdiction. Appropriate signage should be used to control access, and appropriate protective clothing and gear should be worn. Then, appropriate cleaning methods should be used before the space is reoccupied.
When safety methodology is in doubt, facilities professionals should call a consultant. Depending on the issue or the size of the facility, a consultant can perform a localized forensic assessment or a full-condition assessment. They also may perform a localized assessment combined with a building- or campuswide walk-through. The advantage of looking beyond the localized issue is the potential to identify trends that suggest the need for a phased plan for full-scale system repairs, upgrades or replacements.
Facilities professionals also should remember that free inspection services often are provided by manufacturers; in the case of many roofing systems, for example, they also may be required under the warranty. The facilities professional and administrative team should have a list of dates for pre-warranty expiration and expected life of all enclosure systems entered in an integrated calendar software program or an automated work order system so that these critical walk-through and visual surveys will be performed and documented for better maintenance planning.
Timely in-house investigations and inspections and, when necessary, assessments by a building enclosure consultant not only contribute to the development of cost-effective, efficient solutions to building enclosure problems, but also reduce the risks to patient care and facility performance. In addition to visual observations, a consultant may use various tools in the investigation, including tracer smoke testing to examine unintended air flows and air leakage paths; infrared thermography to review thermal inefficiencies, including thermal bridges and air leakage paths; and 2-D and 3-D thermal analysis.
Two major risks
Roofing, terraces and other zones of horizontal waterproofing comprise one of the major risks of water infiltration because they receive the most direct volume of rainwater. Because the roof is not accessed as often as patient rooms and interior spaces, staff have less opportunity to observe issues before they become problems. Moreover, vegetative roofs and terraces with pavers, where the waterproofing membranes are not readily visible, may have hidden damage.
An EFVM system helps to identify leaks in all of these systems. To avoid a significant failure, facilities professionals should perform walk-throughs of all roofs at least once a year to identify roofing that needs repair or replacement, and complete these projects as soon as possible. New roofs should be walked with the manufacturer’s representative and installer six months before expiration of warranties for labor and materials.
Sealants also play a critical role in maintaining water and air tightness. Although redundant waterproofing and flashing may help to control water that gets behind sealed joints in building materials, failed sealants can be an initial source of entry. The sheer number of linear feet of sealant also makes them a high-maintenance risk. Failure may not be readily detectable because it may be as small as a pinhole or a localized area of de-bonding from enclosure substrates at a level that is not readily accessible for a close inspection.
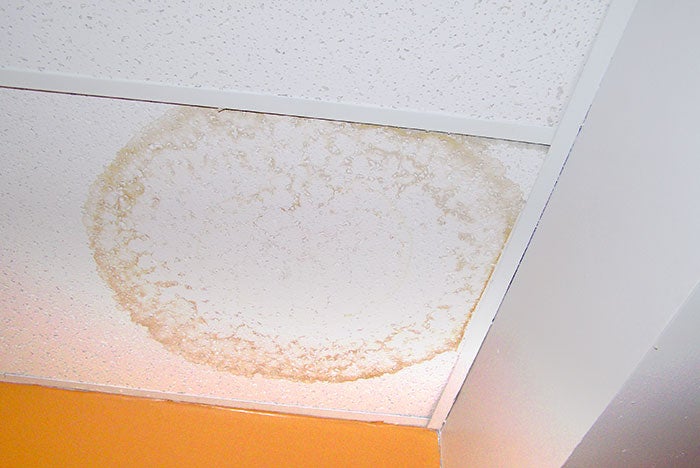
Sources of infiltration can be traced to their origins by removing a stained ceiling panel to find the source.
To increase the potential to detect these penetrations, facilities professionals should perform a careful visual scan every two years, using binoculars and taking care to respect occupant privacy. They also should inspect several elevations every five years using a personnel lift, swing-stage scaffolding or similar equipment to verify that sealants are still performing.
Based on survey findings, the financing required for sealant replacement should be budgeted a year or two before the end of the estimated remaining lifespan. This avoids the higher cost of widespread failure.
Finally, a survey of any system by a consultant or contractor should include a report that identifies short-, mid- and long-term solutions, an estimate of the remaining life span of the product, and projected repair or replacement costs.
Reducing the risks
In addition to conducting regular inspections and immediately repairing any potential problems, the following measures also may help to reduce risks:
- Condensation risk can be reduced by preventing thermal bridging between building system components and by ensuring good HVAC flow. Condensation risk also is reduced, especially in cold or humid climates, by allowing space between furniture and fenestration and by installing window blinds/shades to allow for air circulation when they are closed. These steps prevent stagnation of air flow and associated buildup of moisture load in the air.
- The risk of contaminant buildup can be reduced if the HVAC system cycles provide adequate air changes per hour, and contaminant buildup is also reduced by well-placed localized exhaust systems in critical labs and similar spaces.
- Prefabricated fenestration systems for curtain walls and
- other fenestration systems that may have a shadow box or spandrel panel condition often are a better alternative to site-built systems in environments that have high humidity in spring, summer and fall months, but have a winter season that is much colder. Prefab systems are built in a climate-controlled environment, avoiding the risk of “built-in” moisture that eventually condenses in colder months when the temperature within the spandrel or shadow box drops below the dew point. Ironically, this risk is heightened when site-built systems are properly constructed and thus very airtight.
- Seasonal restrictions on construction timing can reduce the risks in certain climates.
Protecting critical boundaries
As the critical boundaries separating outside from inside environments, as well as interior spaces with different requirements, the building enclosure is a vital component of a health care facility that is designed, constructed and maintained to support patient care, staff safety and operational performance.
Effective design and construction verified by peer reviews and inspections by a qualified building enclosure consultant and third-party commissioning agent are fundamental to ensuring the performance of these systems in new facility construction, expansions and major renovations.
Similarly, timely inspections, maintenance, repair and replacement of these building systems by the owner and facilities staff, supported by qualified contractors and enclosure consultants, are fundamental to reducing condensation and thermal risks and associated problems, and ensuring that a health care organization fulfills its mission.
Paul Totten, P.E., LEED AP, is vice president for building enclosures in WSP USA’s Arlington, Va., office. He can be reached at paul.totten@wsp.com.